2018 Excellence in Environmental Engineering and Science® Awards Competition Winner
Grand Prize - Small Projects
MSD Buncombe County, North Carolina - Sanitary Sewage Sludge Incinerator Improvements Project
Entrant: CDM Smith Engineer in Charge: Richard Tsang, Ph.D., P.E., BCEE Location: Asheville, North Carolina Media Contact: Julie Forgas
Entrant Profile
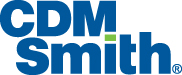
The Metropolitan Sewerage District (MSD) of Buncombe County, serving greater Buncombe County and northern Henderson County in western North Carolina, hired CDM Smith to rehabilitate their existing sanitary sewage sludge incinerator (SSI) at the French Broad River Water Reclamation Facility. The project upgraded the emissions control system to comply with the Environmental Protection Agency (EPA) Maximum Available Control Technology (MACT) provisions of the Clean Air Act by the established March 21, 2016 deadline.
Historically, the standard approach for mercury removal includes a sulfur-impregnated activated carbon adsorber system, but CDM Smith proposed a more cost-effective, safe, innovative and efficient solution - a sorbent polymer composite (SPC) filter system. To implement this novel system, the project team had to move quickly to identify long-lead item equipment that would drive the overall project schedule, working closely to pre-procure items and pre-negotiate pricing for proprietary equipment. Through pilot testing, the SPC system's performance was validated and MSD went on to install one of the nation's first municipal applications of SPC technology. Having achieved mandated emissions limits by the EPA deadline, while saving millions and shaving months off the project schedule, MSD's choice to hire CDM Smith as design engineer for our SSI systems expertise was confirmed.
CDM Smith provided preliminary design, final design, permitting and construction phase services to MSD to deliver this critical compliance project on time and under budget, in partnership with Haren Construction, the general contractor, and Industrial Furnace Company, the air pollution control systems supplier.
CDM Smith provides lasting and integrated solutions in water, environment, transportation, energy and facilities to public and private clients worldwide. As a full-service engineering and construction firm, we deliver exceptional client service, quality results and enduring value across the entire project life cycle.
Haren Construction is fully committed to employee safety. With their safety program and full-time safety manager, they work hard to provide every employee with safe working conditions. Working in the water and waste treatment field, they partner closely with clients to ensure the safety of every jobsite and the public at large.
Industrial Furnace Company (IFCO) is capable of handling all facets of industrial construction. IFCO works with clients from the initial consultation through the installation, all the way to maintenance and repairs to ensure complete customer satisfaction.
Project Description
The Metropolitan Sewerage District (MSD) of Buncombe County, nestled on the banks of the French Broad River, was determined to implement a rehabilitation and improvements project that would meet new EPA standards for sewage sludge incinerator (SSI) air emissions. CDM Smith - who provided preliminary design, final design, permitting and construction phase services - helped MSD implement one of the nation's first municipal installations of sorbent polymer composite (SPC) mercury removal technology, saving millions in public funds and allowing the project to finish ahead of schedule.
Integrated Approach
Exceeding standards for air emissions proves performance. Sampling in advance of the project showed that MSD occasionally exceeded the EPA incinerator emissions standard for mercury. Through pilot testing, MSD and CDM Smith verified the installment of an SPC system, as it was found to remove mercury at an average of 89 percent. After implementation of the system and further optimization, the average mercury removal rate remains high, at 71 percent. This allows MSD to stay well within compliance of the EPA standard.
Lowering contaminated waste disposal volume supports sustainability. The SPC mercury removal system achieves stringent mercury removal requirements with a much smaller volume of material compared to the activated carbon used in an adsorber, leading to a reduction in operation and maintenance expenses incurred in the disposal of contaminated wastes.
Quality
New technology complies with advanced regulations. The upgraded emissions control system complies with EPA's Maximum Available Control Technology (MACT) provisions of the Clean Air Act, having achieved mandated emissions limits by the March 21, 2016 deadline.
Robust SPC drives savings. Ultimately, MSD saved more than $4 million in capital cost, over traditional carbon adsorption technology, and should continue to see high performance and operational savings for years to come through reduced disposal of mercury laden materials, lower power consumption and less complex operating equipment.
Enhancing environment and air quality safeguards community. By meeting the new EPA MACT provisions, MSD has continued their commitment to achieving compliance with regulatory requirements that protect the natural beauty and environment of western North Carolina for MSD's 50,000 customers and many more tourists who visit each year.
Originality and Innovation
Revolutionary technology reduced dangerous mercury levels. Conventional technology typically utilizes sulfur-impregnated activated carbon adsorber systems, which are time-tested but costly to implement and maintain. The chosen vendor's SPC mercury removal process, however, is a true innovation for sanitary SSIs, providing a safer, cost-effective alternative to carbon adsorber systems. This type of system had been used in power plants to achieve air emissions standards, but had not been previously utilized in this type of municipal application for SSIs.
Pilot testing for municipal application ensures success. The innovative SPC technology was pilot tested during the design phase, due to a lack of full-scale municipal application, and demonstrated the capability to meet new EPA emissions limits, with mercury removal rates averaging 89% across five layers of SPC panels during pilot testing.
Proactive procurement achieves a demanding schedule. MSD and CDM Smith used a competitive bid solicitation to pre-purchase the primary heat exchanger. Price and scope were also pre-negotiated with the multi-venturi scrubber and SPC module manufacturer. These approaches contributed greatly to expedited shop drawing preparation and equipment fabrication processes, shaving 4 months off the project schedule and allowing the project to achieve the EPA mandated deadline. This is a true testament to MSD's commitment to being regulatory compliant; many other municipal SSIs were not able to achieve compliance by the MACT deadline.
Complexity
Developing a new solution leads to impressive results. MSD was prepared to implement a conventional carbon adsorber-type system for mercury removal, but also open to innovative approaches which would reduce capital costs and operational complexity while still achieving MACT compliance. In exploring an alternative approach, MSD chose to pilot the new SPC mercury removal technology, even though it challenged the ability to achieve compliance by the EPA deadline. Ultimately, the entire project team collaborated effectively to overcome this hurdle and begin full operation of the system a month ahead of schedule, in December 2015, avoiding additional equipment and unnecessary risks.
Eliminating space constraint issues streamlines execution. Improvements had to be executed within a limited working space inside the existing incinerator building. Working directly with the equipment manufacturer for the multi-venturi scrubber and SPC system, MSD and CDM Smith devised a solution that implemented both systems in the same vessel, eliminating the need for additional ductwork and fluidizing air blower improvements to convey the flue gas. This reduced capital costs and operational complexity.
Social and Economic Advancement
Ensuring air quality and safety for generations to come builds partnerships. Exposure to mercury can result in serious neurological problems and other health issues. These incinerator improvements are helping protect Buncombe County residents and visitors by drastically reducing mercury emissions. In addition, worker safety is upheld by avoiding the risks of operating additional heat exchangers and carbon vessels. The team was also able to defer the potential need for caustic addition, a highly reactive chemical, to a later date if needed to maintain emissions compliance.
Novel approach passes the savings onto ratepayers. By implementing innovative technology to remove mercury via the SPC modules, capital cost savings of more than $4 million and annual operations and maintenance cost savings of several thousand dollars can be passed on to MSD's customers. This cost savings was crucial since no federal funding or assistance was made available.
Producing less disposable waste solves for the future. The smaller SPC mercury media, compared to that of activated carbon adsorption, results in less waste and a more sustainable solution for both MSD and the Buncombe County community.
Leveraging CDM Smith's SSI expertise, MSD managed and completed a large scale rehabilitation project, even when faced with an aggressive timeline imposed by the EPA. This project is a shining example of how embracing advances in technology - through piloting verification - can provide cost-effective solutions to achieving regulatory compliance and lasting environmental, social and economic benefits to the community at large.
Click images to enlarge in separate window.
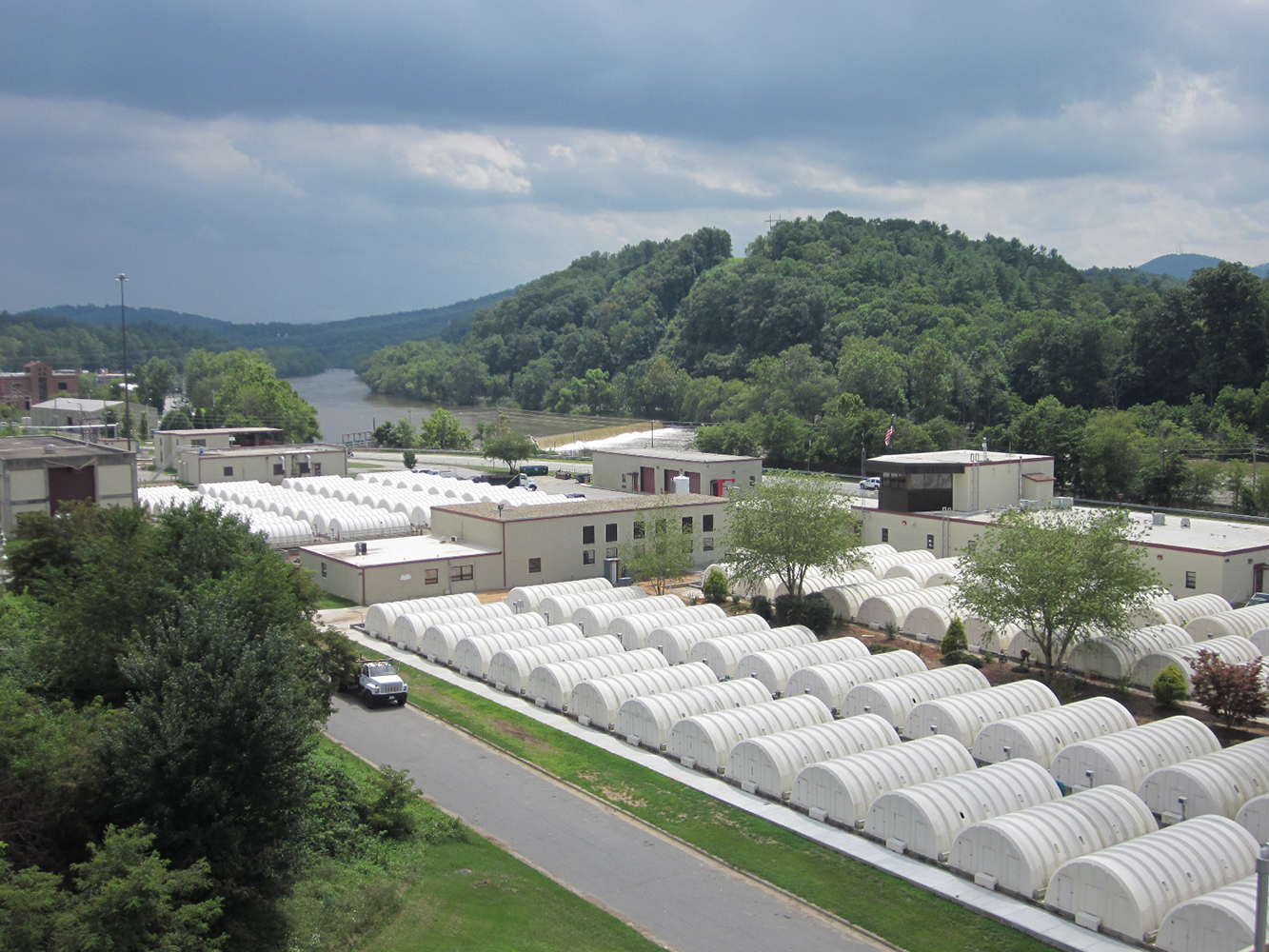 |
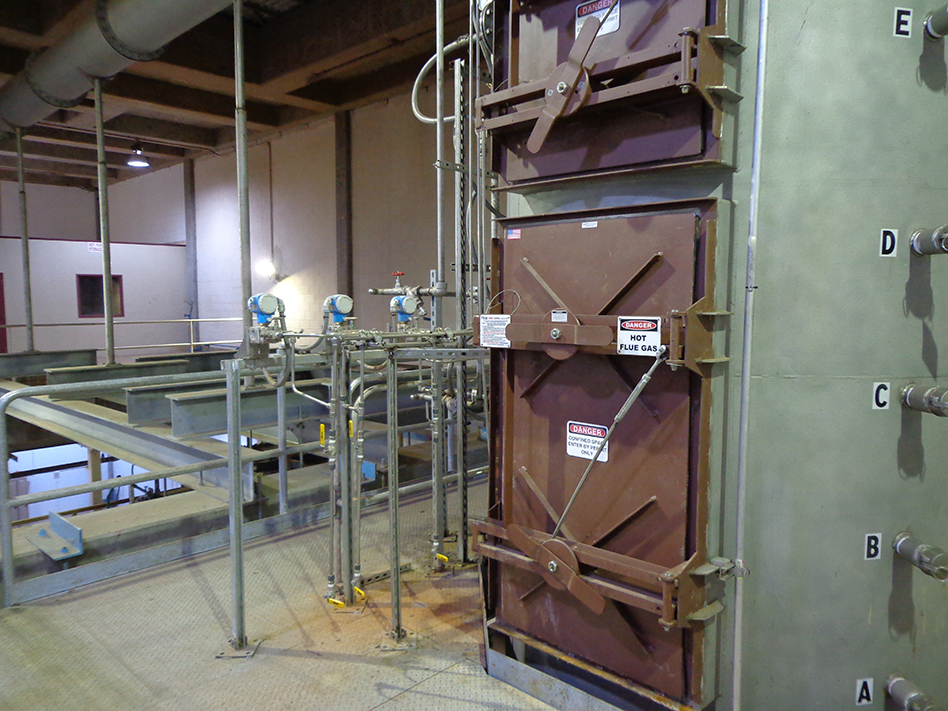 |
Photo 1: On the banks of the French Broad River, in a county that takes sustainability seriously, the MSD water reclamation facility is home to many unique technologies including one of the largest rotating biological contractor systems in the world, as well as one of only three facilities in North Carolina with a fluidized bed sanitary SSI.
|
Photo 2: The innovative SPC technology, added to MSD's air emissions control system, achieves EPA regulatory criteria, reduces contaminated waste disposal and saves $4 million in construction costs - which is crucial since no federal funding or assistance was made available.
|
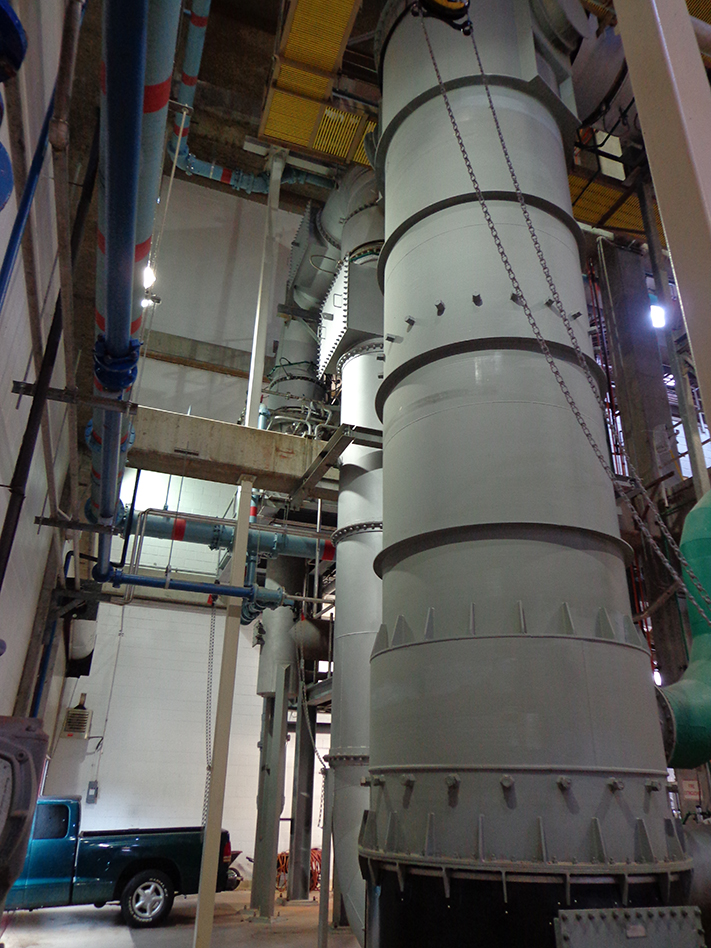 |
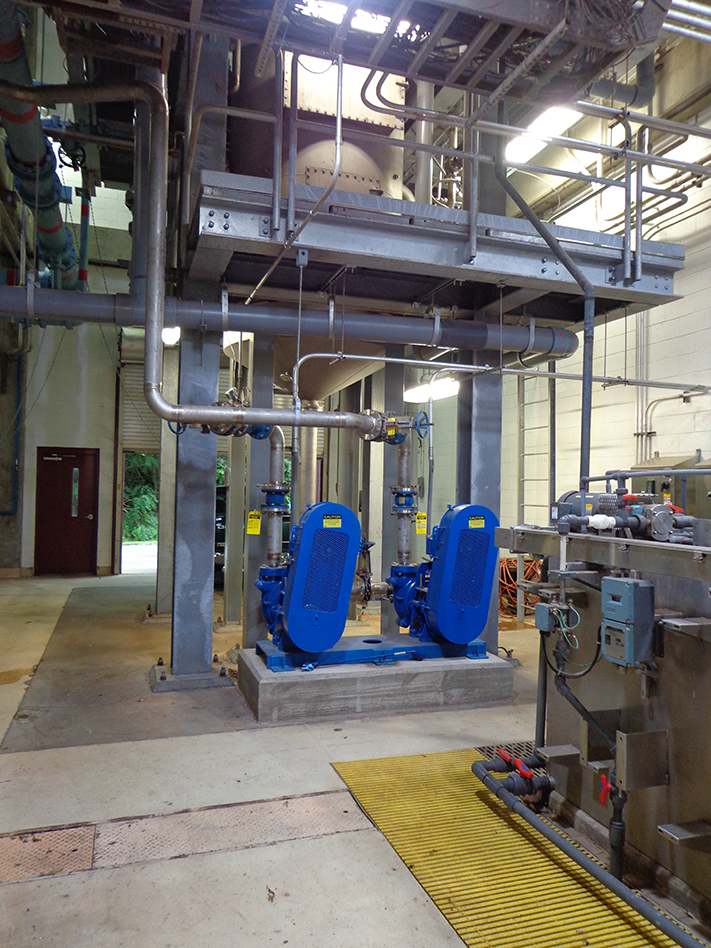 |
Photo 3: In addition to installing new treatment equipment, this project replaced the existing primary heat exchanger for heat recovery to maintain the incineration process. CDM Smith and MSD coordinated to pre-purchase this key equipment in keeping with the EPA regulatory deadline.
|
Photo 4: The multi-venturi scrubber system - for primary scrubbing of the flue gas from the SSI - was installed to replace the existing single tube venturi and tray scrubber, reducing operations and maintenance requirements and construction cost, while ensuring future flexibility.
|
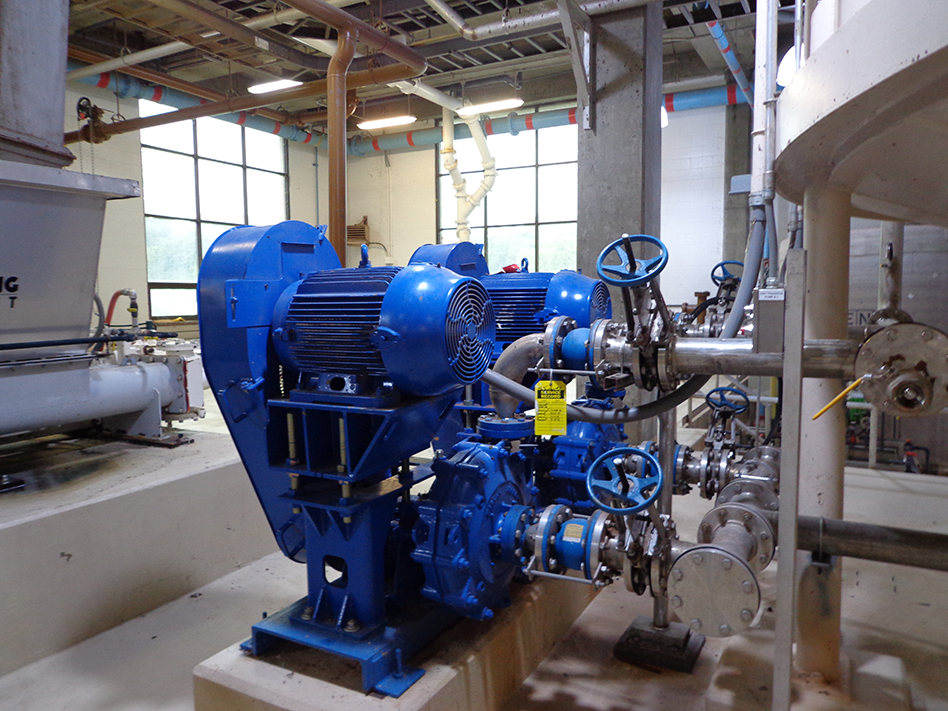 |
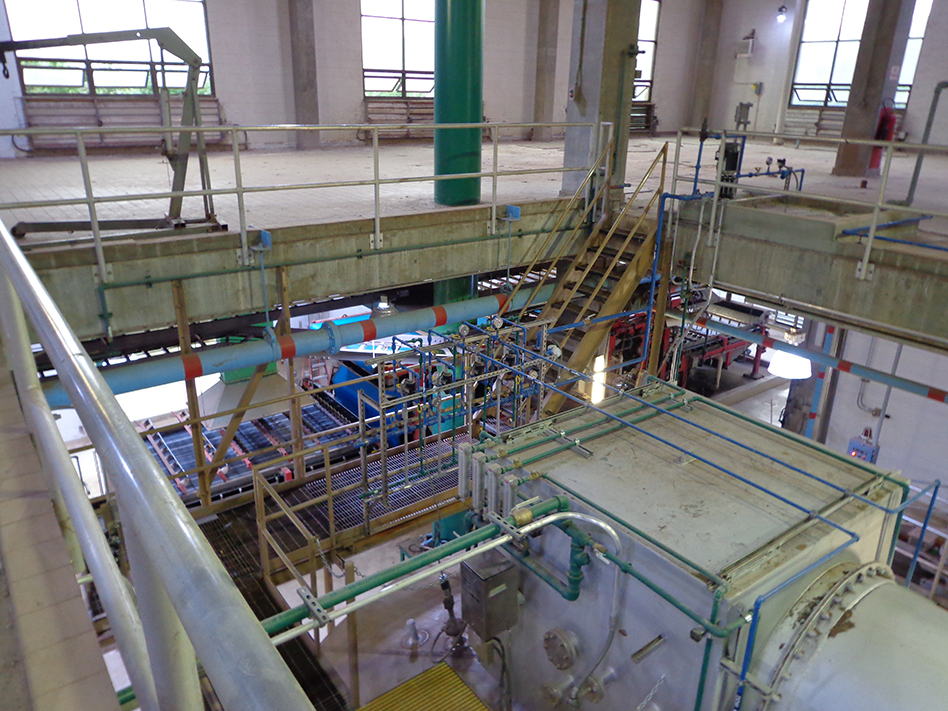 |
Photo 5: To convey ash to an onsite lagoon system and replace aged infrastructure, new ash transfer pumps were installed.
|
Photo 6: In addition to air pollution control improvements, this project also replaced quenching water systems to improve operation and safety of the fluidized bed incinerator system.
|
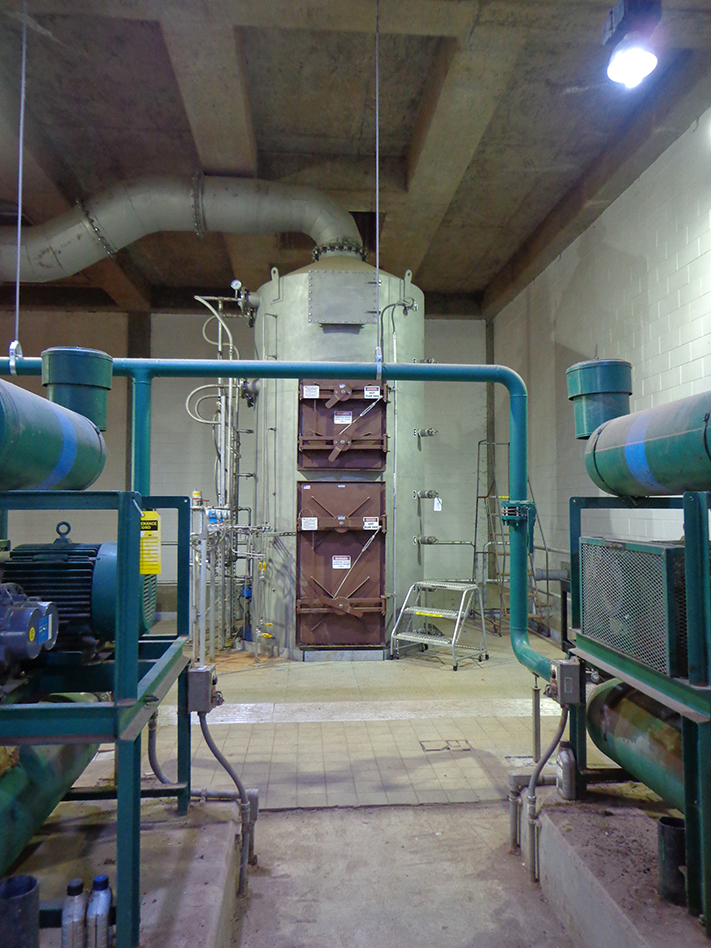 |
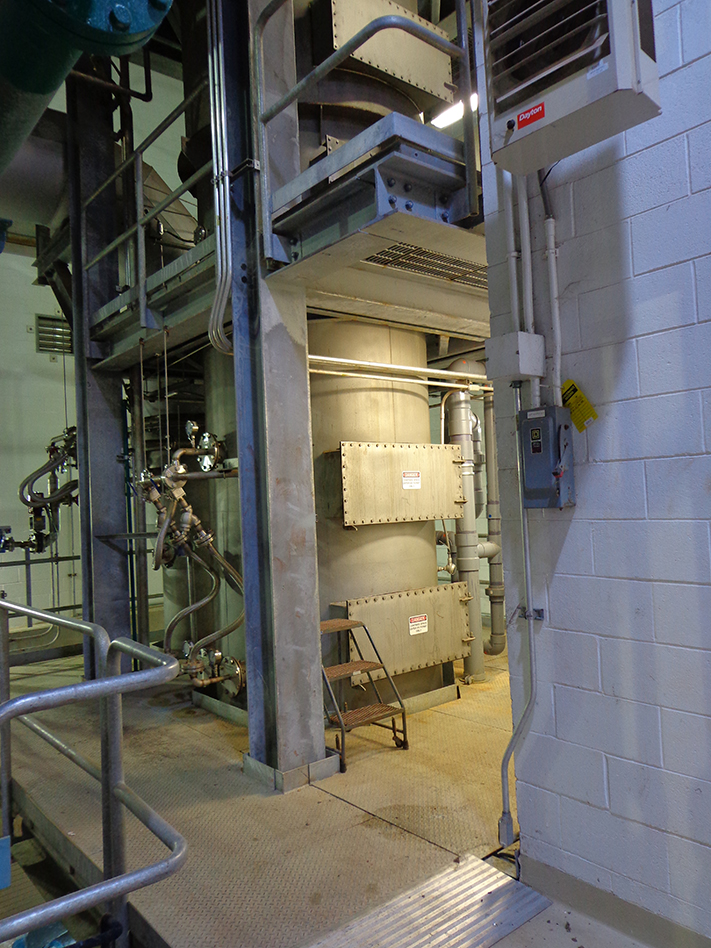 |
Photo 7: The SPC filter system was configured with dual pressure rated doors to facilitate easy access for filter module adjustments and replacement - improving on the standard design for the system, which required a significant number of bolts to secure the access hatches.
|
Photo 8: The design of the multi-venturi scrubber and SPC module system included a robust work platform structure surrounding the process components to provide easy access for operation and maintenance of key components.
|
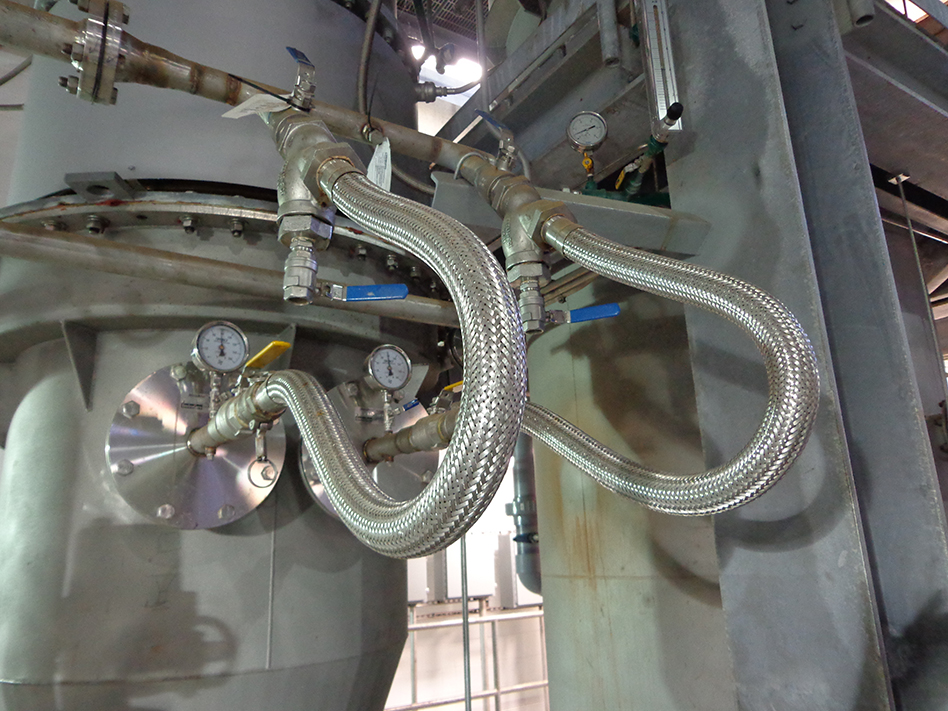 |
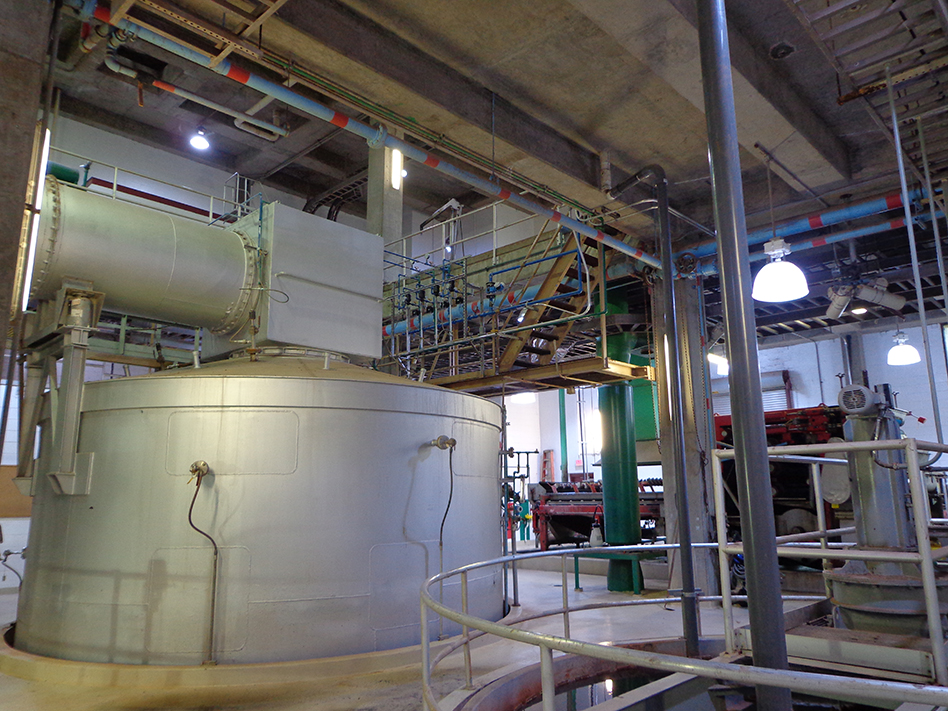 |
Photo 9: Instrumentation and control systems were added to optimize particulate removal - a functionality that is vital to proper operation of the multi-venturi scrubber.
|
Photo 10: The rehabilitation of the fluidized bed incinerator included replacement of the exterior metal dome on the incinerator, as well as insultation repairs, which will extend useful life and improve system performance.
|
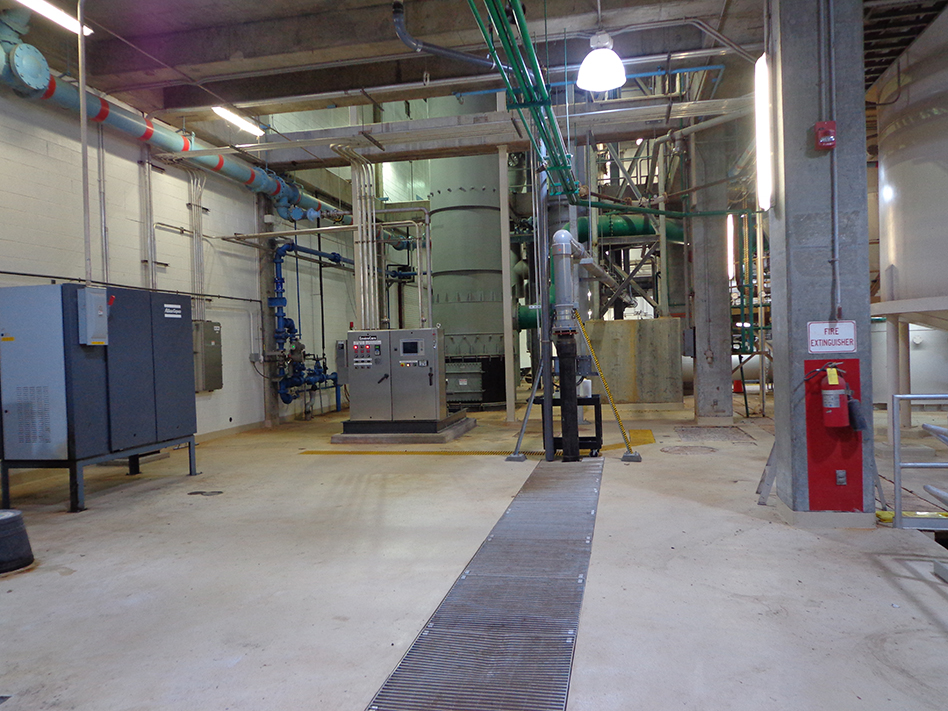 |
Photo 11: The overall improvements were completed within a concise footprint, opening up space for future flexibility for MSD.
|
|
|