2023 Excellence in Environmental Engineering and Science® Awards Competition Winner
Grand Prize - Design
A Headworks Divided - The Key to Unlocking Expanded Water Reuse in Orange County, CA
Entrant: Orange County Sanitation District in Partnership with the Orange County Water District Engineer in Charge: Shahrzad F. Namini, MSc., PMP, P.E., VM Location: Huntington Beach, California Media Contact: Kelly Newell; Shahrzad Namini
Entrant Profile
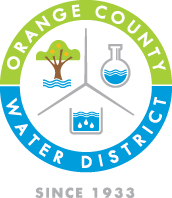
The Orange County Sanitation District (OC San) is a special district governed by a 25-member Board of Directors comprised of 20 cities, four special districts, and one representative from the Orange County Board of Supervisors. OC San provides wastewater collection, treatment, and recycling for approximately 2.6 million people living within a 480-square-mile area of central and northwestern Orange County, California (CA). Our facilities include 388 miles of sewer pipes, located throughout the county. Together both plants currently treat around 180 million gallons per day (mgd) that is sent to our two treatment plants: Plant No. 1 in Fountain Valley and Plant No. 2 in Huntington Beach, CA.
OC San committed to a goal of being 100% reclaimable which meant that we needed to figure out a way to get our effluent flow from Plant No. 2 in Huntington Beach to Plant No. 1 in Fountain Valley and the Groundwater replenishment System. With the work of OC San and the project team, OC San was able to send water from Plant No. 2 to GWRS on time and under budget all while keeping our 24/7 facility running.
Project Description
Background
Orange County Sanitation District (OC San) operates a vast wastewater collection system that ultimately converges to a single point at the headworks facility at treatment Plant No. 2 in Huntington Beach, California (Figure 1). This unique location makes the headworks one of the most critical water pollution control facilities in the state. Continuous and reliable operation of the 317 million-gallon-per day (mgd) headworks is paramount to protecting the coastal environment, public health, and the regional economy.
Nearly a decade ago the Orange County Water District (OCWD) began planning expansion of the nearby Groundwater Replenishment System (GWRS). To facilitate the expansion, OCWD needed more source water from OC San, which could only come from Plant No. 2. However, Plant No. 2 processes industrial flows that are considered “non-reclaimable” and would have to be managed through separate treatment than the GWRS bound flows. The problem was everything mixed in the single headworks facility, and building a new facility was cost and land prohibitive.
The key to unlocking this critical resource was finding a way to physically split the facility into two separate treatment trains. But how could this be completed without jeopardizing the operation of this critical facility?
The solution was the P2-122 project: a complex project delivered on time and below budget, even though construction began in February 2020 at the beginning of the COVID-19 pandemic. The success of the P2-122 project is a testament to the skill, dedication, and leadership of OC San, its employees, consultants, and contractors in unlocking a drought resistant water supply for generations to come.
Integrated Approach
The integrated approach started with the partnership between OC San and OCWD. Both agencies recognized the value of water through the entire life cycle and worked to maximize its benefit. This partnership resulted in OCWD funding the $30 million project through its successful efforts to obtain a low interest rate loan from the U.S. Environmental Protection Agency’s Water Infrastructure Finance & Innovation Act, while OC San led project administration.
The decision to split the headworks was also a decision to embrace sustainability. Instead of abandoning relatively new assets and building an expensive new system, the existing system was modified, resulting in lower costs to ratepayers, reduced construction impacts, and reduced use of resources.
Complexity
Specific work elements demonstrating the complexity of the project include:
Separating Gates and Diversion Pipe
The project physically separated the headworks by installing 17 new large stainless steel slide gates in constrained areas (Figure 2). This work required extensive confined space entries to confirm the design dimensions for the new gates.
The project also included a new 75-inch diversion pipe, which had to be installed 30 feet below grade in a highly congested utility corridor adjacent to the critical facilities (Figure 3). This required a complex shoring system, custom steel fittings, and challenging wall penetrations through 36-inch thick concrete walls.
PLC Split
With the headworks separated, the system controls had to be modified. The complexity of this task was amplified because the existing programmable logic controller (PLC) was already at capacity. Therefore, a new PLC had to be provided and the program split between the two systems. This change required running the entire headworks manually while the new system was installed.
Construction Sequencing
The project team developed a detailed sequencing plan with hundreds of steps, one of these steps is presented in Figure 4. The sequence had a major benefit of avoiding a full facility bypass, a high-risk, high-cost operation which was thought to be unavoidable during the planning phase.
Originality and Innovation
The team deployed multiple innovative approaches to execute the project, including:
Pumping Divergent Flows
With the headworks split, the flows on each side are substantially lower, which would have caused problems with the existing pumps. This issue was resolved by replacing some of the existing large pumps with smaller pumps (Figure 5) custom engineered to provide a large flow range and fit in the existing space.
The tradeoff to providing the smaller pumps was a decreased wet-weather capacity. To offset this decrease, an innovative “over speeding” approach was used on the remaining pumps. By testing and reprogramming the large pumps to operate faster, their total capacity was increased by 50 mgd, offsetting the lost capacity from the smaller pumps without expensive replacement of motors and drives.
Optimized Hydraulic Modeling
The modifications altered the system hydraulics and created a risk of adverse hydraulic conditions. Therefore, the project included a physical model of the influent pump station intake. This was supplemented by a computation fluid dynamics (CFD) model that covered the remainder of the facility. By combining CFD and physical modeling (Figure 6), the project team protected the system’s reliability.
Quality
- Several metrics prove the high quality that has been achieved, including:
- Completed over 20 highly complex major facility shutdowns without impacting the continuous operation of the facility.
- Performed pump testing, constructability review, and modeling site visit.
- Current change orders is 4.3% of Construction Contract value of $14.5 millions.
- Beneficial occupancy achieved on December 6, 2022 per contract schedule.
- The hydraulic performance of the separated system was tested during a major rainfall event shortly after commissioning. Flows on the reclaimable side of the facility approach the design capacity of the separated headworks. (Figure 7).
Contribution to Social or Economic Advancement
The project contributes to social and economic advancement by providing sustainable source water to GWRS, which ultimately provides clean and safe drinking water to over one million people. This makes the system essential to the health and well-being of the community. This water source also requires less energy for transmission and treatment than many alternatives, resulting in a lower carbon footprint and improved air quality.
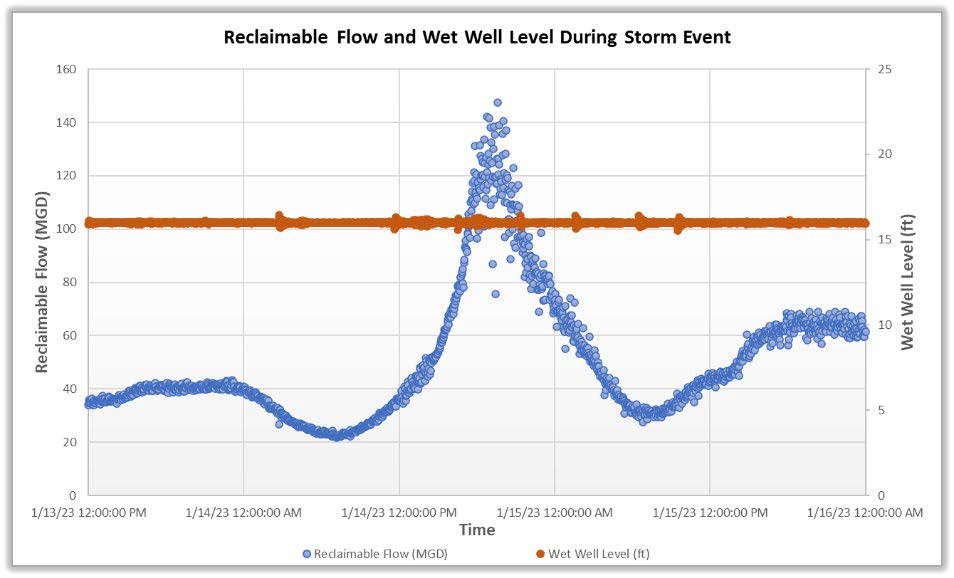
Click images to enlarge in separate window.
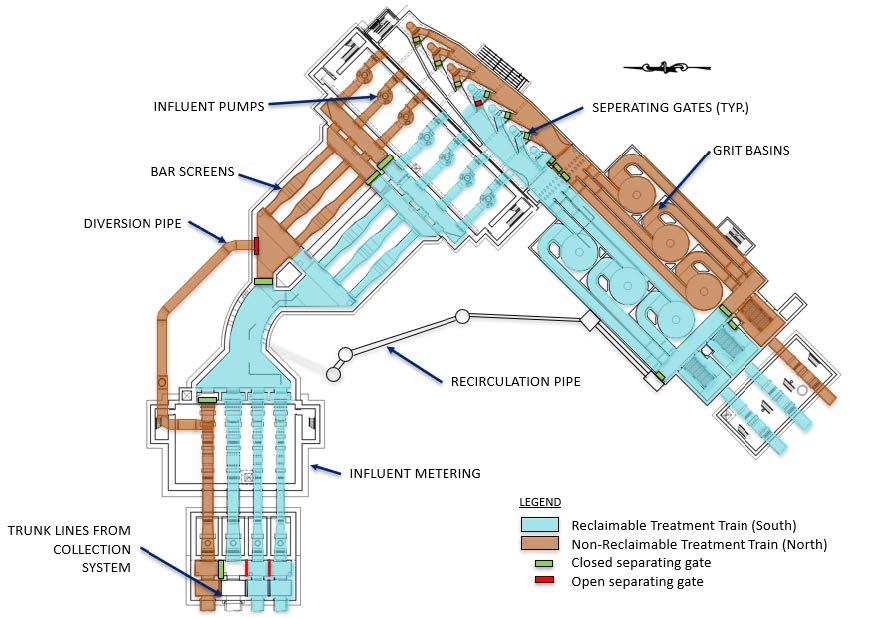 |
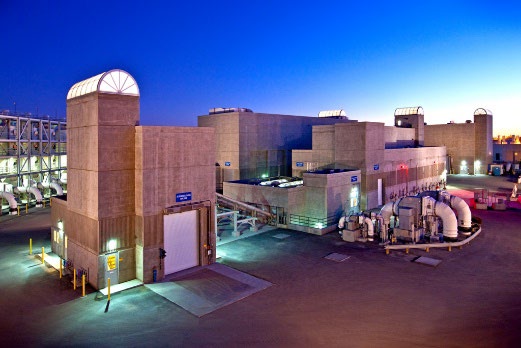 |
Photo 1. Schematic of separated headworks showing major project elements.
|
Photo 2. Exterior view of Plant No. 2 headwork looking towards the bar screen and influent pump building.
|
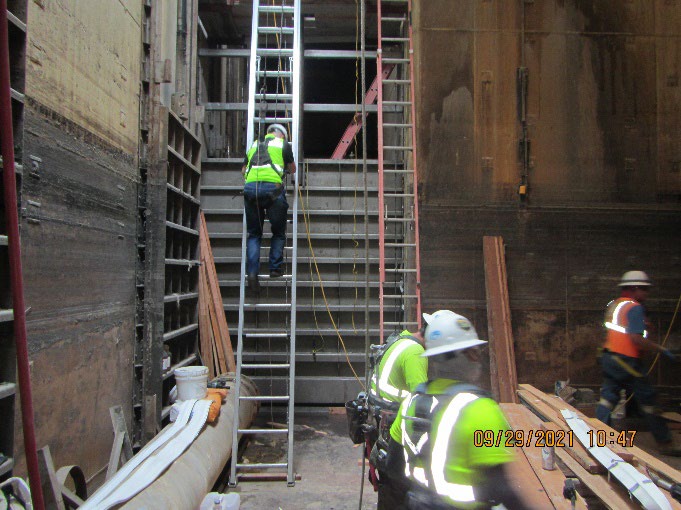 |
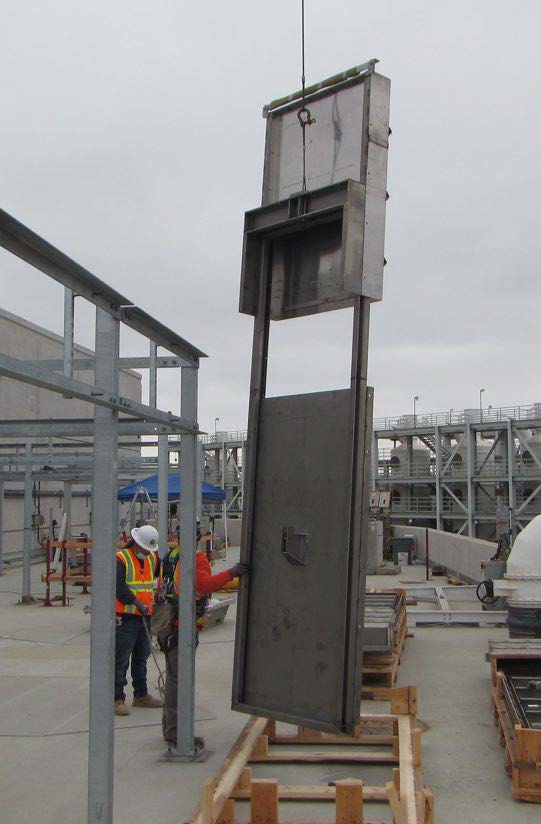 |
Photo 3. Installation of a 10’ x 12’ stainless steel slide gate in the bar screen influent channel. This is confined space work with an active sewage channel opposite the installation.
|
Photo 4. Installation of one of the 4’ x 8’ stainless steel slide gates on the pump discharge channel.
|
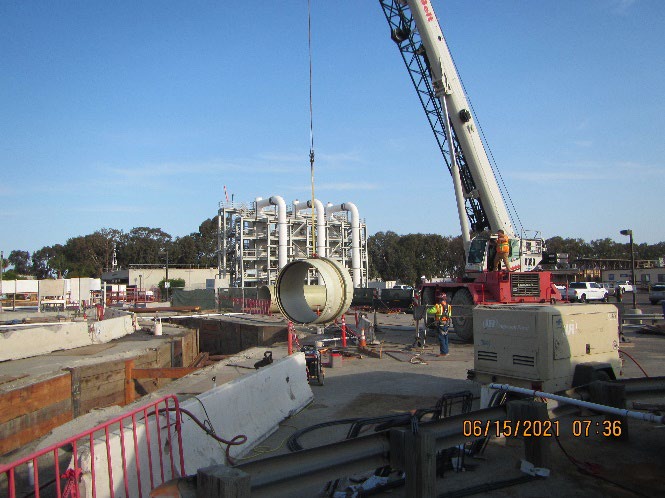 |
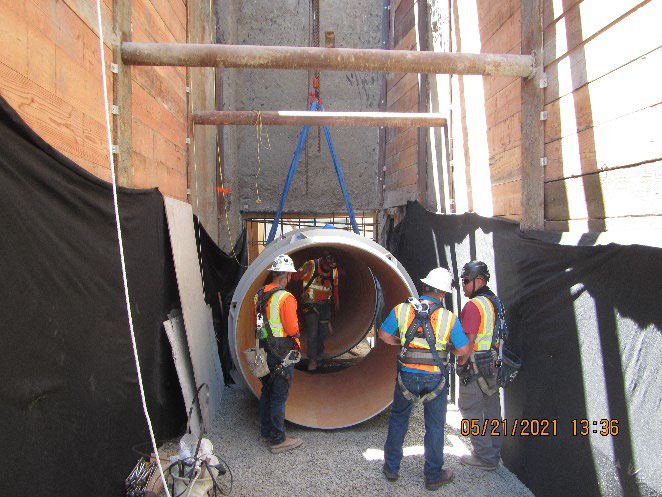 |
Photo 5. Lowering a section of the 75-in diversion pipeline into the trench.
|
Photo 6. Workers installing a section of the 75-in diversion pipeline at the bottom of the 30-ft deep shored excavation directly adjacent to the bar screen channel.
|
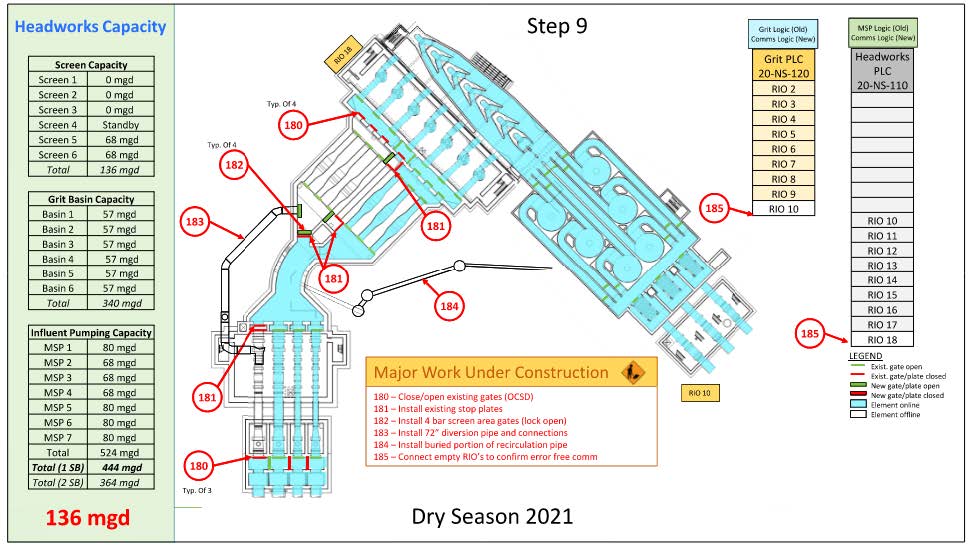
|
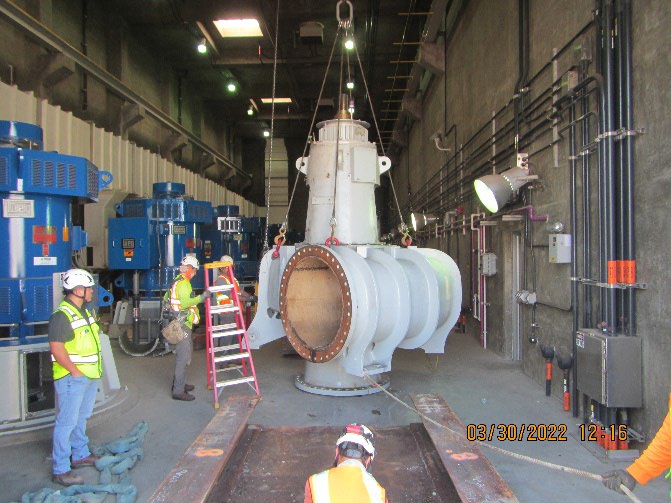 |
Photo 7. Example of the detailed construction sequence developed for the project. The status of each facility is shown, key work steps and available capacity and systems.
|
Photo 8. Workers preparing to lower one of the new low flow pumps down into the pump room. These pumps were custom engineered to fit in the existing space and handle a higher range of flow conditions.
|
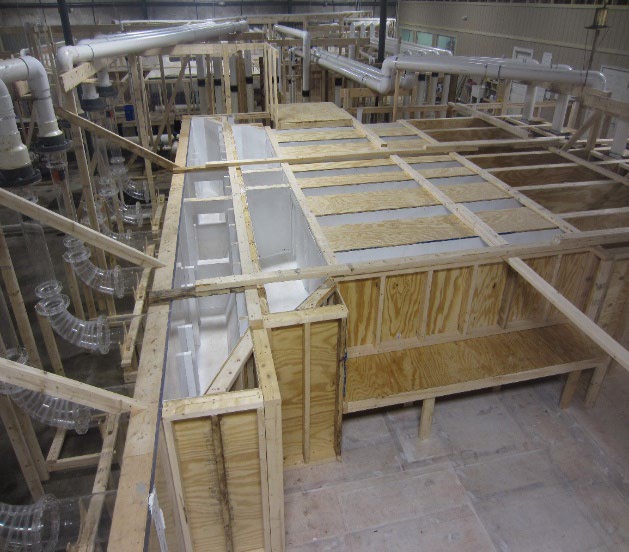 |
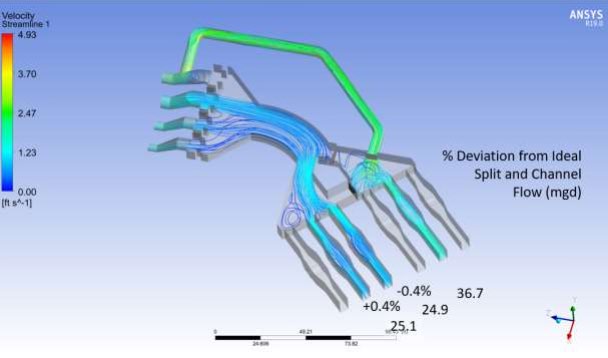 |
Photo 9. Picture of the physical model of the bar screen effluent channel and pump intake. 1:6 model was used to evaluate the intake changes caused by the new gates and pump sizes. The model showed the vortex breaker plates and curtain walls were necessary to maintain adequate intake conditions.
|
Photo 10. Image of output from the Computational Fluid Dynamics model for the area upstream of the bar screens. Using CFD in conjunction with the physical model allowed for comprehensive modeling at reduced cost.
|
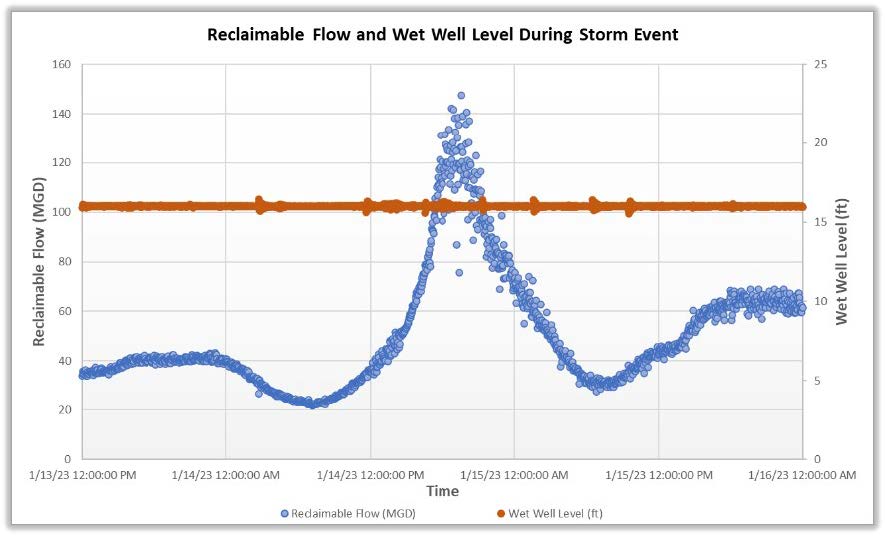 |
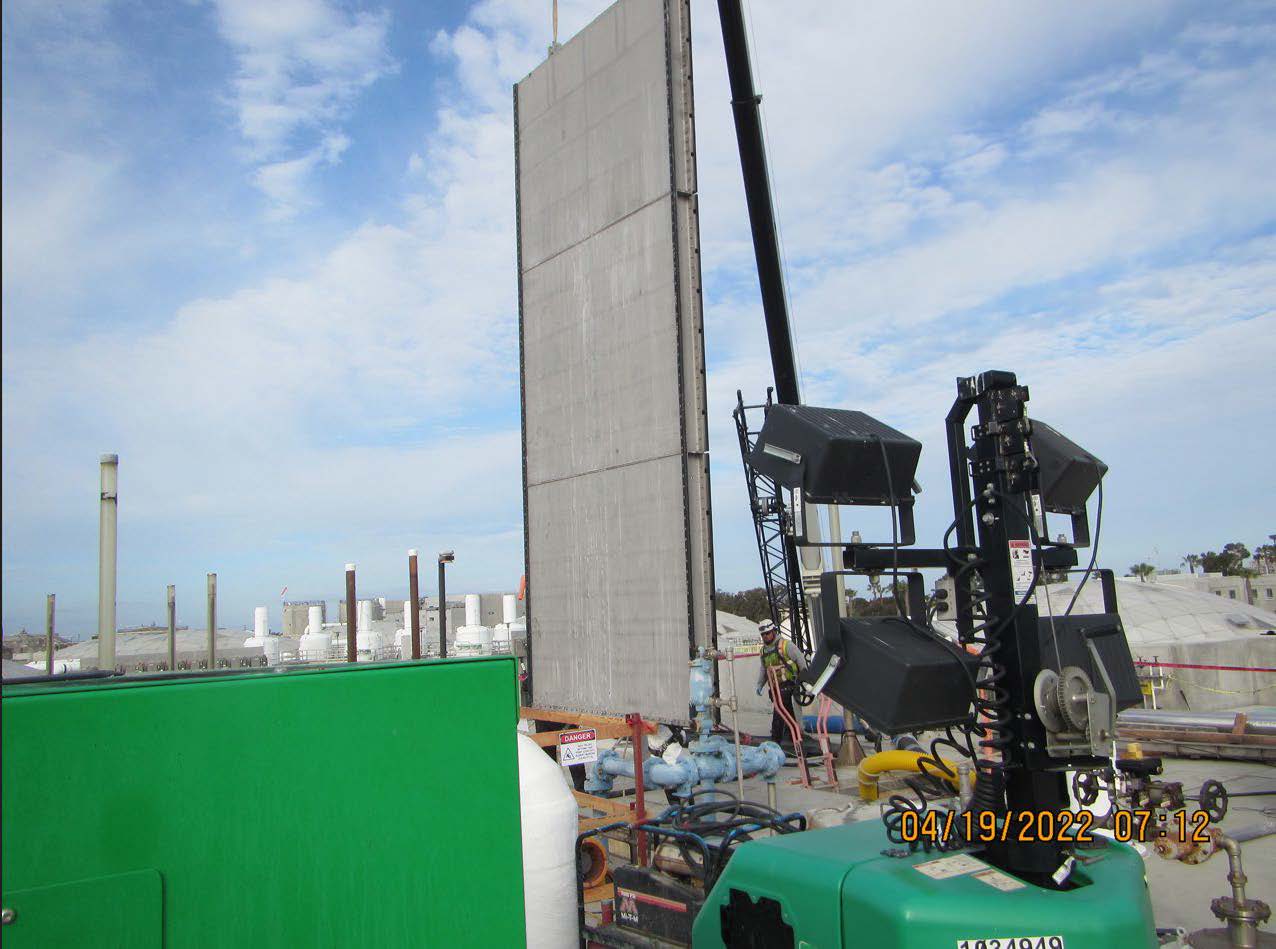 |
Photo 11. Influent flow and wet well level during a high-flow wet-weather event in January 2023. This data demonstrates the performance of the system in separated mode.
|
Photo 12. Installation of a large 25’ x 10’ bulkhead in the grit effluent channel. This system helped keep the system in service and avoid a major bypass.
|
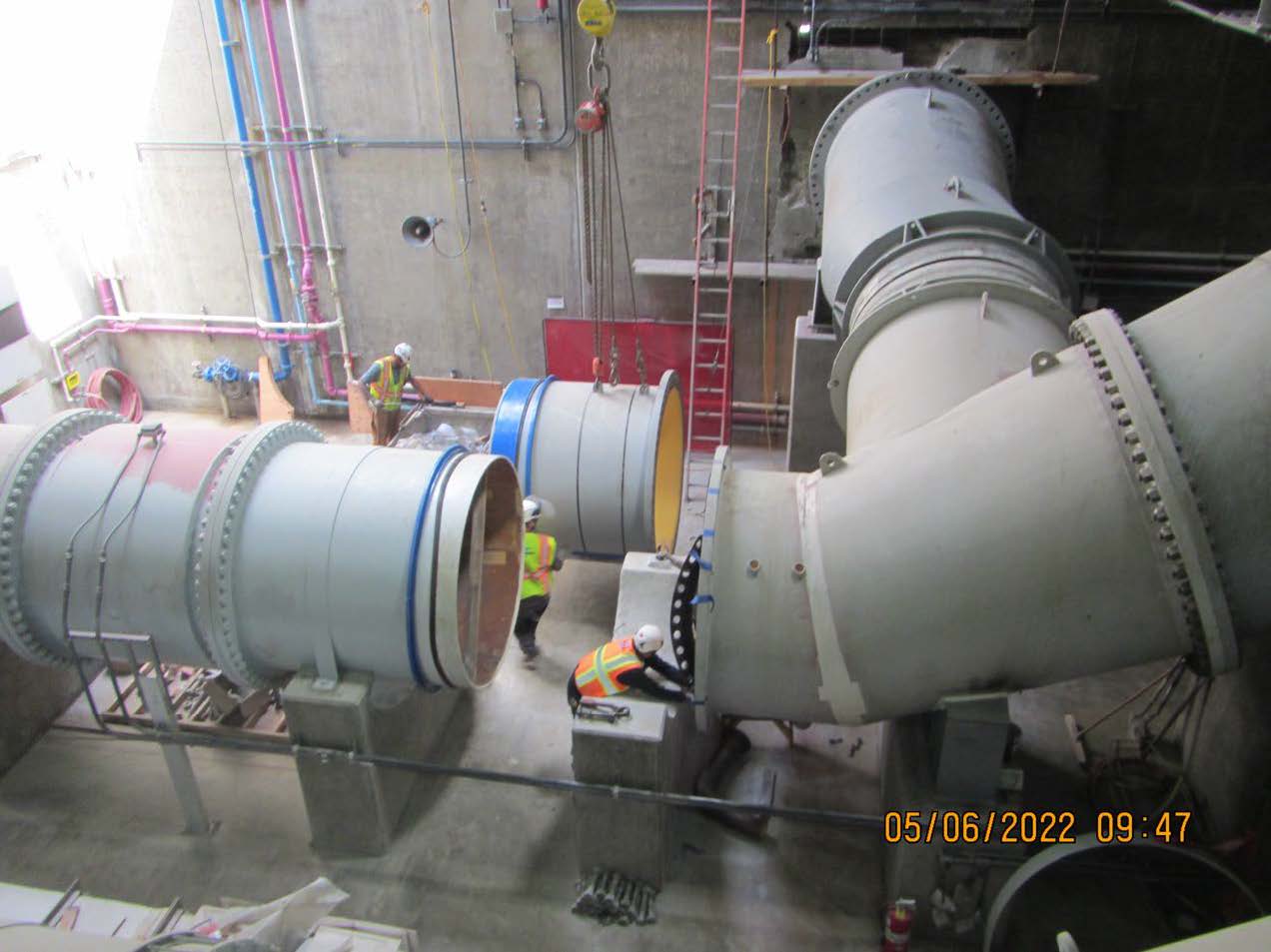 |
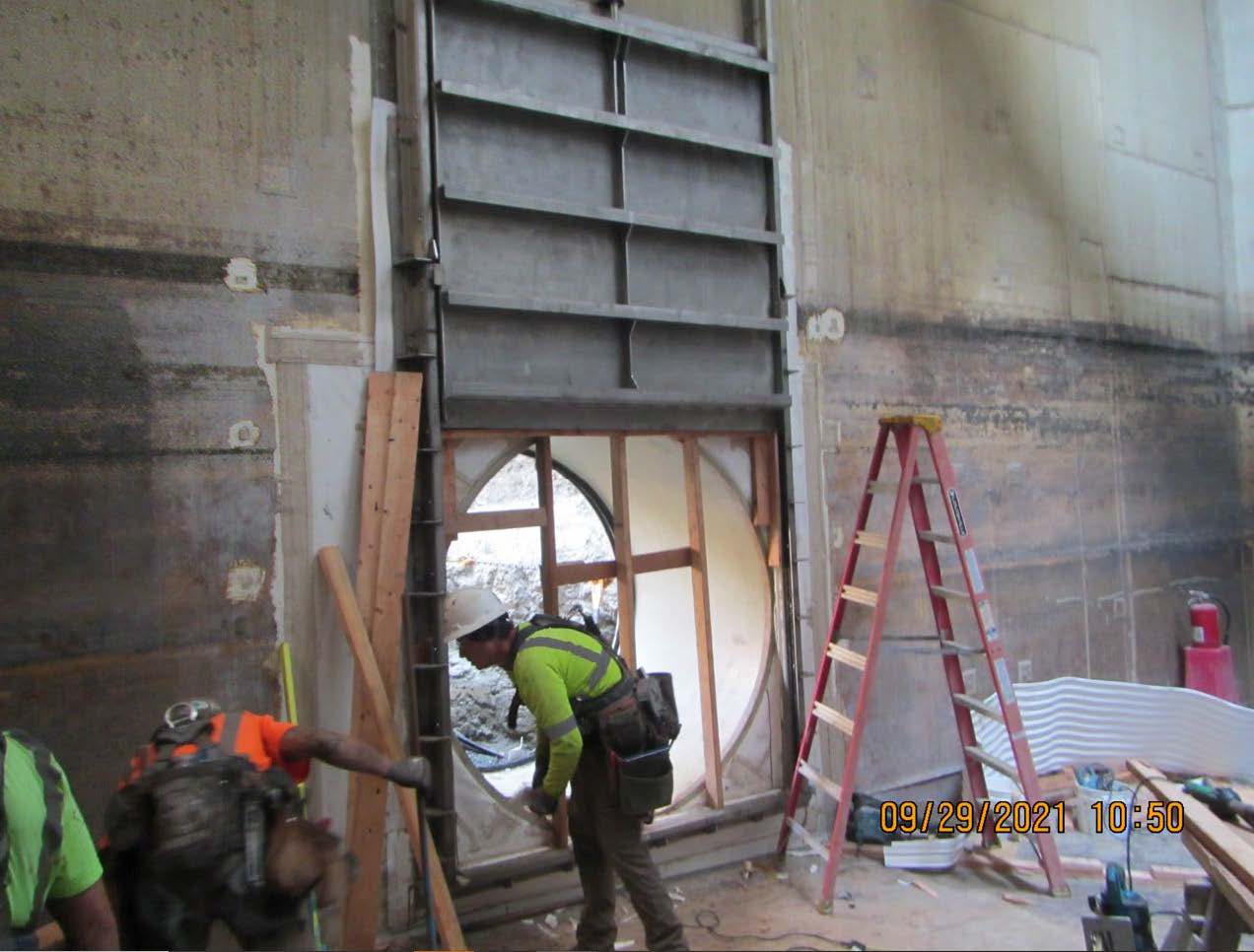 |
Photo 13. Installation of custom steel fittings in the Influent Metering Structure to make the connection to the new Diversion Pipe.
|
Photo 14. Installing the new slide gate at the discharge of the Diversion Pipe. The penetration through the 36-inch concrete wall can be seen in this picture.
|
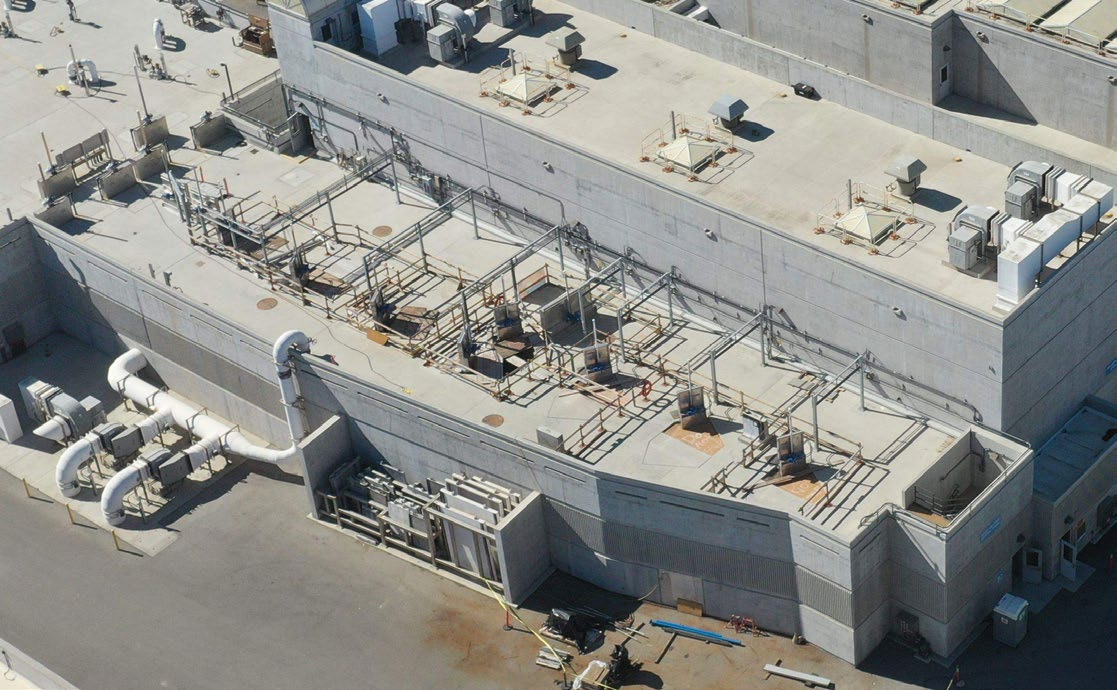 |
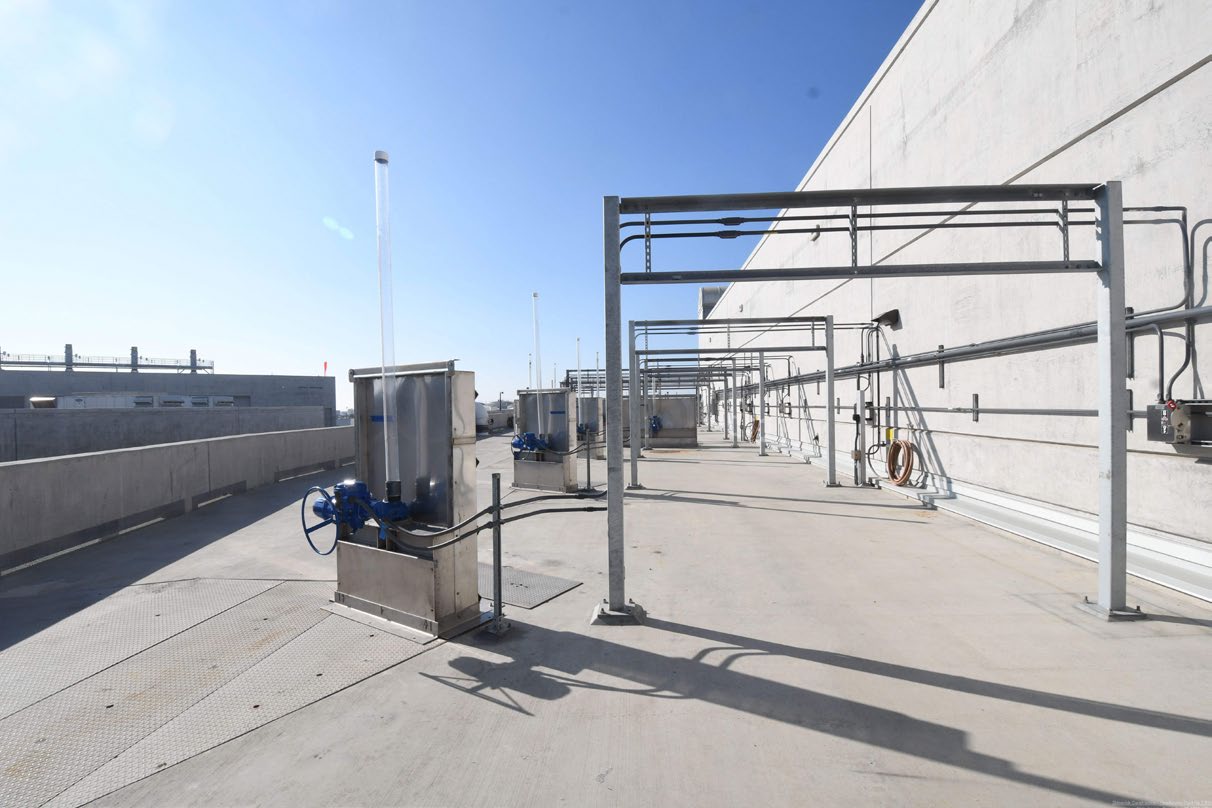 |
Photo 15. Installation of 11 separation gates on the pump discharge channel and grit basin influent channel.
|
Photo 16. View of pump discharge channel and separation gates at the end-of-construction.
|
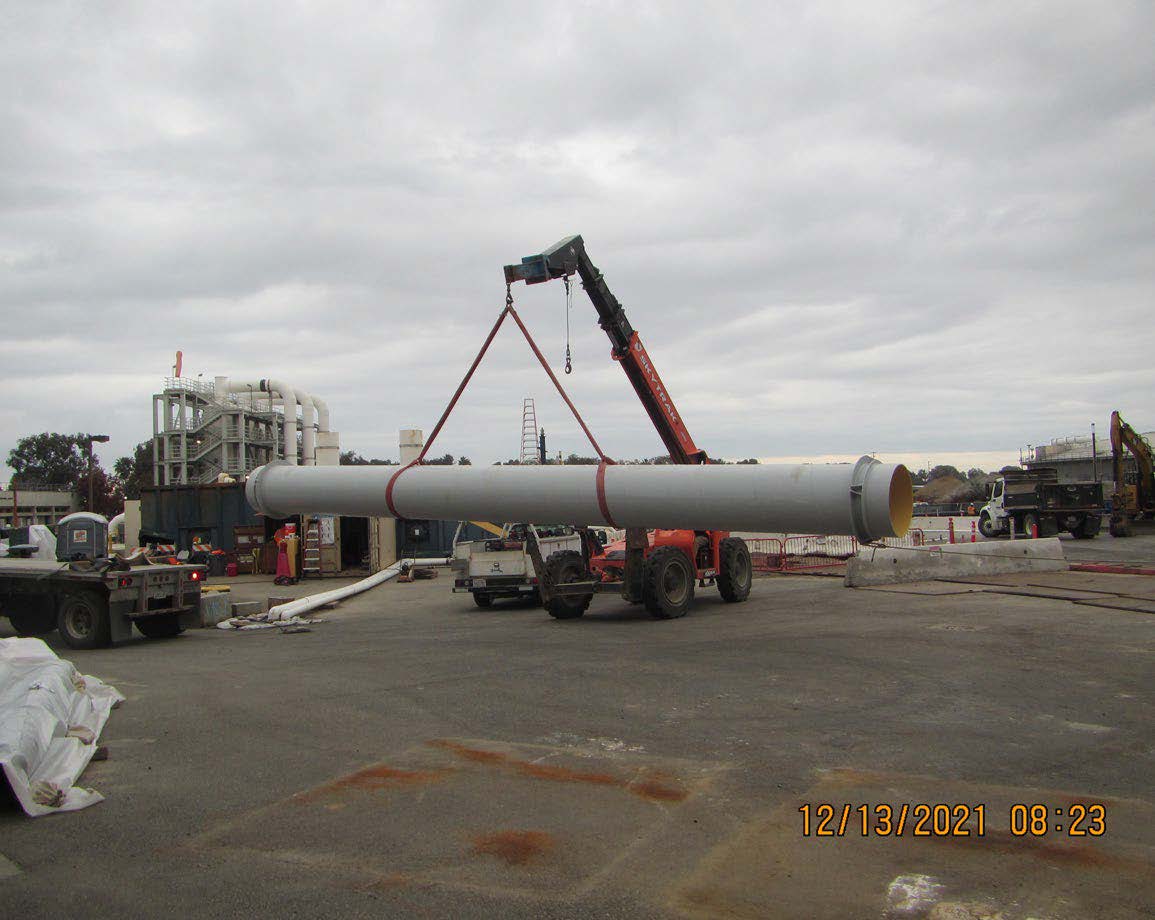 |
|
Photo 17. Preparing to install the Recirculation Pipe, which is another system installed on the project to manage low flow conditions when the headworks is separated.
|
|
|