2023 Excellence in Environmental Engineering and Science® Awards Competition Winner
Superior Achievement
Category Entered: Operations/Management
Subsea Containment System that Captures the Longest Running Offshore Oil Spill in US History
Entrant: Couvillion Group Engineer in Charge: Matthew Couch, P.E. Location: Gulf of Mexico, Mississippi Canyon Block 20 Media Contact: Dillon Hoffmann
Entrant Profile
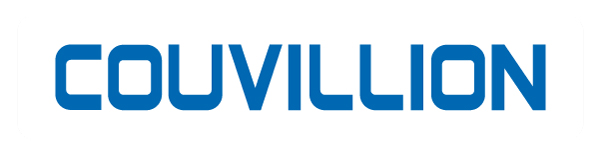
Louisiana's Belle Chasse based Couvillion Group is based out of Belle Chasse, Louisiana and specializes in providing marine construction and salvage, port and vessel maintenance services, emergency response, and disaster recovery for the oil and gas industry. Since 2005 Couvillion Group has excelled at tackling tough challenges with smart and unrivaled results. As a key first responder in the Plaquemines Parish vessel recovery effort after Hurricane Katrina in 2005, Couvillion designed a unique lift and barge system that returned hundreds of vessels to service.
Following the catastrophic BP oil spill associated with the Deepwater Horizon incident, the Couvillion group successfully deployed and managed marine equipment, vessels, personnel, and logistics during the extended cleanup effort. The company was acknowledged to be a high-quality service provider while working with BP, the U.S. Coast Guard, National Park Services, and local government during this period. Most recently Couvillion Group has worked with the United States Coast Guard to successfully contain the longest running offshore Gulf of Mexico oil spill in U.S. history.
Project Description
Twelve miles off the coast of Louisiana a low probability high consequence event occurred in September of 2004 during Hurricane Ivan which resulted in a producing oil and gas platform being toppled over in approximately 460 ft of water and dragged off station approximately 600 ft. Twenty-eight oil and gas well conductors were buried beneath the mudline and have continually been discharging oil and gas into the Gulf of Mexico since the incident occurred.
In November of 2018, the United States Coast Guard partially federalized the worksite and solicited proposals to design, build, install and operate a system to capture the ongoing release of oil at the site. The subsea rapid response system (RRS) that was proposed, designed, built, installed, and operated by Couvillion Group included a subsea collection device that was clamped to a structure suspended off the jacket leg directly above four hydrocarbon plumes. The collected hydrocarbons are routed to a patent pending subsea three phase separator that separates the oil from the water and gas. Oil is sent to subsea oil containment vessels located on top of the jacket and offloaded via hydraulic pump monthly to a surface vessel where the crude is then transported to shore and recycled.
Since the system became operational in 2019 over 1,200,000 gallons of oil with less than 1% water has been safely collected and recycled from the site which would have otherwise been discharged into the Gulf of Mexico. With the dome placed directly above the hydrocarbon plumes, the oil, water, and gas enter the dome which is approximately 5’ off the seabed and flow upwards into the separator. Oil continues to flow upward into the oil storage containers displacing water in the storage tanks back into the environment through vent lines which extend down to a depth below the dome level. Water and gas in the separator are discharged back into the seawater. On a periodic basis the oil collected in the subsea oil storage containers is pumped to a surface vessel using a submersible pump and then oil is taken to shore for recycling.
While working on an emergency response campaign safety is of paramount importance and integral to a projects success. This project was a great example that how a projects success was predicated upon good safety practices, procedures, and safe working practices in a hazardous environment. Over a span of 131 bell runs and a total offshore campaign duration of 1,704 hours the safety protocols and procedures implemented on this emergency response campaign proved to be highly effective. On all projects safety is the first and highest priority, especially on a fast-tracked emergency response campaign.
The offshore campaign was broken down into six basic packages of work as shown below:
- Site clearance and riser section removal
- Installation of strongback clamps, oil storage container clamps and porch clamps
- Installation of porch assembly on strongback
- Installation of 42” diameter separator
- Installation of 72” and four 48” oil storage containers
- Installation of 4” hoses and demobilization
On February 22, 2019, the vessel mobilization began, and the job was completed with vessel headed back to shore on April 29, 2019. Over two hundred tons of equipment were over boarded one time and installed without incident.
To meet the compressed schedule four different engineering firms were involved in the evaluation and design of the system components shown below.
Fabrication was divided between five Louisiana fabricators. All major components were transported using barges on Louisiana waterways and assembled onshore to for test fit up. Comprehensive Inspection test plans were developed and signed off by senior representatives of all parties involved (ie. Prime Contractor, Engineering firm, Fabricator, Installation Contractor and USCG.)
In addition, full-scale testing of the separator was conducted to verify performance. The test facility utilized air compressors to simulate gas, mineral oil, water, storage contains and pumps to completely simulate the separator in the installed configuration at the site offshore.
Installation of the RRS required extended saturation diving at depth, heavy lifts, and hook up of large heavy components, and hose assemblies with associated valving. Detailed procedures, story boards, Hazids, toolbox talks, and JSEA’s were required to successfully assembly this system safely and efficiently. Detailed installation procedures were followed with appropriate sign- offs.
World class IMCA diving safety standards were enforced at all times during the installation work and decompression of the divers. Over the course of this campaign with 135 bell runs for the divers at 8 hours per bell run) there were zero safety incidents, and the job was a complete success from a safety, operational, and environmental standpoint.
The offshore campaign was broken down into six basic packages of work as shown below:
- Site clearance and riser section removal
- Installation of strongback clamps, oil storage container clamps and porch clamps
- Installation of porch assembly on strongback to jacket legs along with support chains and Dome installation
- Installation of separator
- Installation of 72” and four 48” oil storage containers
- Installation of 4” hoses and demobilization
On February 22nd, 2019 the vessel mobilization began and the job was completed with vessel headed back to shore on April 29, 2019. Over two hundred tons of equipment were installed without incident. This was a fast-tracked emergency response program and from contract award until the system was fully operational took less than six months. From April 12, 2019 through November 2, 2022 there have been over 1.2 million gallons of oil collected and recycled from the site. From aerial overflights and from satellite imagery the reported sheen size areas have been reduced by as much as 99+% as have the number of sheen incidents.
This first of its kind design contributes to the advancement of environmental containment and subsea processing technology. It can be utilized in a multitude of applications such as leaking pipeline, sunken vessels, downed platforms, or other environmental catastrophes where oil is released in the environment. A modularized system has been developed and built for future applications.
Click images to enlarge in separate window.
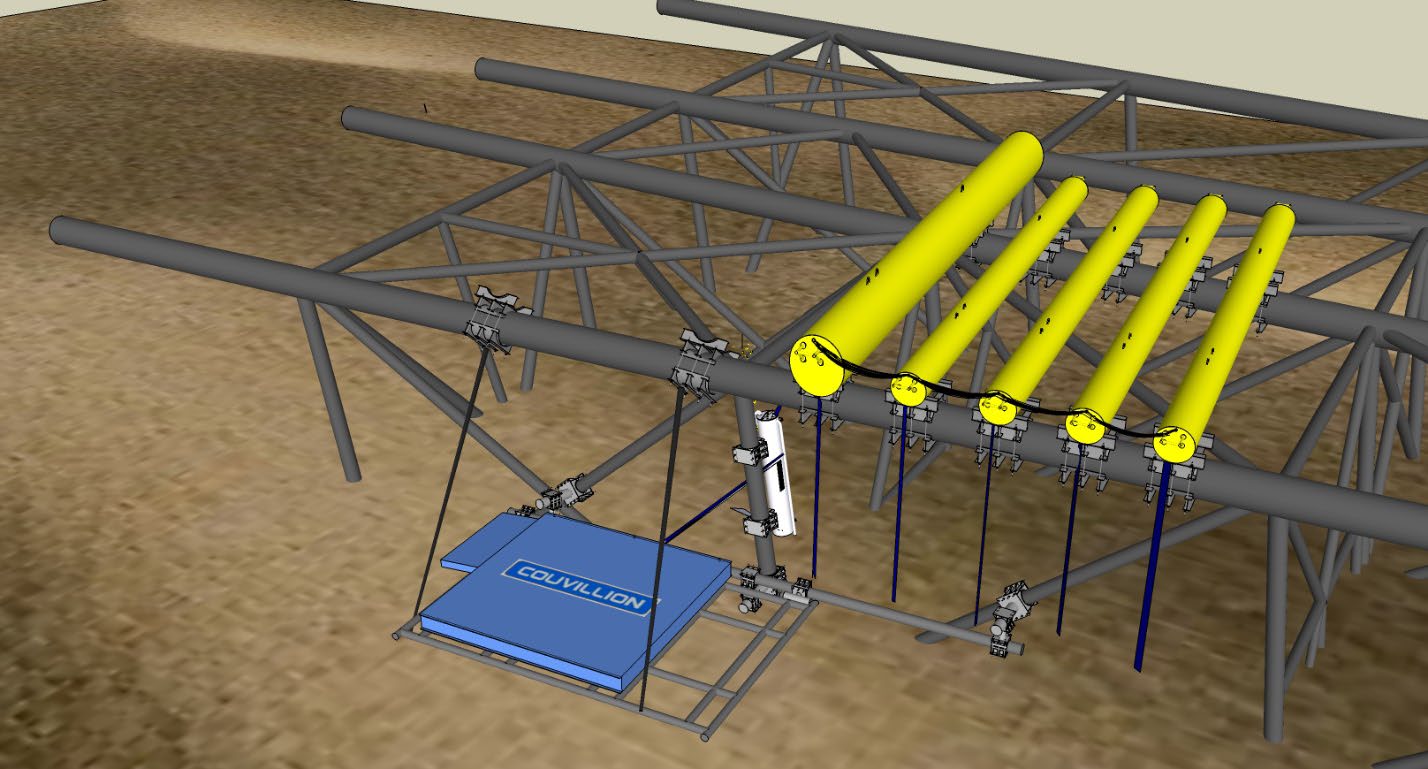 |
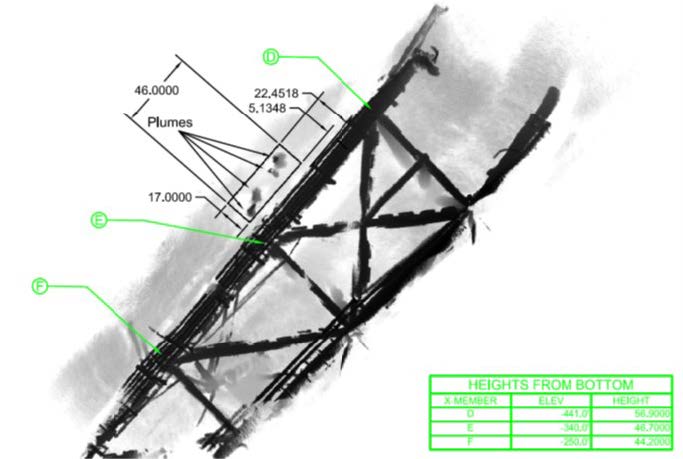 |
Figure 1: Rapid Response Solution System
|
Figure 2: Location and Size of Plumes in Relation to Jacket
|
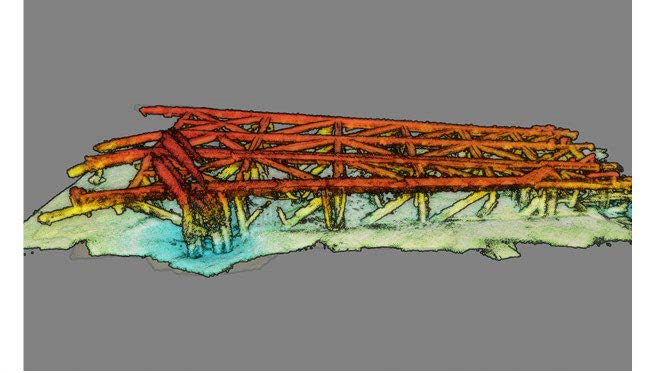 |
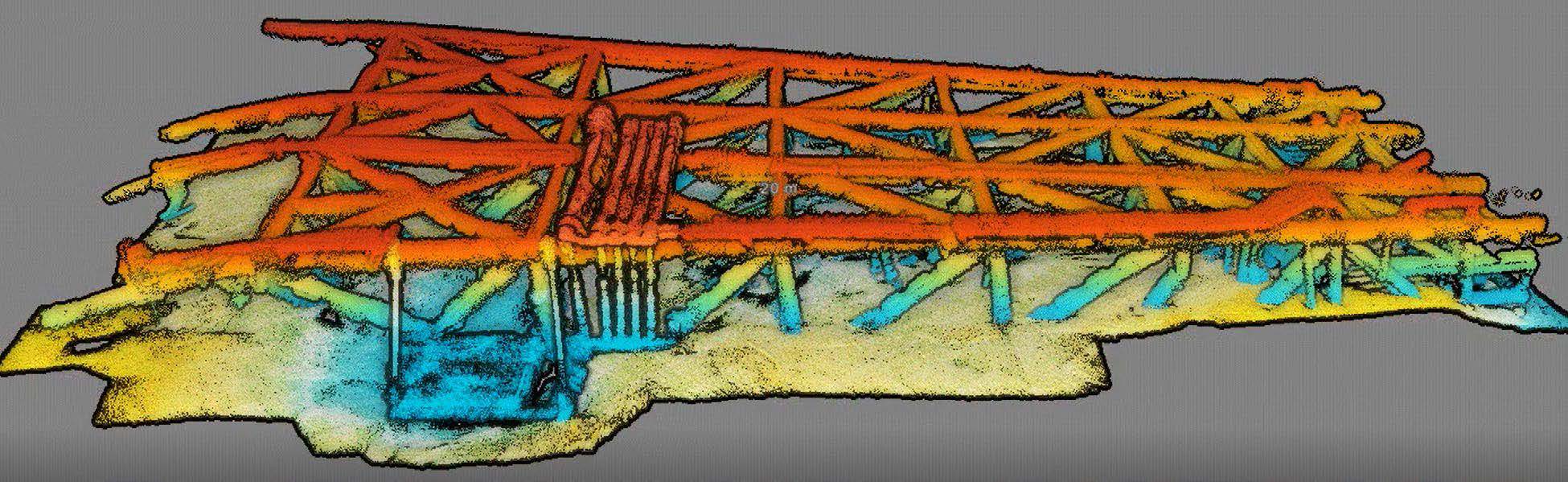 |
Figure 3: Echoscope Image of the downed jacket before the RRS was installed showing oil and gas plumes.
|
Figure 4: Echoscope Image of the down jacket after the RRS was installed showing oil and gas plumes contained by the porch and dome.
|
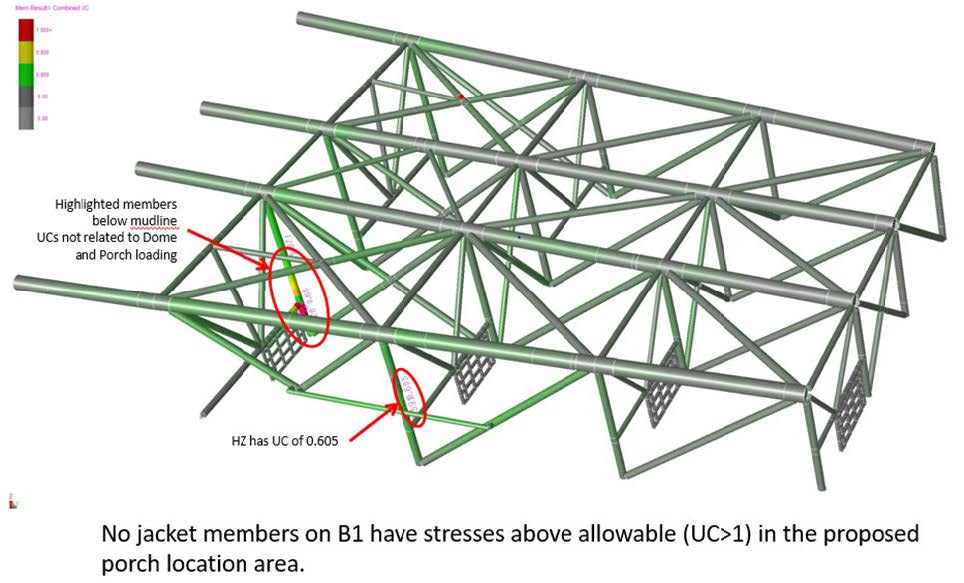 |
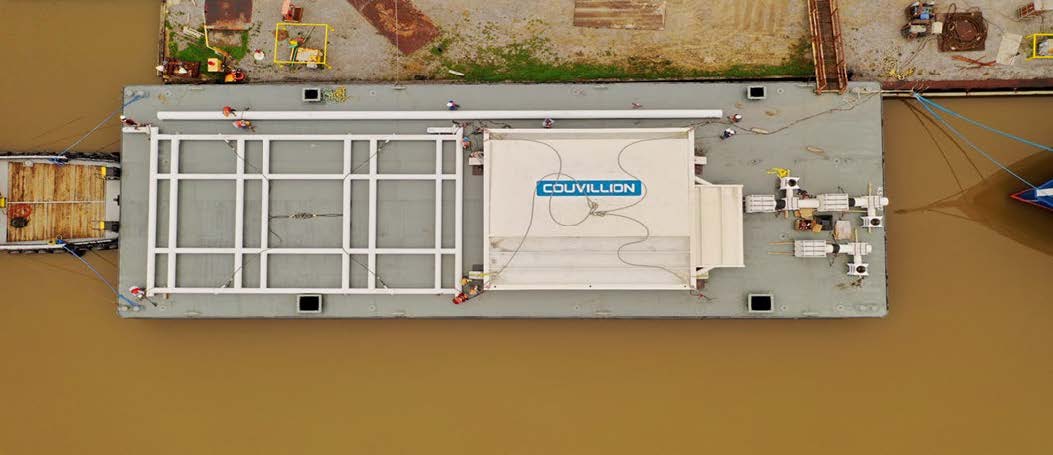 |
Figure 5: Structural Assessment preformed on the downed platform that analyze allowable stresses proposed on the porch location area.
|
Figure 6: Major system components shipped via barge in Louisiana waterways ahead of offshore transport.
|
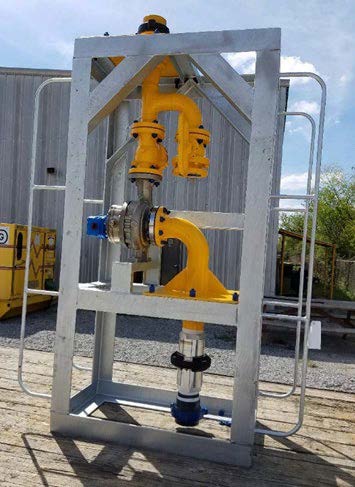 |
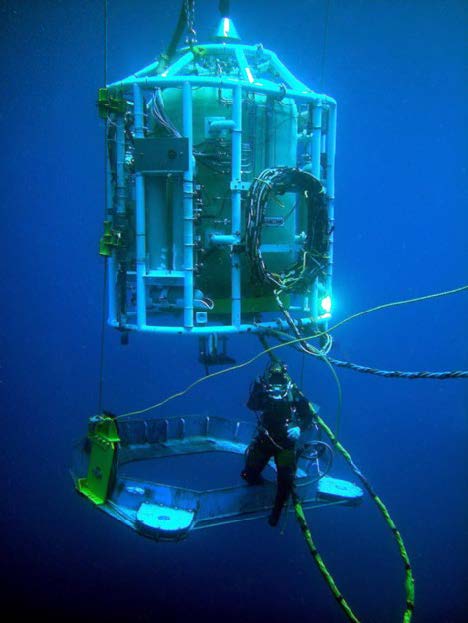 |
Figure 7: Subsea Pump System Vertical Orientation
|
Figure 8: Saturation Diver on Location
|
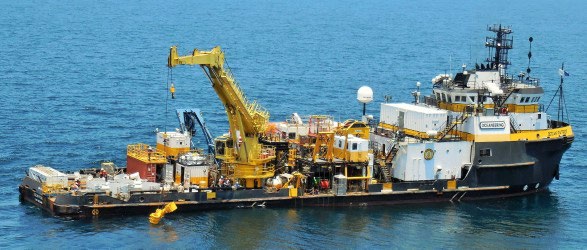 |
|
Figure 9: DSV Ocean Patriot with saturation divers in the water offshore over boarding equipment for installation.
|
|
|