2022 Excellence in Environmental Engineering and Science® Awards Competition Winner
Honor Award - Industrial Waste Practice
Muscatine Organic Waste Recycling Center
Entrant: Stanley Consultants Engineer in Charge: Jay Brady, P.E. Location: Muscatine, Iowa Media Contact: Mary Jo Finchum
Entrant Profile
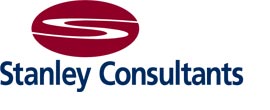
The Muscatine Organic Waste Recycling Center is one of just three municipally owned food waste recycling facilities in the U.S. It’s the only one of its kind in the Midwest.
Its unique ability to separate food waste from its packaging allows the processing of packaged food that would otherwise be landfilled because the labor costs to separate food from its packaging are prohibitive.
The spinning paddles on the T42 Turbo Separator break open packaging and separate the organic waste from its containers. The captured organic waste is homogenized and then fed into the same anerobic digesters that clean the city’s municipal wastewater by converting organic solids into biogas.
The facility is putting Muscatine on the map as a regional hub for organics recycling.
Stanley Consultants has been the prime consultant and engineer for the project for over seven years. During this time the firm has provided a variety of design concepts as the project evolved, as well as preliminary and final design and permitting.
The firm has provided multiple studies and analyses, including:
- Co-digestion feasibility study
- Local high strength waste producer research
- Assessment of types and quantities of waste that might be received
- Receiving system concepts
- Projection of potential biogas production levels
- Feasibility of compressed gas storage
- Costs analyses and construction cost estimates
- Review of renewable fuels credit programs
- Direct pipeline injection costs
- Concepts for receiving and processing facilities
Stanley Consultants provides program management, planning, engineering, and environmental services worldwide.
Project Description
COMPREHENSIVE INTEGRATED APPROACH
Recycling was a central feature of this project with many of its facilities being repurposed/ recycled from previous uses.
Land
- The facility is housed in an idle recycling center, essentially recycling the recycling center. This not only saved millions of dollars but repurposed existing infrastructure that was ideal for the purpose and located just blocks from the water and resource recovery facility.
- The 35,000-gallon tank that stores and mixes the organic waste was rehabilitated and retrofitted with new pumps, piping and controls. Existing piping and control valves were identified to transport the blended waste to the digesters.
- Land utilization is improved by removing organics from landfills, which account for nearly 30 percent of landfill content extending landfill life.
- The process produces a nutrient rich soil amendment. About 6 million gallons/year of biosolids are applied on farmland increasing soil organic and micronutrient content.
Air Quality
- Decreases air emissions by lowering landfill methane production.
- Future use of biogas will offset carbon dioxide emitting fuels.
Water
- Application of the biosolids to farmland reduces the nitrogen and phosphorus fertilizer needed, reducing the likelihood of runoff.
- The landfill leachate is cleaner due to the removal of organics.
QUALITY
”Like the Apollo moon shot, we took a leap of faith,” said City of Muscatine’s Water and Resource Recovery Facility Director Jon Koch. “The innovative approaches we took were proven to work and the end product has been better than what we envisioned.”
Phase 2 of the project is in the planning stages. Koch’s long-term vision is to produce enough methane to power city vehicles, inject into gas pipeline or produce renewable electricity situated in a microgrid to supply heat and power to while attenuating supply/demand fluctuations.
Capturing and selling the gas could be used to stabilize rates. “It’s really a win-win-win,” said Koch. “Keeping the rates low for all our rate payers in Muscatine plus doing something good for the environment and cutting greenhouse gas emissions.”
ORIGINALITY AND INNOVATION
This unique center is one of just three municipally owned food waste recycling facilities of its kind in the US. It’s the only one in Iowa and the Midwest.
“There isn’t anybody else doing this,” said Koch. “We are quickly becoming an epicenter for organic waste recycling.”
The T42 Turbo Separator allows the processing of packaged foods that would otherwise be landfilled due to prohibitive labor costs. Its spinning paddles break open the packaging, separating organic waste from its containers.
The packaging is collected for recycling or disposal. The captured organic waste is screened and discharged into a 35,000-gallon tank for blending. The homogenized waste is then continuously fed, via metered injection, into the same anerobic digesters that operate to clean the city’s municipal wastewater by converting organic solids into biogas. As a result, gas production is up five times over what it was before.
Being municipally owned provides vertical integration not available to corporate-owned facilities, such as the ability to use the City’s Transfer Station and anerobic digesters.
COMPLEXITY
The first challenge was developing a concept that met the functionality, maintainability, and budget of the City of Muscatine. There are few similar facilities to model a design. The final concept was developed in close collaboration between the City and Stanley Consultants to bring forward the best of the existing facilities tailored to meet Muscatine’s situation.
The second challenge was budget. Initial concepts started with a smaller building with limited tipping floor space and truck unloading. Recognizing facility insufficiencies, the revised design increased floor space, truck unloading and truck turning/queuing. When costs became too high, the City and Stanley Consultants worked to pivot, using an idle recycling center and simpler, smaller liquid receiving facility.
The recycling center is a marrige of tried-and-true traditional engineering systems and processes outside of the general bounds of water engineering systems. With no established manual or process to follow the team had to create the entire process from scratch. There was a big learning curve. For example, the team worked through the logistics of truck unloading and materials staging, determining what to do with the waste stream, calculating the optimum metered injection rate for material going into the digesters and the impact it would have on the digesters.
Treatment plant digesters are designed to process human waste with little organic value. Feeding high strength organic food waste to the digesters might be compared to feeding them rocket fuel. The food waste creates more biogas than traditional wastewater sludge so it’s critical to manage overall volumes, to feed it in a controlled manner and to maintain constant monitoring so that overall digestion process runs smoothly.
The project marked the first time the Iowa DNR had been asked to permit this type of facility. It was necessary to work through issues related to how DNR views this type of facility. Ultimately it was permitted under the City’s wastewater permit as source separated material and not mixed waste requiring a solid waste permit.
SOCIAL AND ECONOMIC ADVANCEMENT
Economic
In 2021 the center recycled 2,775 tons of organics and is on track to process 4,000 tons in 2022. It is funded by tipping fees of $45/ton. Based on projected revenue, it will pay for itself in four to seven years.
Most waste is trucked in from local food manufacturers but business up to 200 miles away have expressed interest. It also receives food waste from four regional and two local grocery stores.
Social
The center has been very well supported by the City of Muscatine, residents and businesses. Multiple articles, broadcasts, webpages, presentations tours and webinars have spread the word that the Muscatine is on the cutting edge for municipal organic waste processing.
Over 4,000 pounds of food waste have been collected in a free household organic waste collection bin available to residents. Local schools are piloting collection projects. Inquiries have been received from multiple municipalities, some in large metropolitan areas, who express interest in augmenting their own systems with a similar recycling center.
Click images to enlarge in separate window.
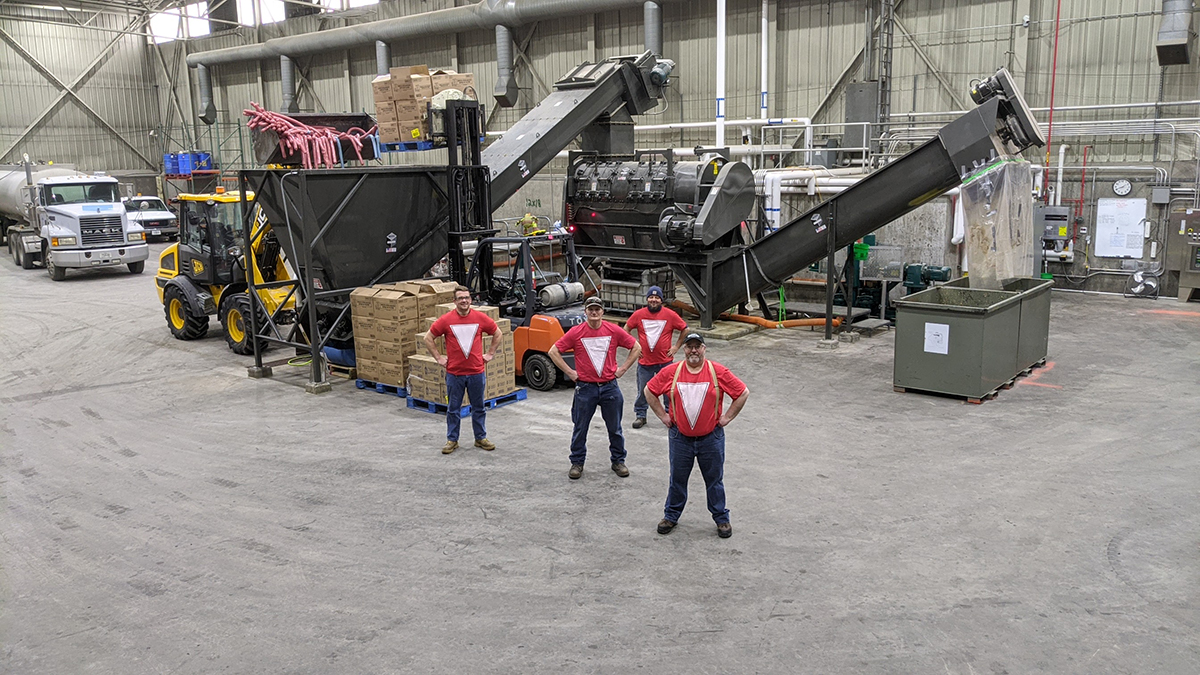 |
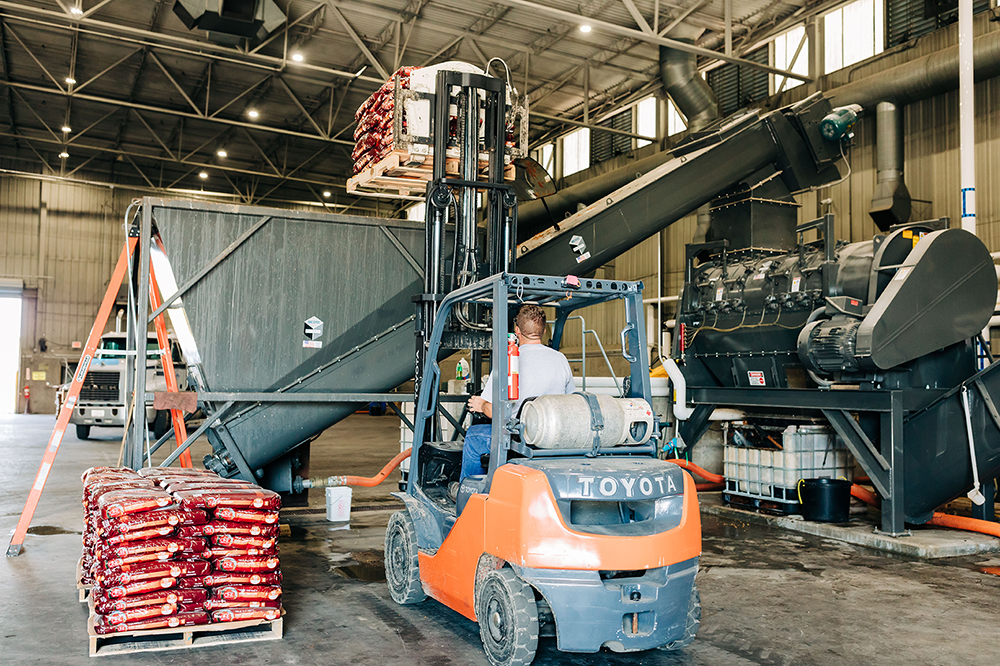 |
The Muscatine Organic Waste Recycling Center is one of just three municipally owned food waste recycling facilities in the U.S. It’s the only one of its kind in the Midwest.
|
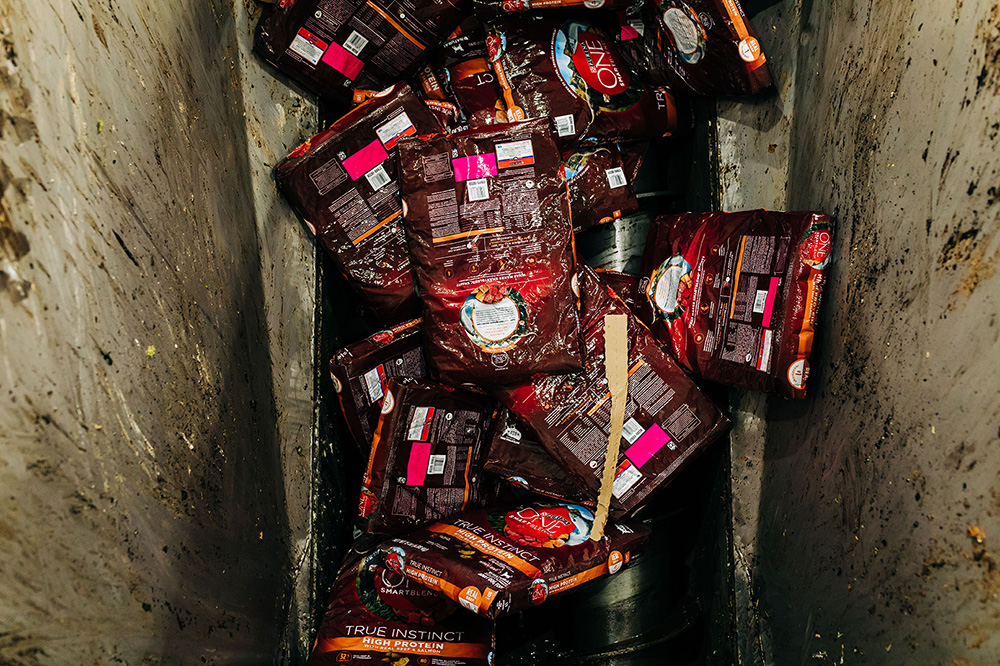 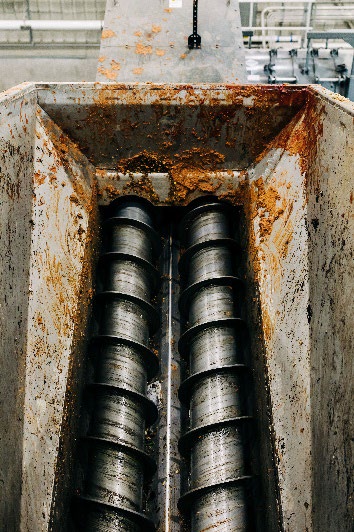 |
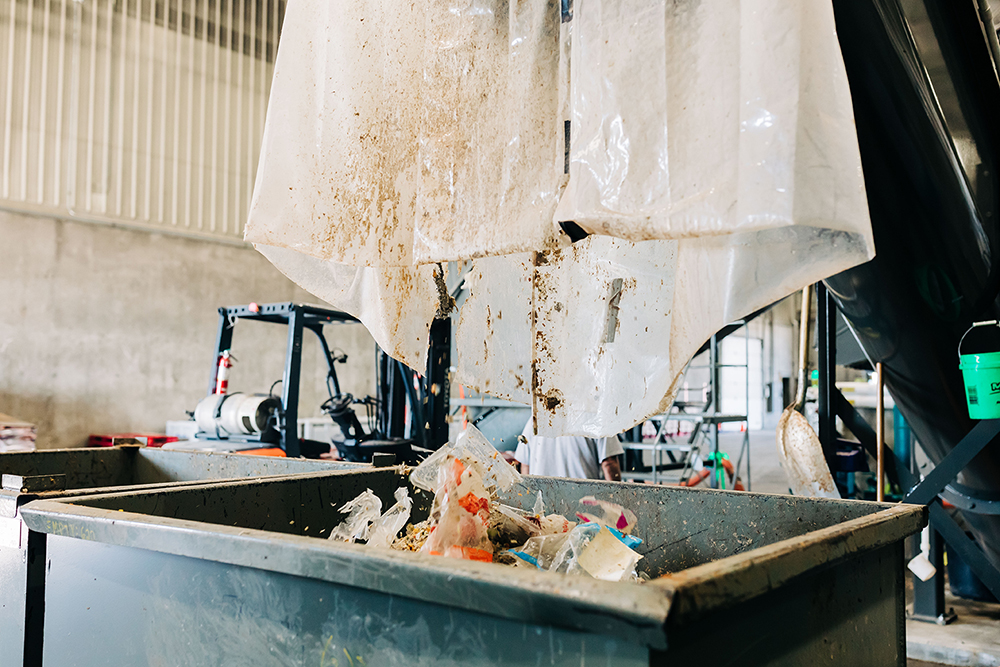 |
Packaged food waste is dumped into a hopper where twin-screw augers feed it into the T-42.
|
Its spinning paddles can break open a wide assortment of packaging, including paper, plastic, glass and aluminum. In just a matter of minutes the materials are separated. The packaging is funneled into a hopper for recycling or disposal.
|
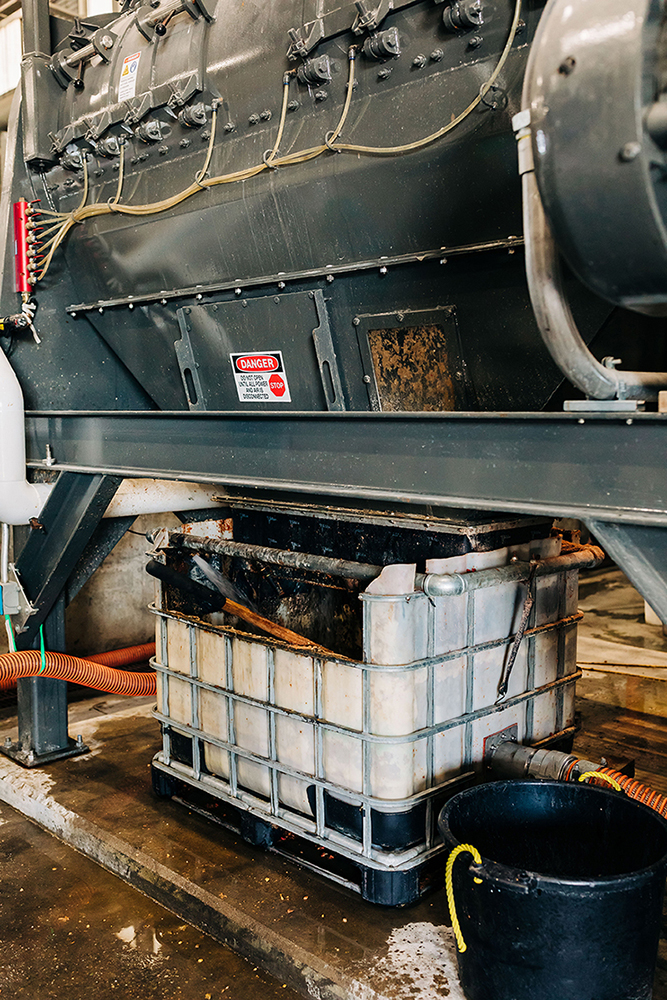 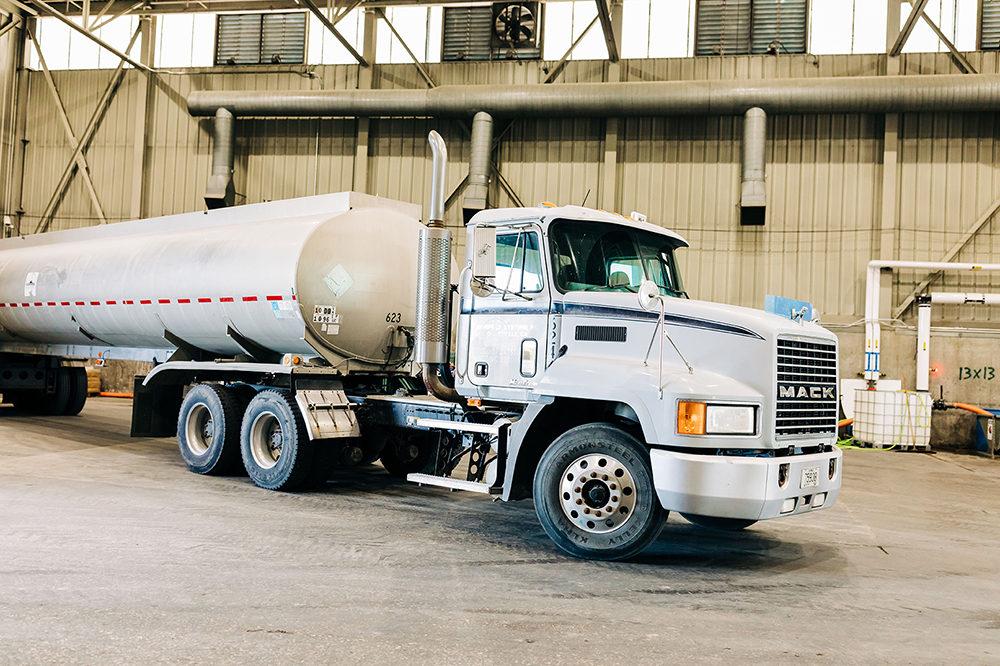 |
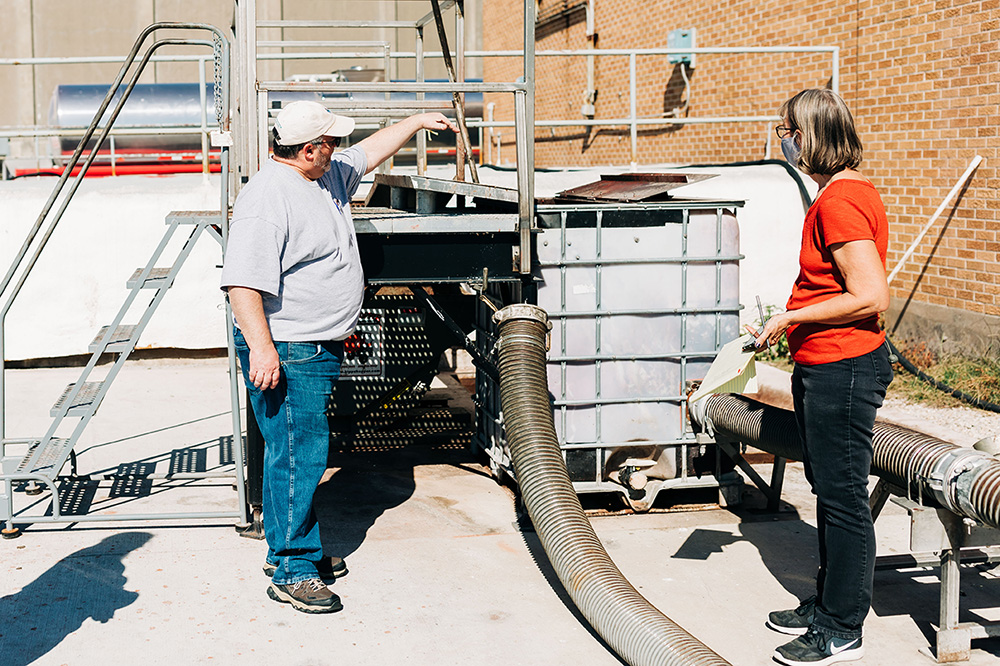 |
The organic waste is captured in a tote underneath the T42 Turbo Separator, pumped into a nearby tanker and transported ½ mile to the City’s Water and Resource Recovery Facility (WRRF).
|
At the WRRF the liquid gold is transferred through the high strength waste station.
|
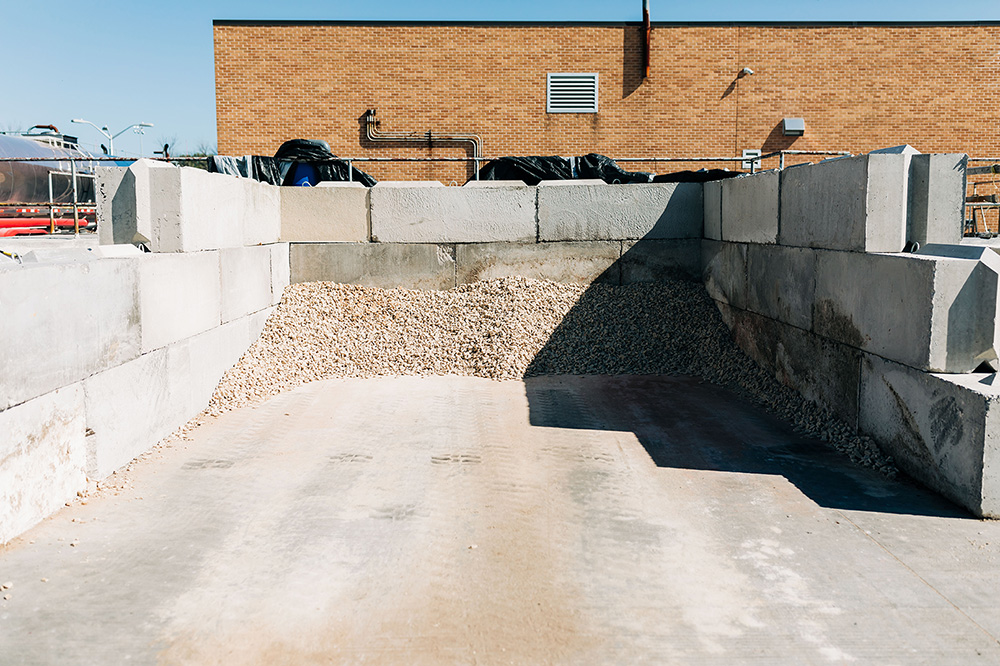 |
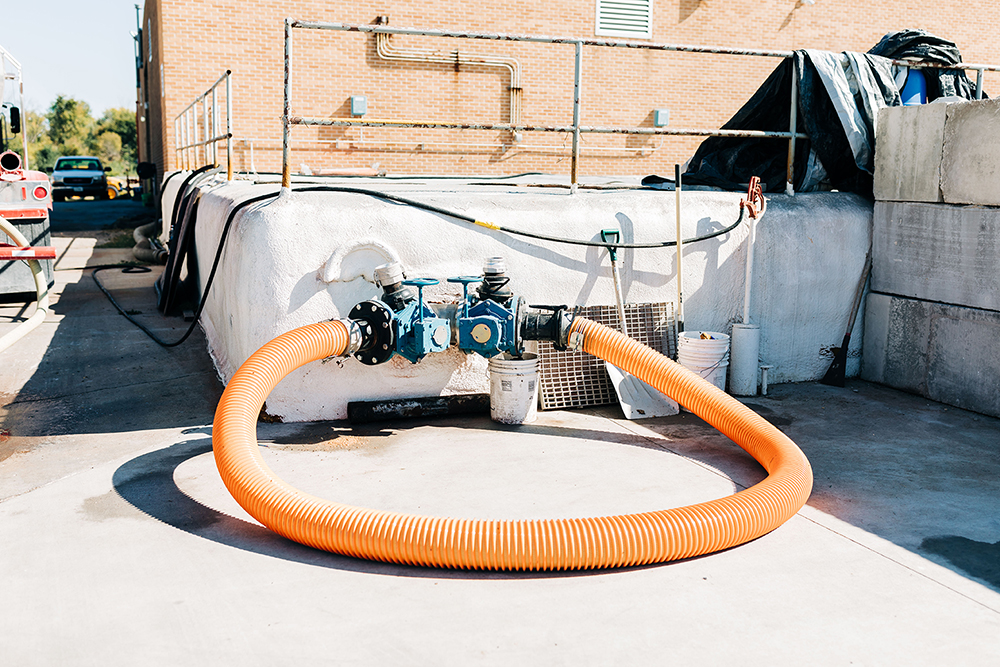 |
Dry organic solids storage bunker for receiving and staging material for loading into the high strength waste (HSW) storage tank where it is slurried in preparation for feeding to digestion.
|
Hose connection for receiving trucked liquid food waste into the HSW storage tank.
|
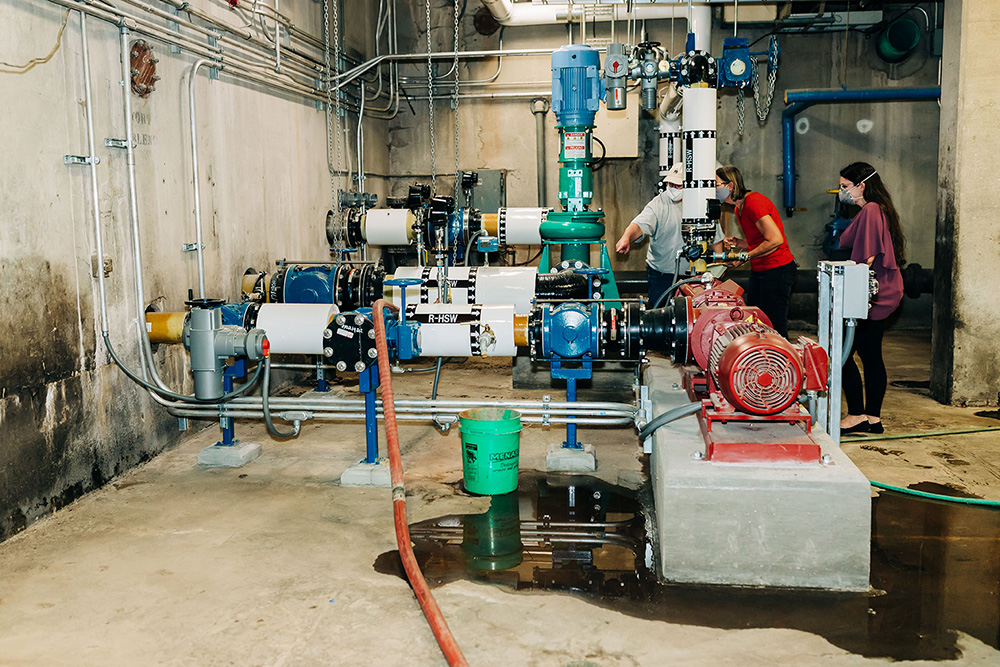 |
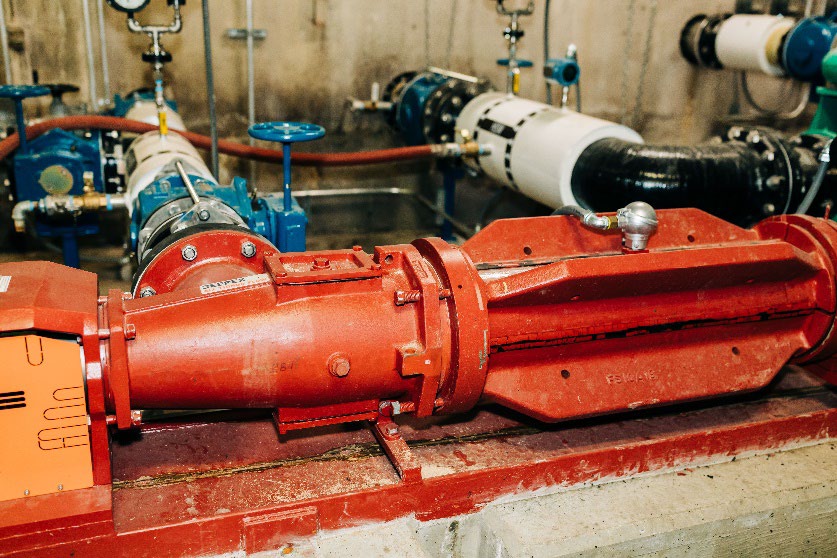 |
he liquid gold is pumped into a 35,000-gallon treatment tank, adjacent to the pump room where it is blended so that the material becomes homogenous. It is continuously fed, via metered injection, into the same anerobic digesters that operate to operate to clean the city’s municipal wastewater.
|
Retrofitting and rehabilitating the interior of the 35,000-gallon concrete tank, used for blending and storing organic waste, required intense, detailed work to repair deterioration. The interior surfaces of the 20x25x20 foot tank were blasted and cleaned. New cement surfacing was manually applied to the surfaces to rebuild the cement cover over reinforcing steel. Several layers of protective coating were applied to prevent concrete corrosion from waste acids and fumes.
|
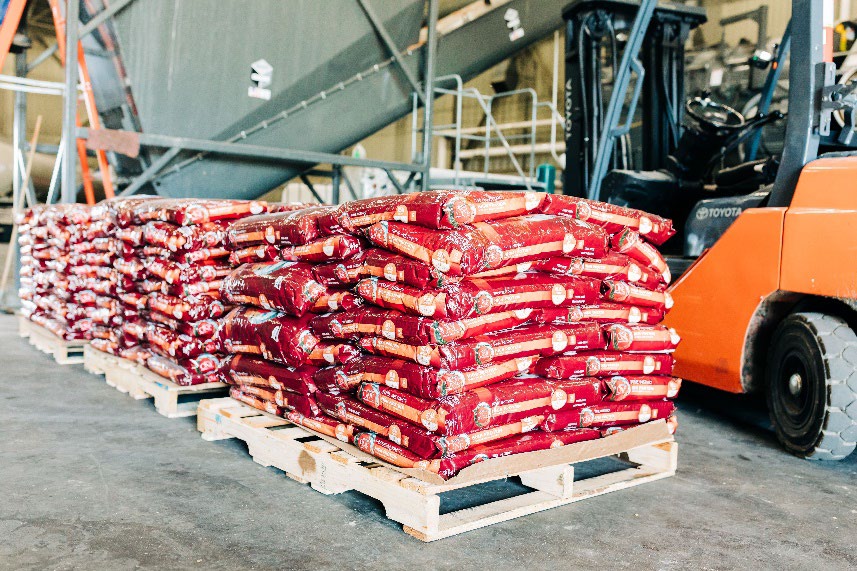 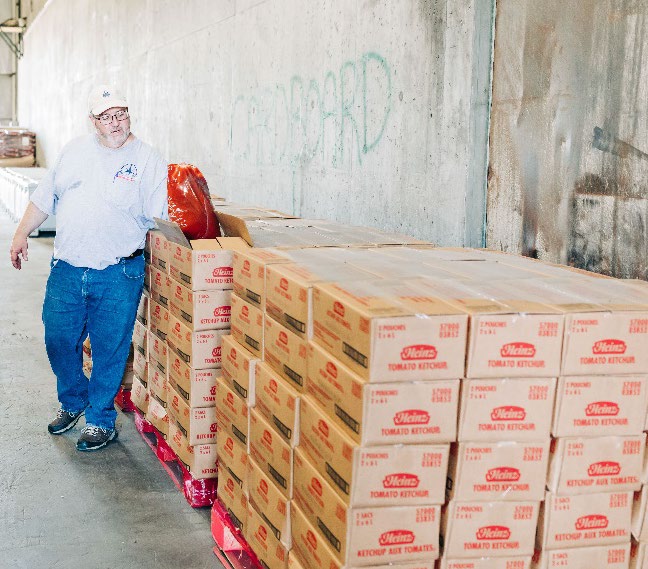 |
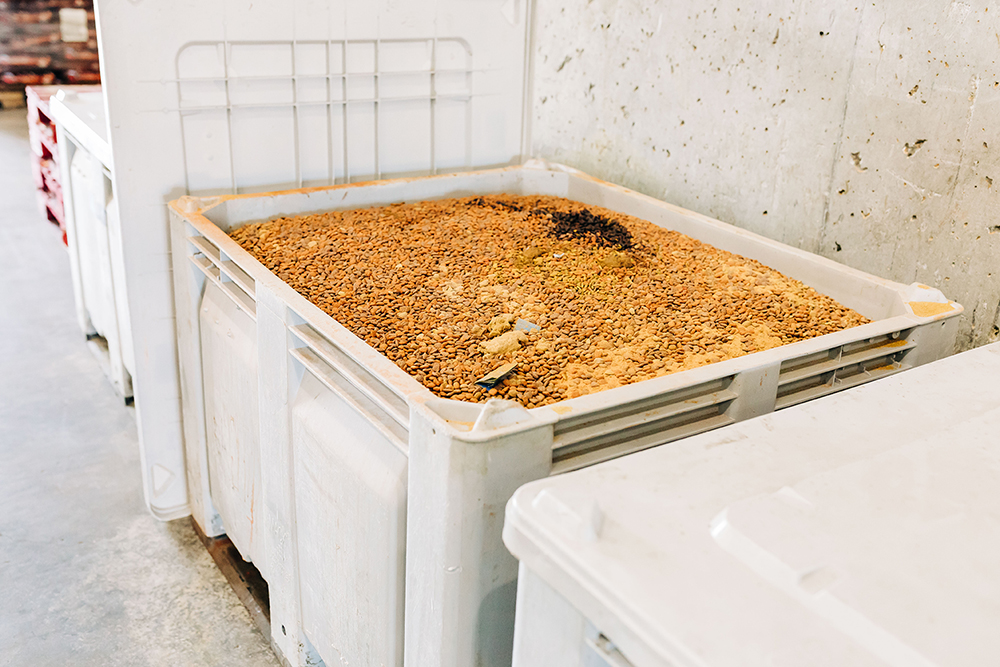 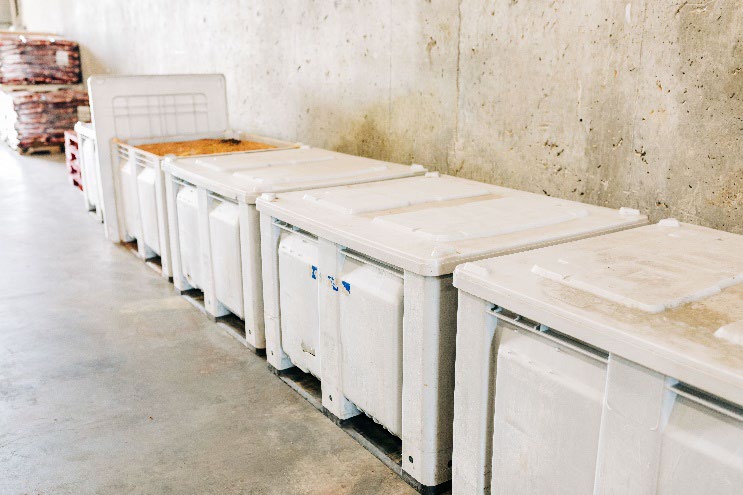 |
Pallets and totes of dry dog food and boxes of bottled ketchup waiting to be processed through the T42.
|
During the manufacturing process of packaged human and pet foods, it is not uncommon for some product to be rejected. The reasons could vary from health concerns or food quality standards to technicalities such as incorrect labeling. The product must be destroyed as it has been declared unsuitable for consumption. Historically these rejects would end up in a landfill as there was no other viable option. But MORC gives the manufacturers the better option not only reducing the organic waste volume landfilled but also of deriving benefit from the wastes.
|
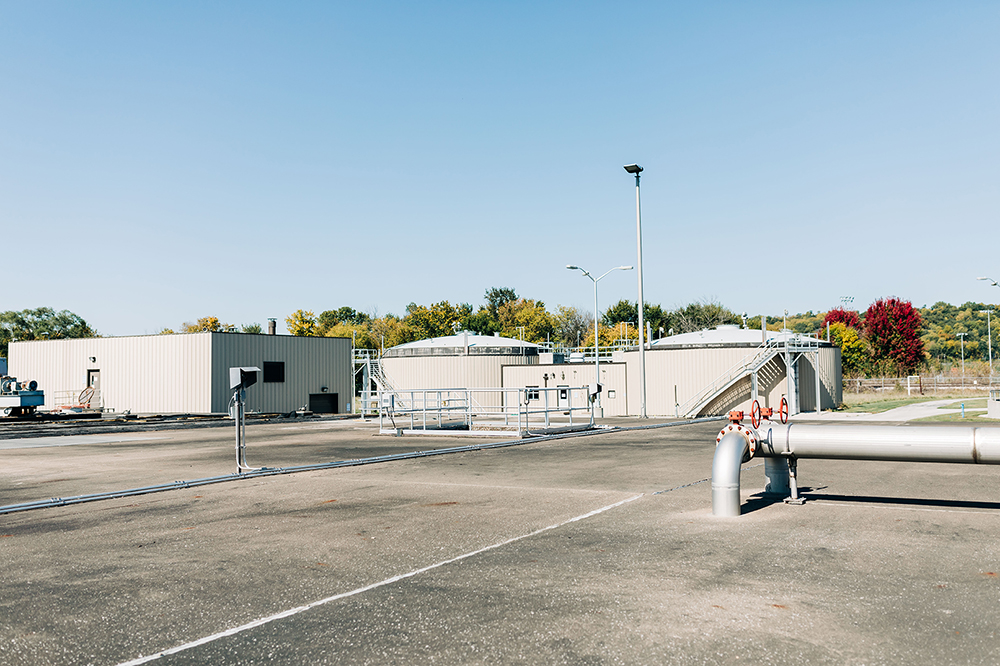 |
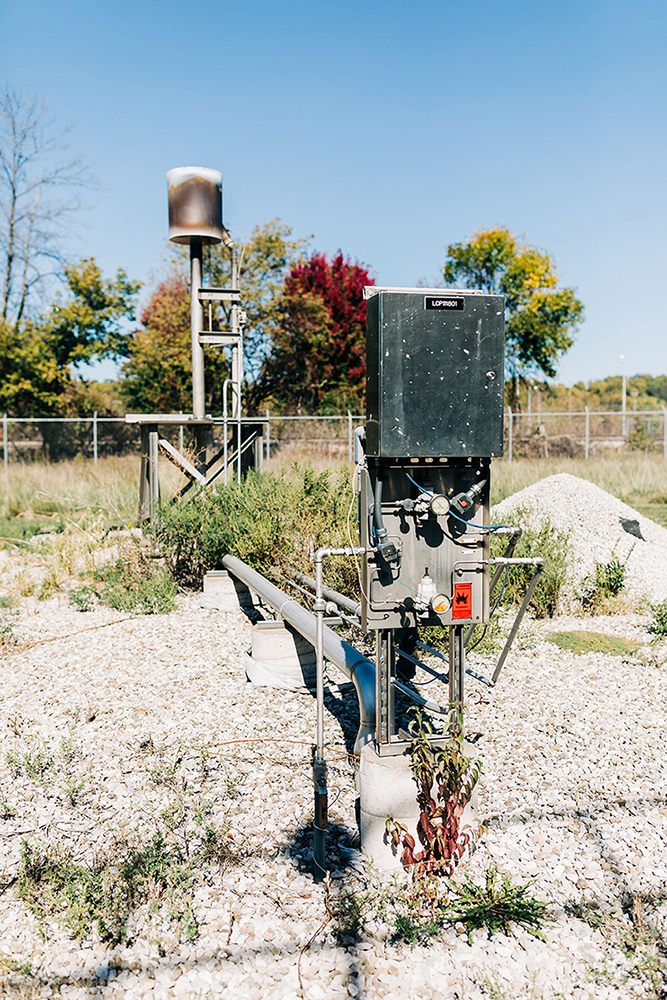 |
The plant’s two anerobic digesters. The bacteria in the digesters break down organic matter by co-digestion, which occurs when anaerobic digestion is used to break down multiple forms of organic waste in one anaerobic digester. In addition to human waste, the bacteria feeds on fats, oils and greases (FOG) from restaurants, and food waste food from homes, businesses and industries.
|
The digestion process generates biogas that is mostly methane, the primary component of natural gas. It is currently being flared off. Muscatine’s Water and Resource Recovery Facility (WRRF) Director Jon Koch, has a long-term goal of increasing the volume of biogas produced by the digesters, converting it into compressed natural gas for pipeline injection and eventually using it as a carbon negative vehicle fuel.
|
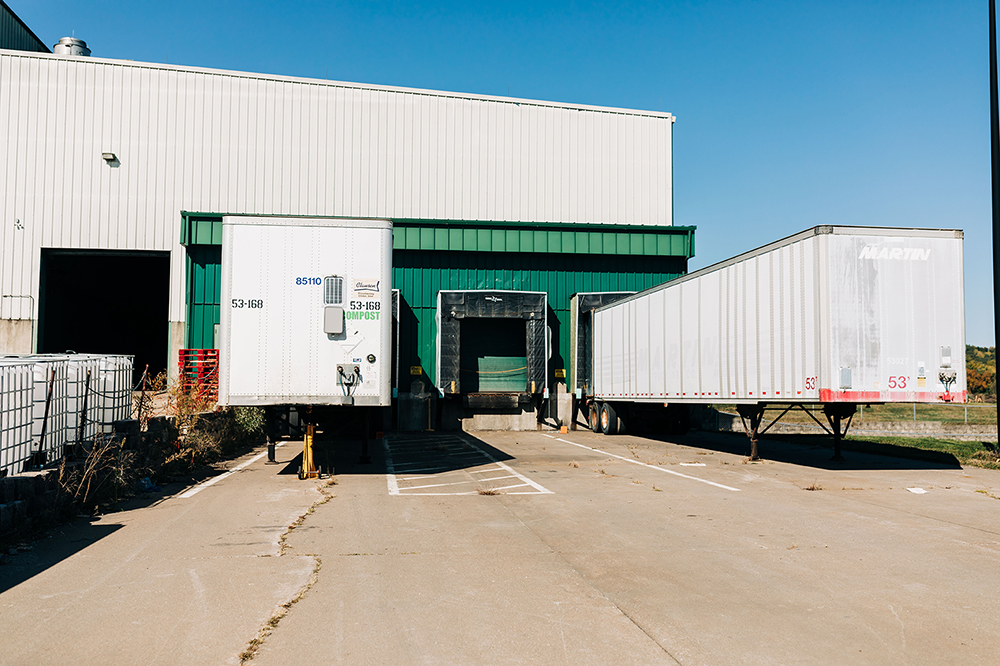 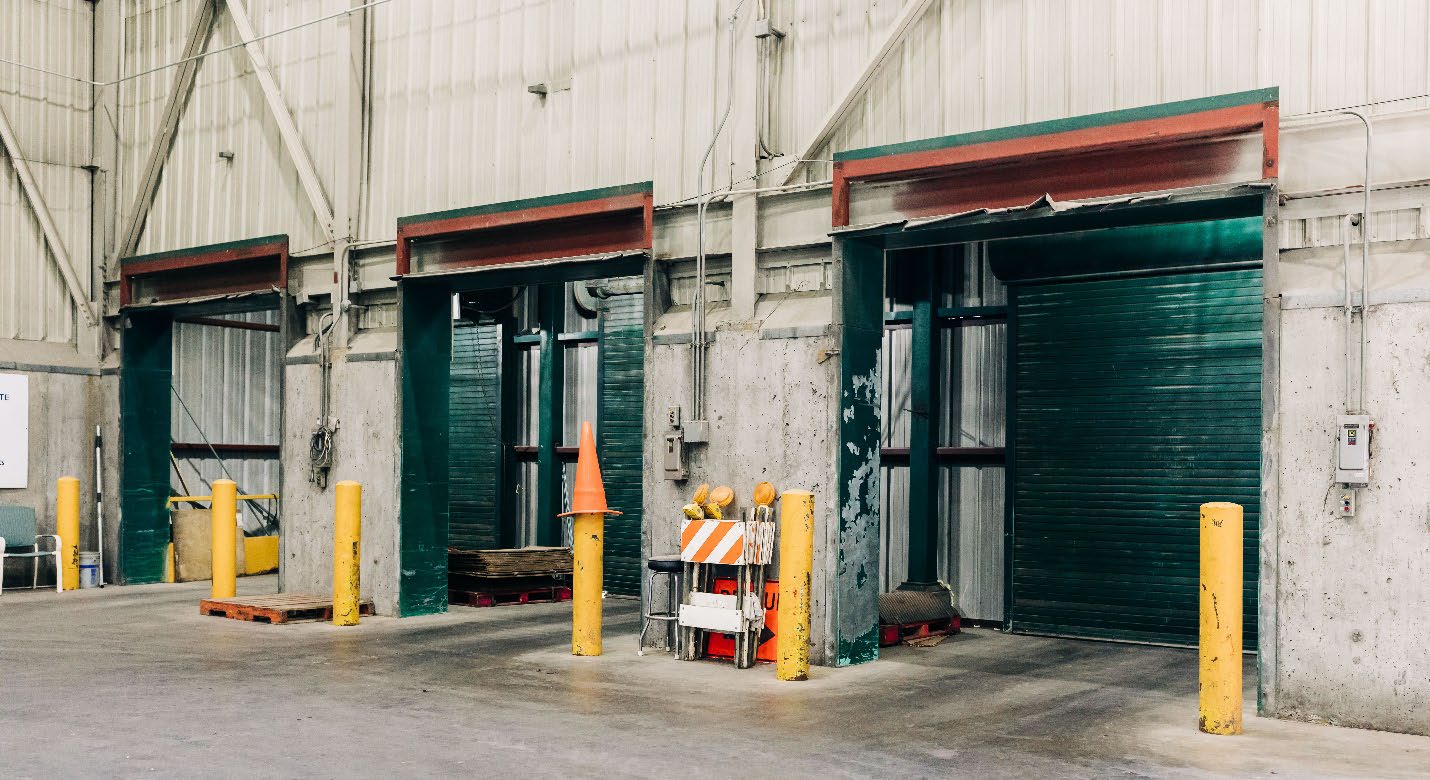 |
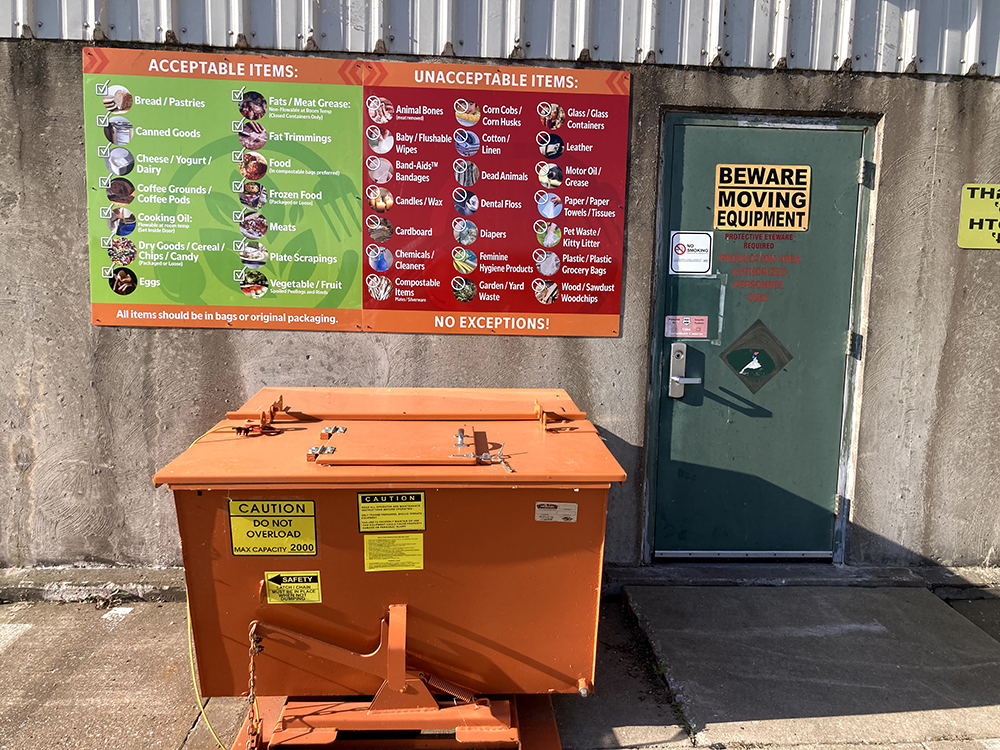 |
The recycled recycling center was already equipped with three large loading docks well suited for unloading organic waste.
|
Over 9 tons of food waste have been collected in a free collection bin available to residents, restaurants and food banks. The recycling center has the full support of the City of Muscatine, residents and businesses. Multiple articles, broadcasts, webpages, presentations tours and webinars have spread the word that the Muscatine is on the cutting edge for municipal organic waste processing.
|
|