2017 Excellence in Environmental Engineering and Science® Awards Competition Winner
Honor Award - Research
Biotrickling Filter for Digester Gas Hydrogen Sulfide Control at the JWPCP
Entrant: Sanitation Districts of Los Angeles County Engineer in Charge: Grace Robinson Hyde, P.E., BCEE Location: Whitter, California Media Contact: Sam Pedroza, LACSD
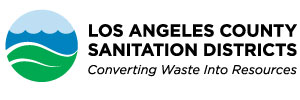
Entrant Profile
The Sanitation Districts protect public health and the environment through innovative and cost- effective wastewater and solid waste management and, in doing so, convert waste into resources such as recycled water, energy, and recycled materials.
The Sanitation Districts consist of 24 special districts serving about 5.6 million people in Los Angeles County. The service area covers approximately 850 square miles and encompasses 78 cities and unincorporated territory within the county.
Seventeen of the Sanitation Districts in the metropolitan Los Angeles area are served by a regional, interconnected system of facilities known as the Joint Outfall System (JOS). The JOS service area includes 73 cities and unincorporated territory, as well as small areas within the City of Los Angeles, Orange County, and San Bernardino County.
The JOS employs two main types of treatment plants. Upstream water reclamation plants (WRPs) capture low salinity, high quality wastewater and produce a drought-resistant water resource – disinfected tertiary recycled water that is ready to use without further treatment. Downstream, the Joint Water Pollution Control Plant (JWPCP) treats high salinity wastewater along with the solids removed at the upstream plants. The higher salinity means that JWPCP water needs to be treated further to be recycled and reused. The Sanitation Districts have entered into a partnership with the Metropolitan Water District of Southern California to explore providing this advanced treatment and creating a significant new source of local water.
Project Description
Hydrogen sulfide (H2S) concentrations in digester gas can be an odor issue and intensify metal corrosion. In addition, local air pollution regulations require that the H2S concentrations be controlled to minimize emissions of sulfur oxides if digester gas is combusted. Consequently, control of H2S in digester gas is an important part anaerobic digester operation. Current H2S control measures are expensive and can be difficult to manage. Due to the expense and limitations of existing H2S control measures, the Sanitation Districts of Los Angeles County (Districts) developed a biological system that is economical and relatively easy to operate.
The development work was done at the Districts' Joint Water Pollution Control Plant (JWPCP) in Carson, California. This facility generates approximately 7.5 million cubic feet of digester gas per day, which is sufficient to generate 20 Megawatts (MW) in a combined cycle power plant. The power plant must meet the South Coast Air Quality Districts' (SCAQMD) regulation for H2S of 40 ppm for combusted digester gas. To meet this requirement, the Districts currently add ferrous chloride to react and combine with the sulfides in the digesting sludge. Approximately $4 million per year of ferrous chloride is being used to control digester gas H2S levels at the JWPCP.
A biological treatment system was developed by the Districts to reduce the costs of digester gas H2S control. The system uses sulfur oxidizing bacteria inside of a biotrickling filter to remove H2S directly from digester gas. While sulfur oxidizing bacteria have been used to remove H2S from air process streams for many years, using such bacteria to remove H2S from digester gas is a novel process. The new process is well suited to its task because it employs bacteria that are already present in a wastewater treatment facility.
The first step in the removal of H2S by sulfur oxidizing bacteria is the dissolution of gaseous H2S into the recirculating liquid solution on the scrubber packing and the subsequent dissociation of H2S in the liquid phase (Equation. (1) below). After the initial dissociation of H2S, sulfide is oxidized by the bacteria to release energy. Sulfide oxidation often occurs in steps with elemental sulfur as an intermediate product, as seen in Equation (2) and in oxygen-limited environments, oxidation may proceed only to elemental sulfur, producing less energy. The most energy is released when sulfide is oxidized completely to sulfate Equation (3).
To determine if a biotrickling filter system could be used to remove H2S from digester gas, pilot plant systems were used for initial testing. The pilot system was evaluated using the following factors:
- Removal efficiency: The ability to effectively remove H2S from digester gas is a key requirement in the efficacy of a biotrickling filter system.
- Cost effectiveness: Cost is a key factor in determining the viability of new technologies. If the system is very costly to construct or operate, the technology may not be acceptable.
- Sensitivity to operational changes (resilience): The sulfur oxidizing bacteria are aerobic microorganisms that require oxygen to oxidize H2S. There are concerns about the bacteria being sufficiently robust to reliably oxidize sulfur in the low oxygen environment of the biotrickling filter under variable H2S conditions.
The Districts operated several pilot plant configurations at the JWPCP to determine the most effective designs. The study was conducted in phases to determine the required empty bed residence time, selection of effective biotrickling filter media packing, optimum recirculation rates, appropriate pH conditions and digester gas oxygen content. A comprehensive sampling and analysis program was used during all phases of testing. Inlet digester gas flow and air rates were monitored along with inlet and outlet H2S concentrations, recirculation solution pH, and recirculation solution ammonia concentrations. In addition, inlet and outlet organic sulfur compounds and outlet oxygen concentrations were periodically analyzed.
The pilot units were operated for over two years and demonstrated the ability to effectively and economically remove H2S. The pilot system was able to achieve over 95% removal of H2S with the only operational cost being the electricity used for the solution recirculation pump. A summary of the critical optimal design parameters that were determined during the pilot plant testing are shown in Table 1.
Table 1. Design Parameters Developed for Full-Scale Biotrickling Filter.
Table 2. Biotrickling Filter Resilience Test Results.
Digester gas treated and percent removal of H2S by full-scale biotrickling filter.
Process resiliency was evaluated systematically using the pilot system. Three commonly encountered operational outages/equipment failures were simulated: power outage at the biotrickling filter for 24 and 72 hours and power outage for 72 hours and loss of the recirculation solution. As shown in Table 2, the biotrickling filter was able to reachieve 90% H2S removal in reasonable time periods.
The data generated by the pilot system were used to construct a full-scale biotrickling filter system that could treat 300 cubic feet per minute of digester gas. This system was constructed and put into service in April 2015 and as shown in the figure below has been operating effectively for over eighteen months saving the plant $500 per day in chemical costs.
Demonstration of a Comprehensive, Integrated Approach That Considers All Environmental Media (Air, Water, and Land)
The main project benefit is an improvement to digester gas quality through the removal of H2S, which reduces odor and helps meet requirements for sulfur oxides when the digester gas converted to electricity. Compared to the current method of treatment, the new system reduces chemical use which reduces the production of biosolids and the number of truck trips required to haul biosolids to their end use site. Reduced chemical usage reduces chemical deliveries to the treatment plant and reduced chemical production. Reduced truck trips and chemical produce result in less energy consumption and less emissions of air pollutants.
Quality as Evidenced by the Degree of User Satisfaction and Proven Performance
The project resulted in a full-scale installation that has been effectively operating for over 18 months. The system has been able to treat over 300,000 cubic feet per day of digester gas and consistently remove over 98% of the inlet H2S. Plant operators are very satisfied with the biotrickling filter due to the ease of operation and minimal maintenance required. Plant staff is also pleased with the significant reduction in costs required for H2S control.
Originality and Innovation
This project is the first, full-scale demonstration of a digester treatment system using sulfur oxidization in a biotrickling filter at a low empty bed residence time to remove H2S from digester gas. The results demonstrate that biotrickling filters can significantly reduce the cost to control H2S in digester gas. These results could be utilized by other wastewater utilities to provide H2S control in a more cost-effective and environmentally superior manner.
Complexity of the Problem Addressed
There are many technologies available to remove H2S from digester gas and most are expensive and difficult to operate. The development of a H2S treatment system that can reliably and economically treat digester gas can be a significant benefit to many wastewater treatment facilities. High concentrations of digester gas H2S can be a major issue for wastewater treatment facilities due to air pollution regulations, corrosion of equipment and piping, and odor. This technology requires a relatively small footprint and does not need the addition of chemicals or significant amounts of energy. The use of the biotrickling filter results in multiple environmental benefits including reduced traffic, reduced traffic emissions, and reduced energy consumption.
Project Contributes to/or Offers the Prospect of Contributing to Social or Economic Advancement
This study demonstrated that the biotrickling filter technology can be operated effectively at a very low cost. The savings in using this technology can be significant with large facilities like the JWPCP saving over $3 million per year.
This biological technology can be used at wastewater facilities across the country providing more cost-effective and environmentally sound treatment. By effectively eliminating odorous H2Sc, the new technology can help wastewater treatment facilities to be better neighbors with their surrounding community.
Click images to enlarge in separate window.
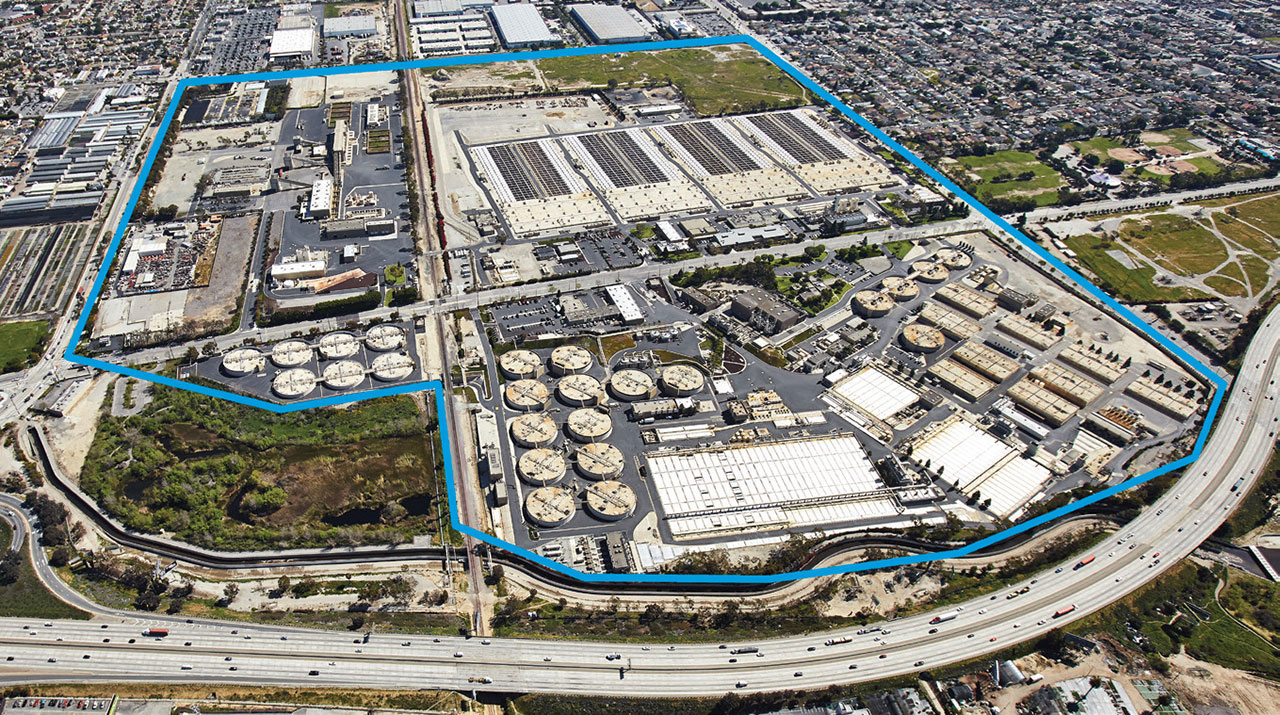 |
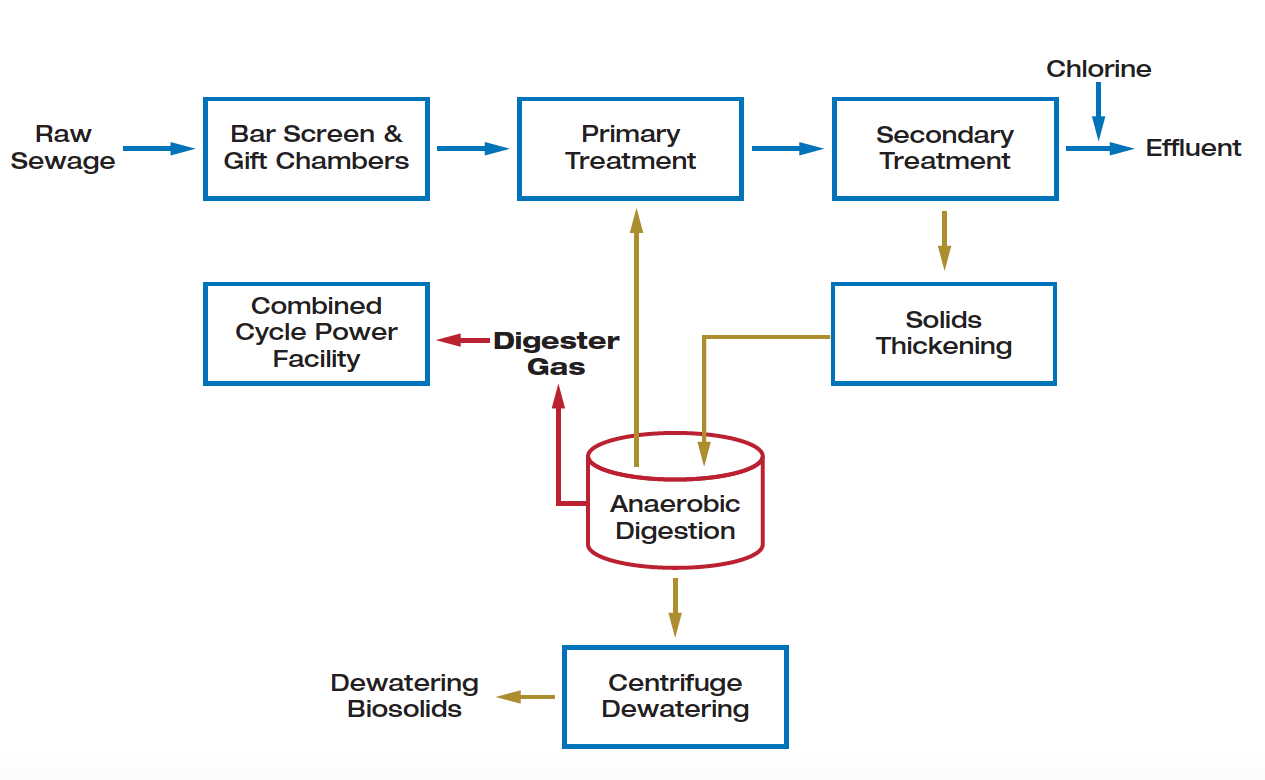 |
Aerial photograph of the JWPCP, location of the biotrickling filter developed to removing H2S from digester gas.
|
The JWPCP is designed for 400 million gallons per day (MGD) of dry weather flow and currently treats 260 MGD of wastewater. The digester gas is used to generate 20 MW of power, which is sufficient to power all of the JWPCP. The digester gas H2S is current maintained to below 40 ppm by the use of ferrous chloride.
|
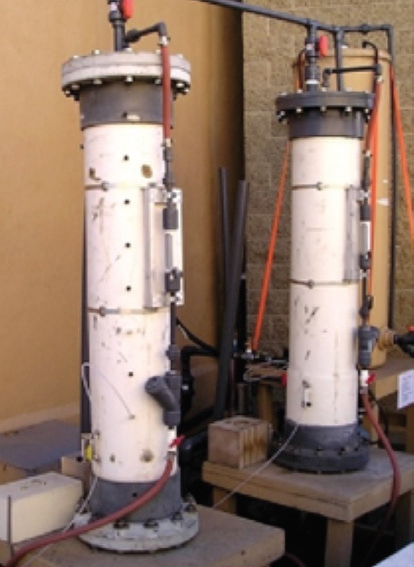 |
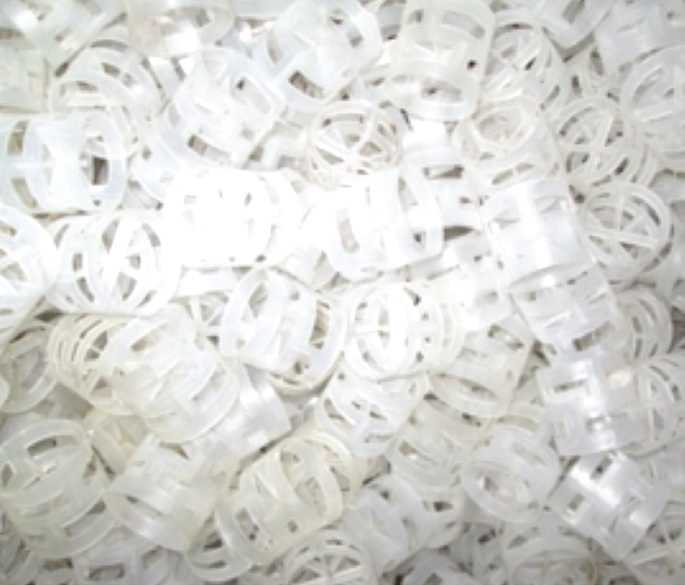 |
Two of the pilot biotrickling filters used to deter- mine effective operational conditions.
|
Pall ring media packing that were determined to be most effective as microorganism carriers for the biotrickling filters.
|
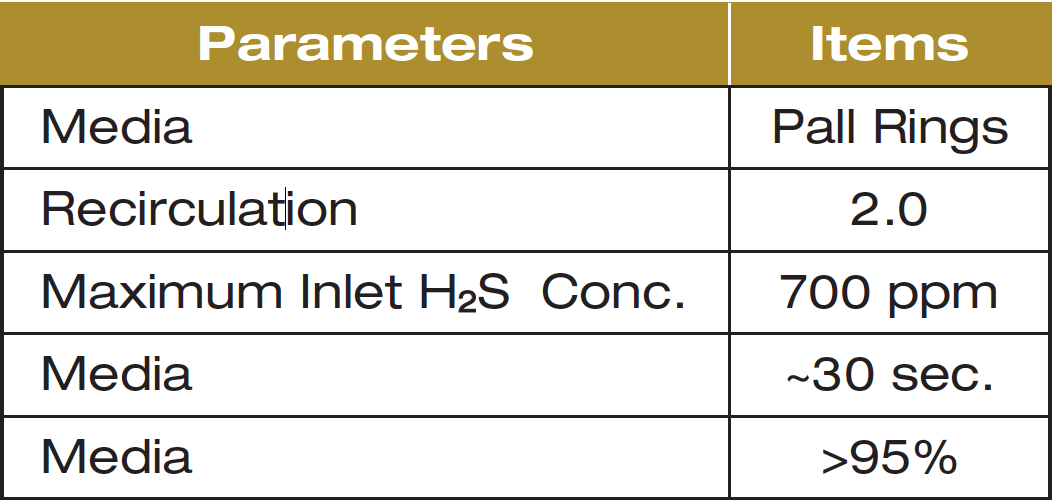 |
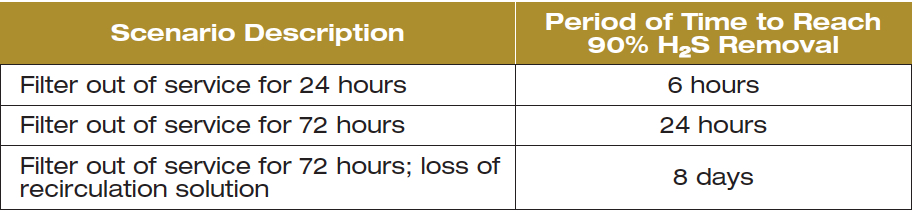 |
Design Parameters Developed for Full-Scale Biotrickling Filter.
|
Biotrickling Filter Resilience Test Results.
|
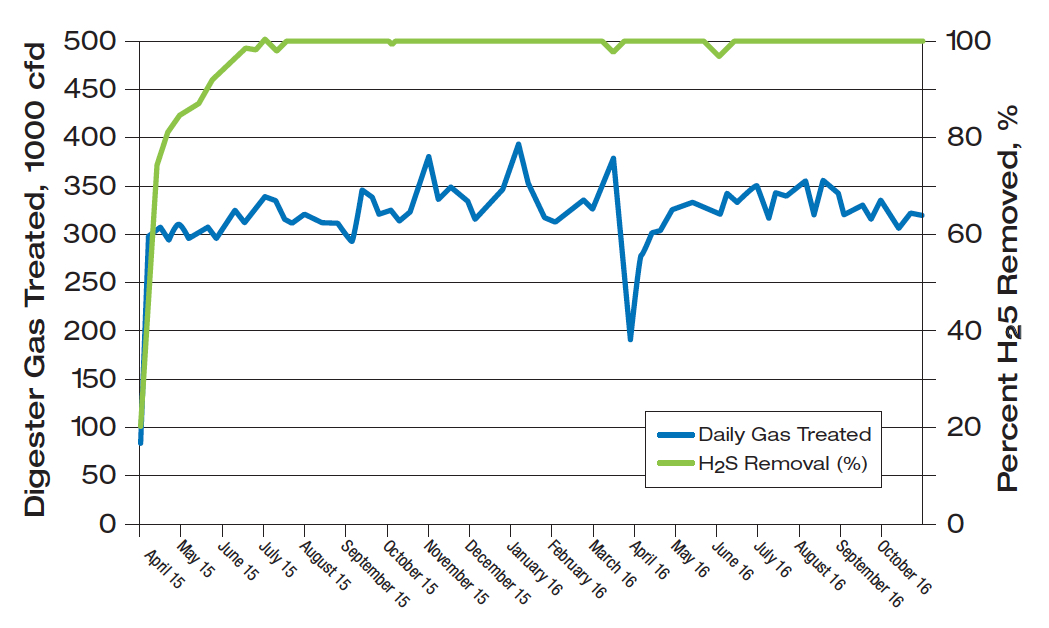 |
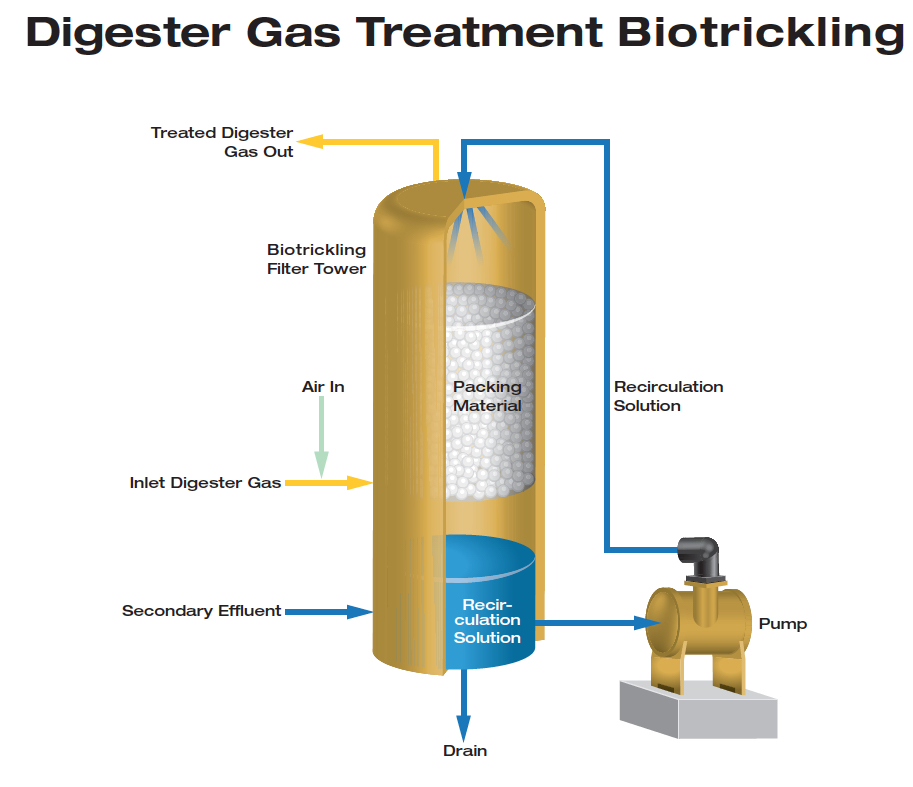 |
Digester gas treated and percent removal of H2S by full-scale biotrickling filter.
|
Schematic of biotrickling filer process.
|
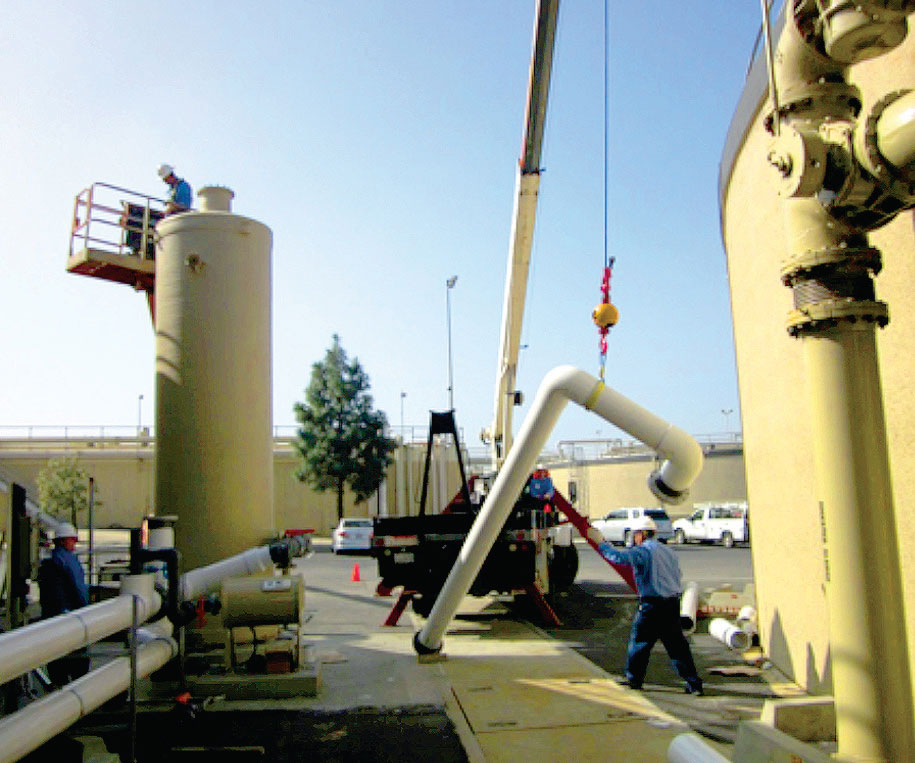 |
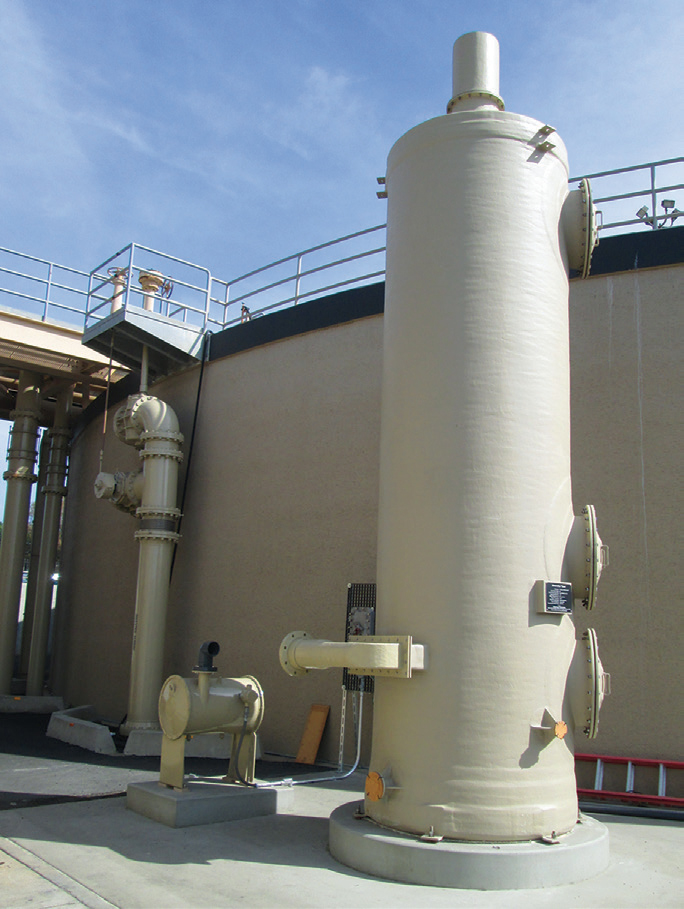 |
Biotrickling filter system during construction.
|
Finished Biotrickling filter system.
|
|