2018 Excellence in Environmental Engineering and Science® Awards Competition Winner
From Pilot to Full Scale: Development of STARx HottPad®
Entrant: Savron, a division of Geosyntec Consultants International, Inc. Engineer in Charge: David Major, Ph.D., BCES Location: Houston, Texas Media Contact: David Major, Ph.D., BCES
Entrant Profile
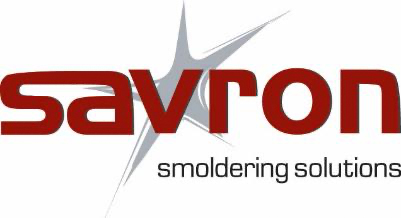
Savron is an operating division of Geosyntec Consultants International, Inc., an employee-owned, multi-national provider of sustainable waste management and remediation solutions, specializing in the safe, energy-efficient, environmentally responsible treatment of a broad range of hazardous materials. Savron helps organizations in the oil and gas, waste management, chemical manufacturing, and utilities industries manage environmental liabilities and comply with regulatory requirements.
Self-sustaining treatment for active remediation (STAR) is based on a patented technology - an energy-efficient self-sustaining combustion process that captures and recycles the energy released from hazardous materials to destroy them in an effective, controllable, and safe manner. A broad range of hazardous materials including petroleum hydrocarbons, coal tar, creosote, and mineral oils can be treated by this technology. It works faster and to a dramatically higher environmental standard than common hazardous waste disposal practices such as thermal desorption, incineration, solidification, or landfilling.
A committed team of individuals from Savron, Chevron, the University of Western Ontario, and Queensland University successfully took the concept of STAR and developed an above ground application (STARx) to treat excavated soils and sludge using an engineered soil pile. The soil pile is placed on a HottPad®, a low-profile base with the air supply and heating infrastructure required to smolder oil-impacted soils (OIS) or sludge mixed with a porous media (e.g., clean sand or OIS). Pilot testing involved the use of reactors systems of various scales and a prototype HottPad system to assess materials for construction, scaling effects, heating and process controls and monitoring, and treatment effectiveness of various types of hydrocarbons and soils. A full scale STARx HottPad system was then designed to treat 12,000 cubic meters (m3) of sludge mixed with OIS. The system was manufactured in North America, shipped and installed at an operating terminal facility in the South East Asia (SEA) to successfully treat sludge from an oil/water separator pond in 2017.
Project Description
Background
STAR is a patented self-sustaining process based on the principals of smoldering combustion to destroy heavy hydrocarbons and usually used to treat contaminated soils below ground. However, many sites have excavated OIS and/or ongoing operations that produce waste sludge and need a cost-effective treatment option. To achieve this goal, we developed an above ground smoldering process that has sufficient throughput rates and low capital/construction costs. Throughput will be dependent on the propagation rate of the combustion front, which is a function of the oil type and concentration, soil permeability, and injected air flux. Capital/construction costs are impacted by constructing the system of materials compatible with heating / combustion temperatures, the selected ignition method, air flow requirements, emissions management and control requirements, and soil pile configuration. The pilot test program addressed all these criteria and closed all significant data gaps as required by Chevron prior to approval for using the technology at an operating facility.
Integrated Approach to Environmental Media
Chevron's acceptance required that the technology meet their Integrated Risk Prioritization Matrix that is used to assess the likelihood of an event, its impact on safety, health and the environment, and consequences arising from facility damage, business interruption and product loss. These events can range from rare to unheard of to reasonably expected to occur. Each identified event must be addressed through strategies for short term risk reduction or by developing long term risk reduction plans and processes that are readily or reasonably implemented. The key environmental media concerns were:
- air emission control and treatment evaluation such that appropriate off-gas treatments could be integrated into the process to meet applicable regulations; and
- treated OIS meet local regulatory requirements.
Quality
A new technology must be field proven through Chevron's 9 Stage Technology Development process before it will be accepted throughout their operations as shown below:
The HottPad technology moved from Stage 5 ("Demonstration") to Stage 9 ("Field Proven") during the program, a substantial achievement in the eyes of Chevron's management. Significantly, Hottpadds exceeded OIS clean-up standards and at a 50% lower cost to alternatives.
As shown in the testimonial letter, our client is extremely pleased with our efforts.
Contributions to Social and Economic Advancement
Our technology removes OIS and sludge and risk to human health and the environment with a much lower carbon footprint than other technologies (e.g., incineration). It removes the costly options to landfill or otherwise dispose of existing OIS/sludge materials. HottPads can be integrated into on-going operations to continually treat generated residues; thereby, alleviating the land area required for their storage, removing the risk of their release into the environment, and eliminating future liability.
Originality and Innovation
Creativity and innovation is required to scale from the laboratory to an industrial scale process. We used various scaled reactors to scale the process under various scenarios, assess technology process limitations, and to collect key design and operational information.
Our approximately 1 m3 intermediate scale reactors (ISR) were used for initial testing of surrogate materials that represented the expected range of soil types and grain size distributions, and various hydrocarbon mixtures. These tests allowed us to compare observed combustion temperatures, smoldering front propagation rates, and emission profiles. We also tested "real-world" OIS and sludge shipped to our facility from Chevron's oil and gas operations in South East Asia and Australia
We used a large-scale reactor (2.5 m3) to assess and model scaling effects on propagation velocity, emission profiles, and treatment efficacy, and to evaluate ignition methods and material fatigue. The obtained results were used to design a low profile HottPad prototype for testing at our facility, and ultimately the full scale HottPad system (12,000 m3).
Our work resulted in ground breaking understanding of the smoldering process, such as how hydrocarbons can be mobilized ahead of the combustion front. This work produced Master thesis and peer-reviewed publications: Kinsman, L, et al., 2017. Organic liquid mobility induced by smoldering remediation, Journal of Hazardous Materials (325), pp. 101 - 112, DOI: 10.1016/j.jhazmat.2016.11.049). The data generated also allowed the development and application of models used to help scale and design full scale systems: Solinger, Rebecca L., "STARx Technology for Waste Oil Sludge Treatment Investigated with Numerical Modelling" (2016). Electronic Thesis and Dissertation Repository. 4153. https://ir.lib.uwo.ca/etd/4153)
Our work is being presented at international conferences:
L. Kinsman, et. al., 2013. Upscaling Self-Sustaining Treatment for Active Remediation (STAR): Experimental Study of Scaling Relationships for Smouldering Combustion to Remediate Soil, Abstract H41H-1351. Fall Meeting, American Geophysical Union, San Francisco, CA., December.
Scholes, G. et. al., 2013. Self-Sustaining Treatment for Active Remediation (STAR): Lessons Learned and Scale up from the Laboratory to the Field. AquaConSoil, Barcelona, Spain, April.
Sabadell, et al., 2018. Treatment of Oil-Impacted Soil and Oily Waste: Overview of Two Field Demonstration Projects. SPE International Conference and Exhibition on Health, Safety, Security, Environment, and Social Responsibility, Abu Dhabi, April 16-18, 2018. Paper Number: SPE-190566.
Complexity
The simplicity of our system belies its complexity in terms of variables that need to be balanced to construct, ship, and successfully operate a full-scale HottPad system at foreign location. Our design allowed delivering the entire HottPads and ancillary / control equipment in modified shipping containers that also served as control and office space. Simple site preparation was required to allow laydown of six HottPads.
Sludge from the oil/water separator lagoon was mixed with available sand by backhoe and placed on the HottPad. Thermocouples monitored temperatures in the soil piles and HottPad plenum space. Combustion gases were collected under a simple flexible heat resistant tarp system via an extraction pipe and continuously monitored and treated before discharge. Treated soils were easily removed and another batch of OIS was treated. During the entire process the temperature, air pressures, and combustion gases could be remotely monitored to assess progress and completion of the treatment. We could also change air flow to improve heating, cooling, and treatment times.
A "rolling start" of the combustion process showed that changing the sequence of heating of each of the six HottPads we could reduce the energy load by approximately one-third, which reduces the required energy infrastructure.
Click images to enlarge in separate window.
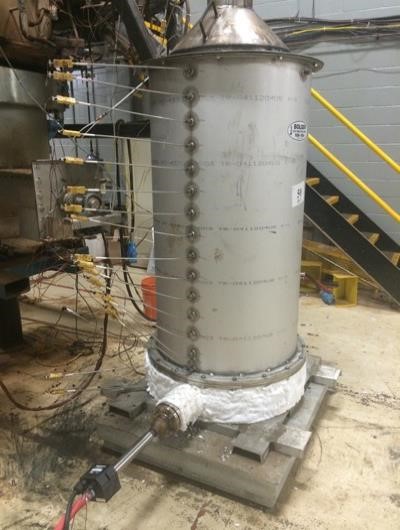 |
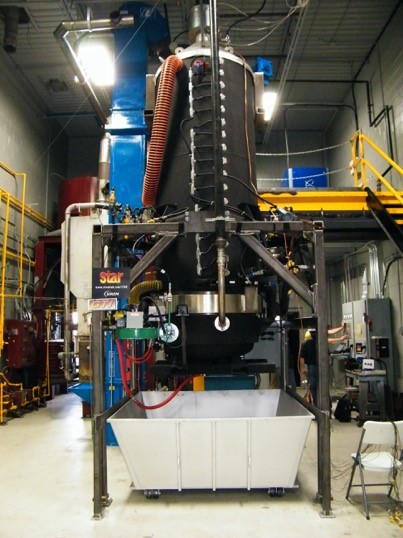 |
Photograph 1: Intermediate Scale Reactor (ISR) - Large scale columns were used to demonstrate that various OIS and types of oils could support self-sustaining smoldering reactions. A convective heater is used to inject hot air in a plenum space located at the base of the ISR. OIS is placed plenum and instrumented with thermocouples. After a short heating period to initiate smoldering, the heater is turned off while air supply is maintained. The energy in the OIS provides all the energy needed to maintain self-sustaining combustion reaction. A continuous emission system was used to profile the mixture of combustion gases, oxygen, and volatiles.
|
Photograph 2: Large Scale Reactor - A 1m diameter by 3m tall reactor was specially constructed. The weight of the reactor could be continuously measured to observe loss of hydrocarbon mass during smoldering. Thermocouple arrangements allowed measurement of temperature profiles in three dimensions. The reactor could be loaded from the top and emptied from the bottom. Emissions were characterized and treated before release. Construction using special alloy steels was found not to be required. Two heating systems were tested; direct flame through a conductive coiled heater, and externally supplied heat convective heating. Convective heating was found to be the most reliable, less wear, and less costly.
|
Photograph 3a & 3b: Prototype HottPad®
|
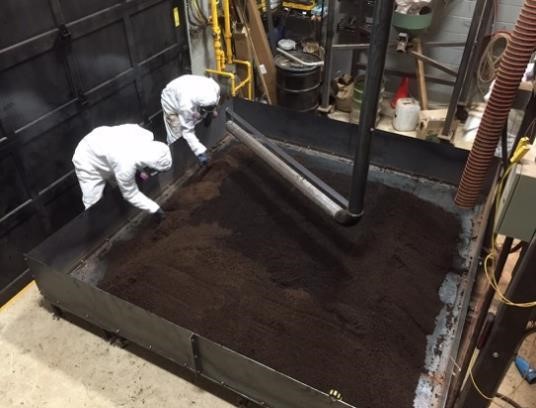 |
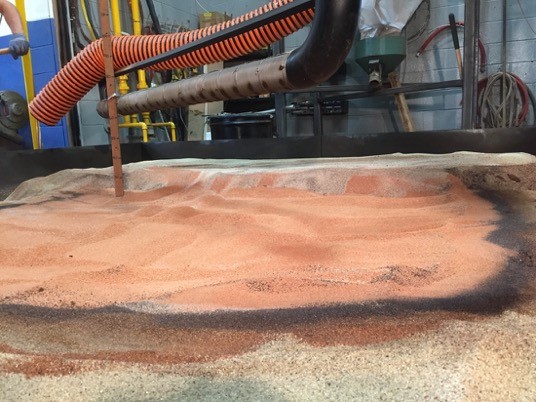 |
Photograph 3a: A square hot pad (3m by 3m) with a 1m2 screen plenum space was built and tested with OIS. A vertical extraction pipe was used to collect vapors, and the assembly covered with a heat-resistant tarp (not shown).
|
Photograph 3b: After treatment the clean soils are shown as reddish in colour due to oxidation. A "crust" of pyrolyzed material forms at the edge where there is insufficient air flow to support total combustion. The angle of the pyrolyzed edge matched modelling predictions. TPH was not detectable.
|
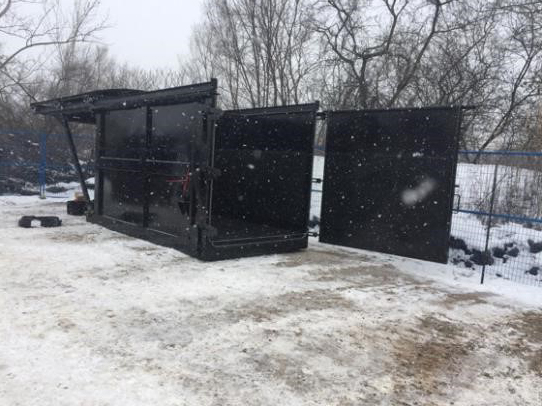 |
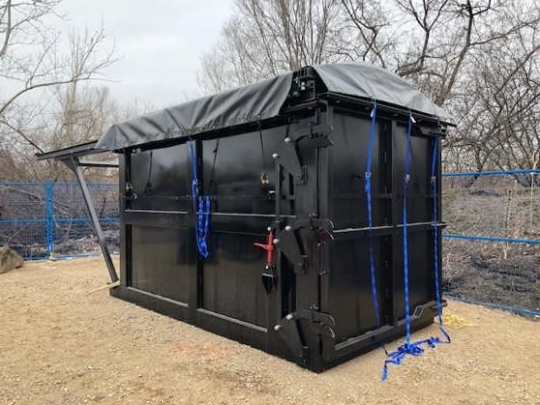 |
Photograph 4a & 4b: Commercial Pilot Test of HottPad: An outcome of the project was the development of a mobile pilot test STARx HottPad for use at client sites. This version can hold 16 tons of soil.
|
Photograph 5a & 5b: Full Scale STARx HottPad
|
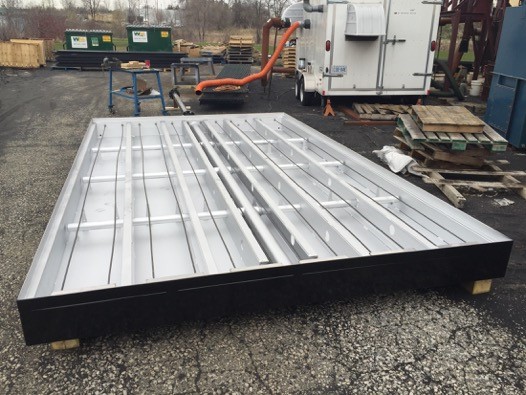 |
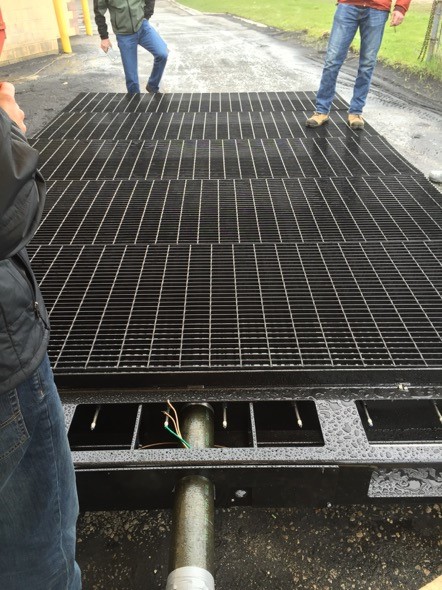 |
Photograph 5a: The base of a HottPad containing the air distribution system and resistive heaters. Each HottPad is approximately 2m x 3m.
|
Photograph 5b: The junction box for connecting the heaters to the control unit, airline, and the grates. There is a thin wire mesh sandwich between the lower and upper grate that prevent sand and dust from entering the plenum space. The HottPads are rated for 50 tons of traffic.
|
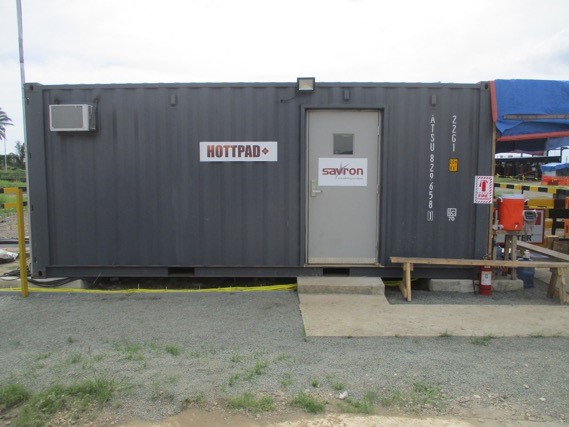 |
Photograph 6: Control Room and Office - The HottPads were shipped inside shipping containers that also serve as the office and control room (heaters, blower, compressor control).
|
Photograph 7 (a,b,c): Assembled HottPad
|
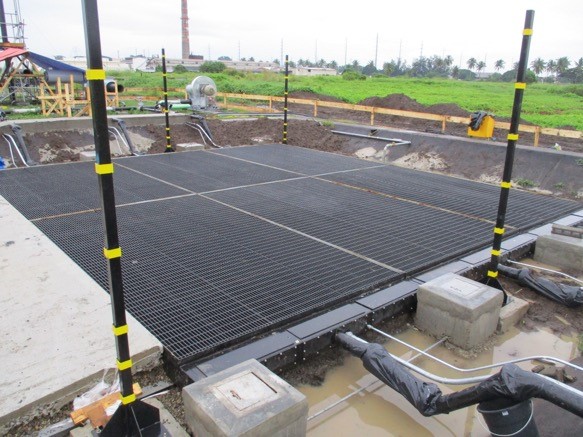 |
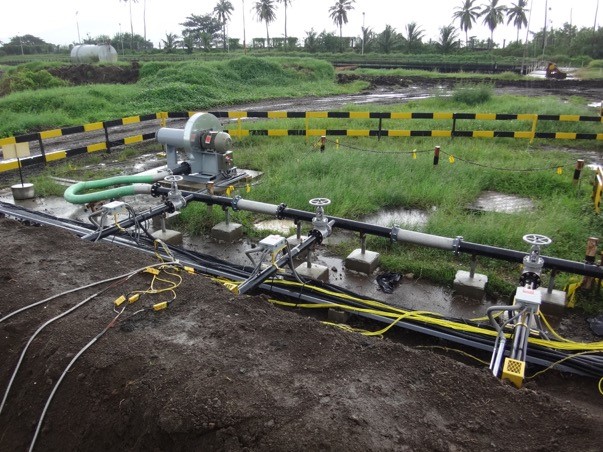 |
Photograph 7a: Six Hottpads are connected together to create the surface on which OIS are placed. A surface area of any size can be assembled to meet the throughput requirements.
|
Photograph 7b: An air compressor connects to a common header to three of the HottPads. Air to each HottPad can be controlled via the valves. There is a duplicate compressor to service the other three HottPads. Yellow lines are connected to thermocouples.
|
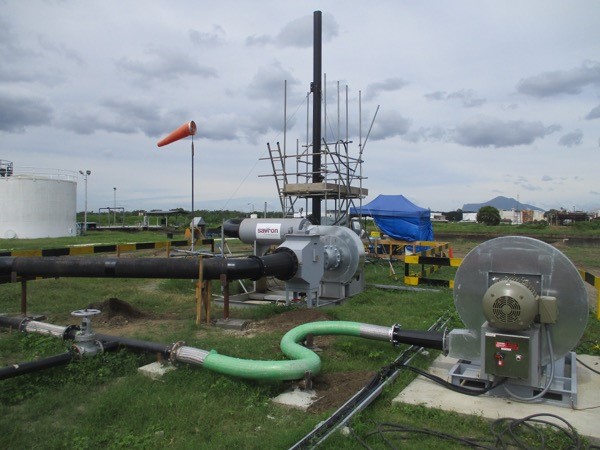 |
Photograph 7c: A blower collects off gases from the top of the HottPad (not shown), transfers them to the air treatment system, and then to the emissions stack.
|
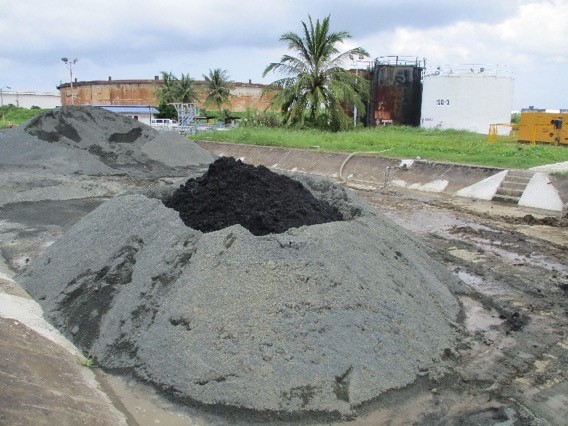 |
Photograph 8: OIS - Sludge from an oil/water separator lagoon is mixed with local site soil to create a mixture. The mixture is mixed with a backhoe.
|
Photograph 9a & 9b: OIS Loading
|
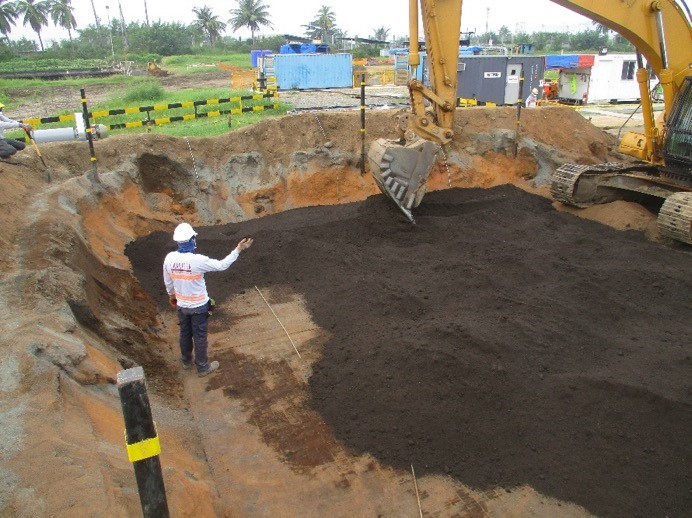 |
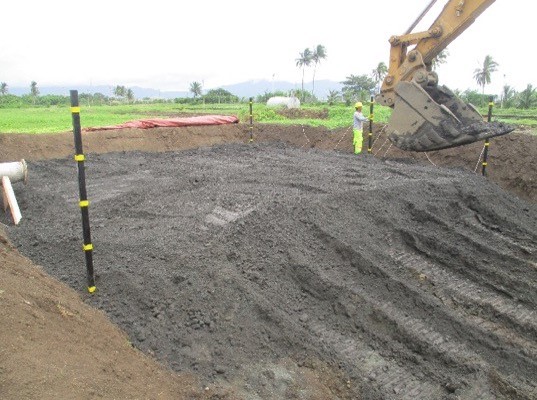 |
Photo 9a: The OIS is loaded on top of the HottPad
|
Photo 9b: A clean sand cap is placed over OIS to act as heat sink and flame arrestor. Previously treated soils can be used as the clean cover.
|
 |
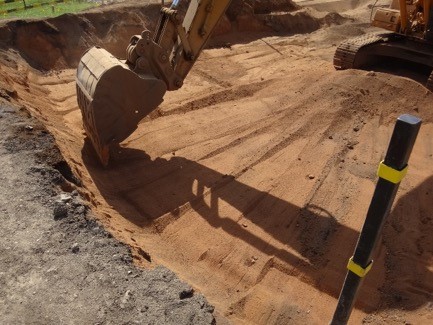 |
Photograph 10a & 10b: Post-Treatment Unloading of Soil - Treated OIS is characteristically red in colour due to oxidation of iron in the soil.
|
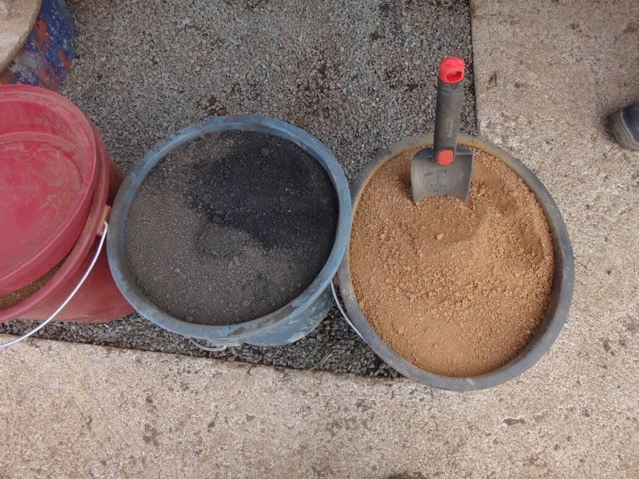 |
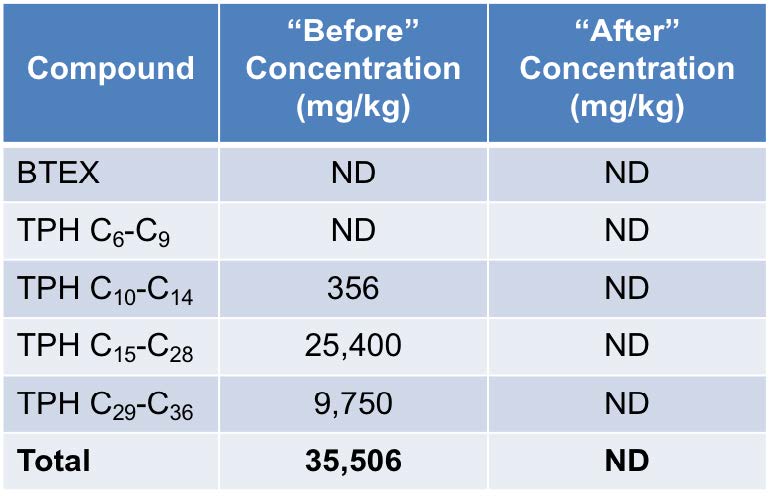 |
Photo 11: Typical Results - A clear difference can be seen between untreated (left) and treated OIS (right).
|
Photograph 12: Concentration Table - Analytical results confirm visual observations.
|
|