2021 Excellence in Environmental Engineering and Science® Awards Competition Winner
Grand Prize - Small Firms
Last Dollar PUD Homeowner Association Wastewater Treatment System Improvement Project
Entrant: AquaWorks DBO, Inc. Engineer in Charge: Adam Sommers, P.E. Location: Telluride, Colorado Media Contact: Adam Sommers, P.E.
Entrant Profile
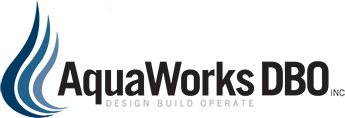
Introduction & Problem Statement
The Last Dollar PUD Association owns and operates a domestic wastewater treatment plant in Telluride, Colorado, serving a community of 29 homes. A new plant was required to treat 7,830 gallons per day and 23 pounds per day of BOD.
The association’s wastewater treatment plant faced significant challenges related to the condition of the current facility, the timing, land area available for construction, and cost. The existing facility consisted of a 45-year-old Case Cotter packaged wastewater treatment plant that had exceeded the end of its design life. The existing facility was failing and needed to be replaced quickly. In fact, previous leaks had occurred. However, it was necessary for the old plant to remain operational until the new plant was online.
In addition, there was extremely limited land available for construction at the site and slope stability issues left only 0.5 acres available for this project. The current facility was already on unstable ground.
AquaWorks was challenged with engineering and implementing a solution that would fit in the small construction footprint onsite, allow the existing facility to remain operational while the new plant was constructed, and implement a system as quickly as possible at high elevations, all at the lowest cost possible.
Project Description
Failing concrete tanks
Location of the old facility and site topography
Unloadong of precast treatment tanks
Newterra containerized MBR System
MBR treatment tanks
Land disturbance of 0.5 acres
Automated systems
Complexity
Several factors compounded the association’s problem, with the most significant issues being the potential failure of the treatment basin before improvements could be installed and the inability for the homeowners to afford the improvements.
During the original installation of the treatment tank, reinforcing steel was not incorporated into the cast in place concrete. The old and weak condition of the tank had already resulted in several leaks. The failure of the basin had been temporarily mitigated with additional reinforcement and secondary containment. However, structural problems were likely to escalate, possibly resulting in a major failure. The association did not have time to wait more than a year to have a new system operational.
Construction challenges due to the elevation (8,750 feet) and topography of the site complicated the project further. There is extremely limited land available for construction at the site and slope stability was an issue. The existing treatment plant was already exhibiting substantial distress from settlement and slope stability. The site is mostly rock and the available space in between the existing facility, a rock outcropping and a steep slope is very limited.
Originality & Innovation
AquaWorks worked to engineer an affordable system that could be fabricated offsite, installed and operational in a few months within less than half an acre.
The most original and innovative component not seen in conventional projects was the use of a prefabicrated, turnkey membrane bioractor (MBR). This system is delivered in a shipping container, ready for operations. Building an entire wastewater treatment system offsite in a container and delivering it onsite, ready for installion is truly unique. This approach allowed for the design, permitting, fabrication and construction to occur simultaneoulsy with minimal land disturbance. In addition, there was no downtime in treatment because the existing treatment system remained operational during the construction of the new facility.
The MBR produces consistent effluent quality better than other available technologies such as conventional activated sludge, rotating biological contactor, moving bed bioreactor, sequencing batch reactor, lagoon, and oxidation ditches because of the ultrafilter at the end of the process.
Because Newterra offers this technology as a made to order containerized system, no further building was required to house the treatment equipment. The equipment installation process was greatly simplified with this approach as it does not require the onsite contractor to complete the specialized process equipment, electrical, and controls work.
Social & Economic Advancement
The Association funds the WWTP capital and operational costs through monthly HOA dues and does not charge a separate sewer fee.
Prior to AquaWorks involvement, the association was facing an unaffordable 20-year present value project cost estimated between $2.2 million to $3.2 million dollars. Furthermore, those alternatives would have taken 2-3 years to complete. AquaWorks was able to design, build, and install a membrane bioreactor in 7 months for under $1 million.
Project Integration
Upgrading the facility improved the following:
Water Quality Improvement: The MBR technology removes more BOD, TSS, ammonia, total nitrogen, and phosphorus from the effluent, than the pre-existing facility and the other alternative treatment options. Most importantly, the new upgraded system quickly replaced the old system that could have failed and released untreated wastewater to the environment.
Land Protection: Land disturbance area was a major concern in this project. Due to topography and slope stability the small footprint of the containerized system was essential. Also, because of the high MLSS concentrations, less tank volume is required than other available technologies. This technology only required a half an acre, which is much less area than a traditional wastewater treatment facility.
Improved Air Quality: Based on AquaWorks’ pervious evaluations of the MBRs, the facility will be approximately 30% more energy efficient than the current facility. The new facility features high efficiency pumps and blowers, variable frequency drives (VFDs) tied to instrumentation, so the facility only aerates as much as is needs. The life cycle impact of energy efficiency result in reduced air pollution and greenhouse gas emissions from power generation.
Quality
The project represents a significant upgrade over the previous facility. The new facility is more efficient and has far more process control capabilities than the existing facility. The new facility has PLCs to control most treatment equipment and processes. Instrumentation, such as dissolved oxygen sensors are included to regulate how much air is supplied to the process, reducing wasted energy costs. Chemical feed systems are configured to dose proportional to the flow treated at the plant. Telemetry is installed to allow operators to access the plant’s control panel remotely. A generator with an automatic transfer switch will provide a backup source of power in the event primary electrical source fails.
Click images to enlarge in separate window.
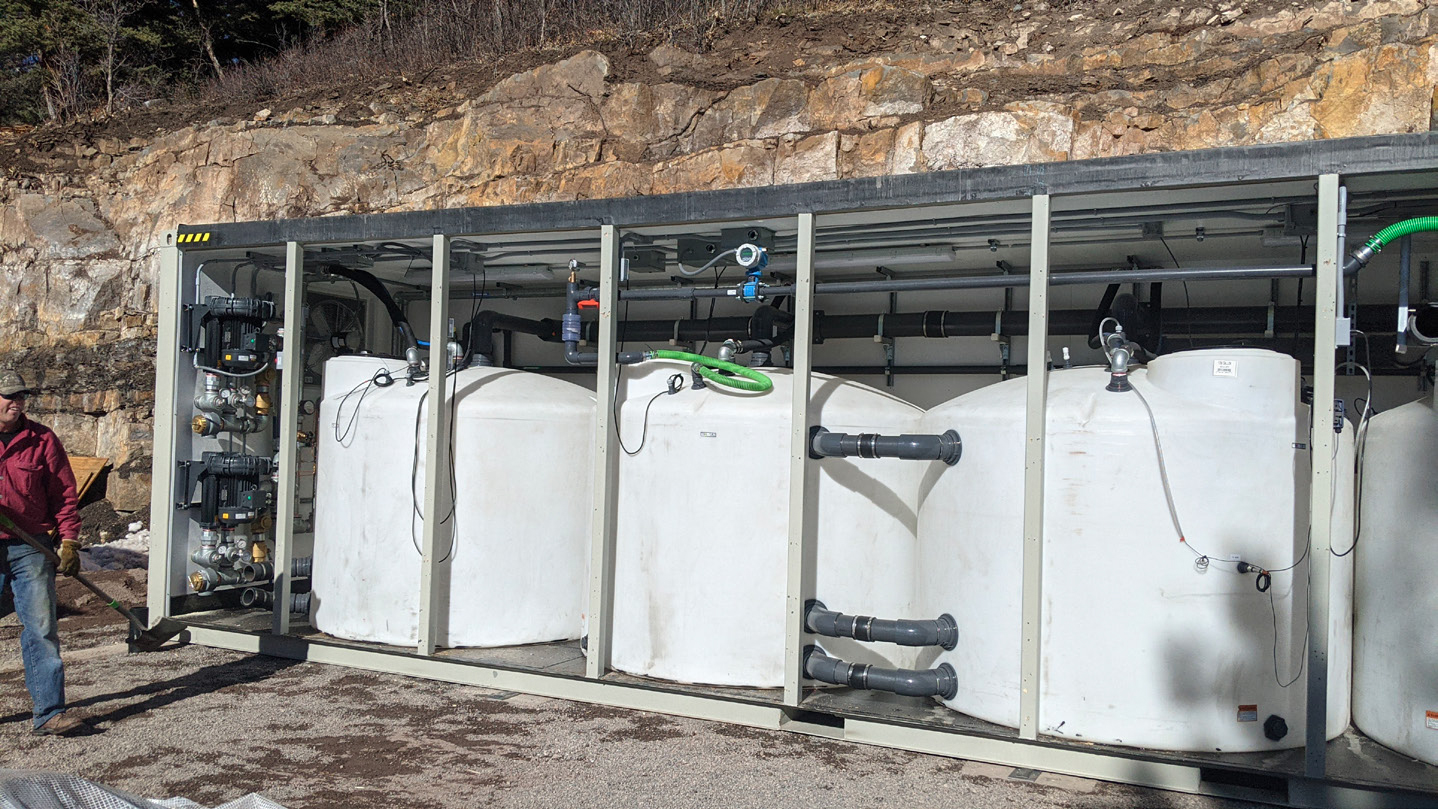 |
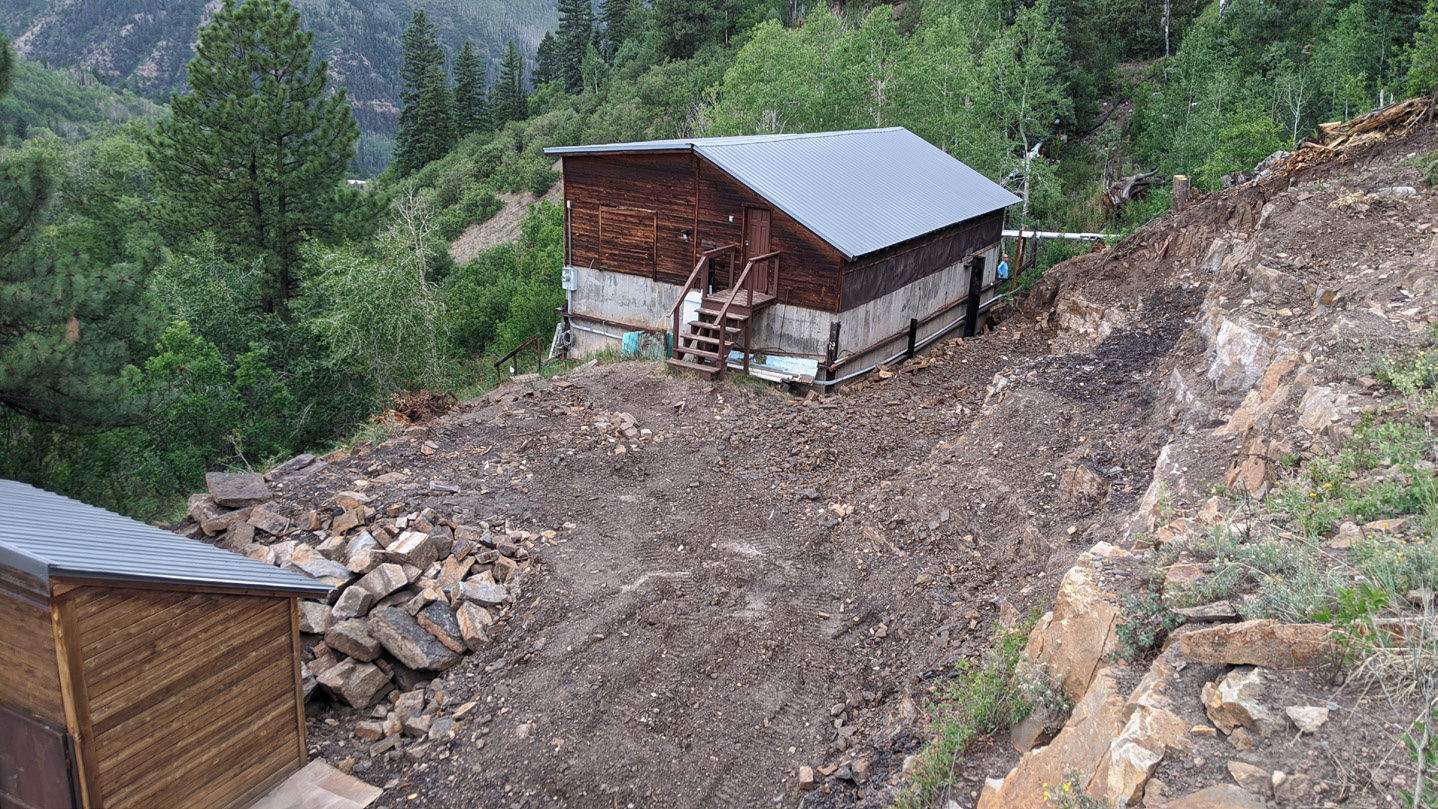 |
Aerobic and anoxic tanks come installed in the containers
|
Availability of space was limited
|
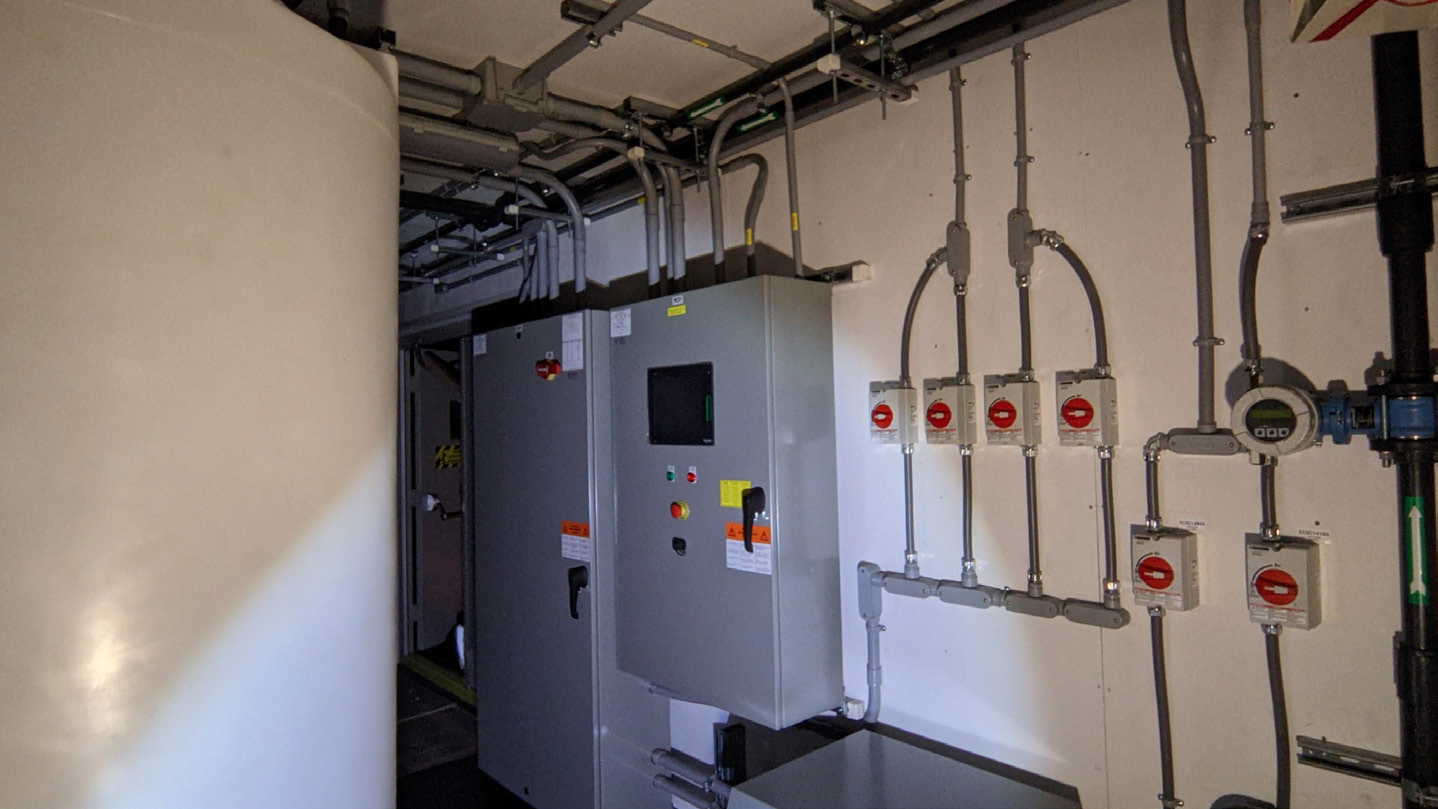 |
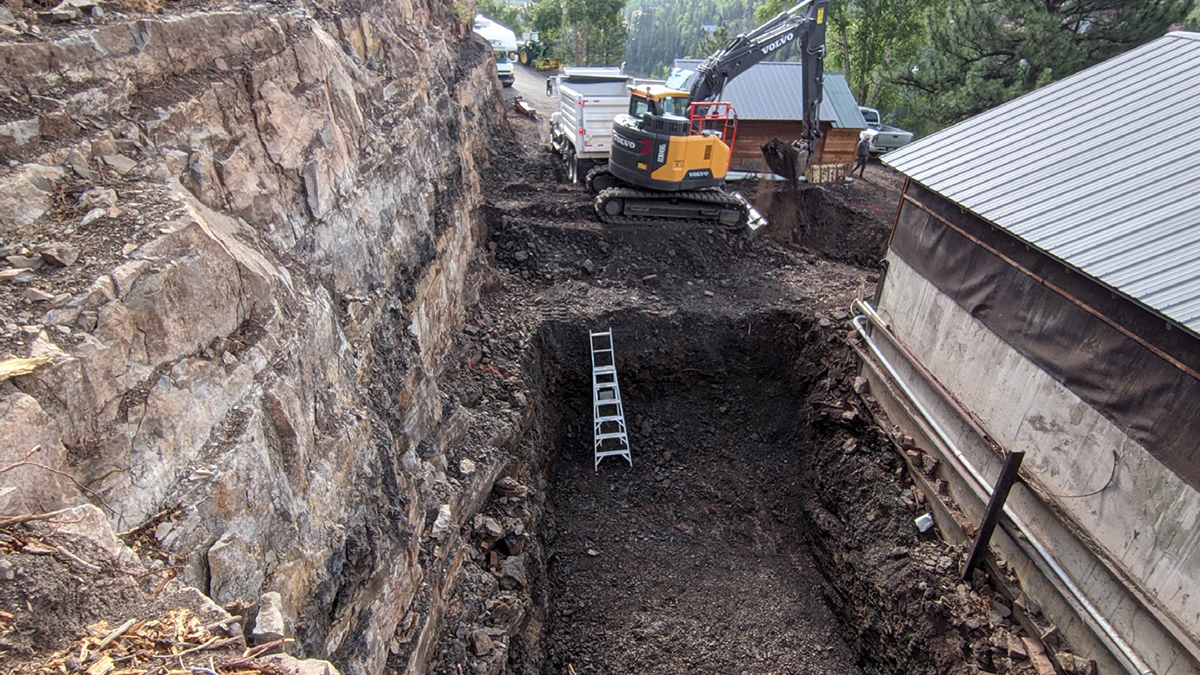 |
Electrical panels
|
Excavation for influent EQ tank
|
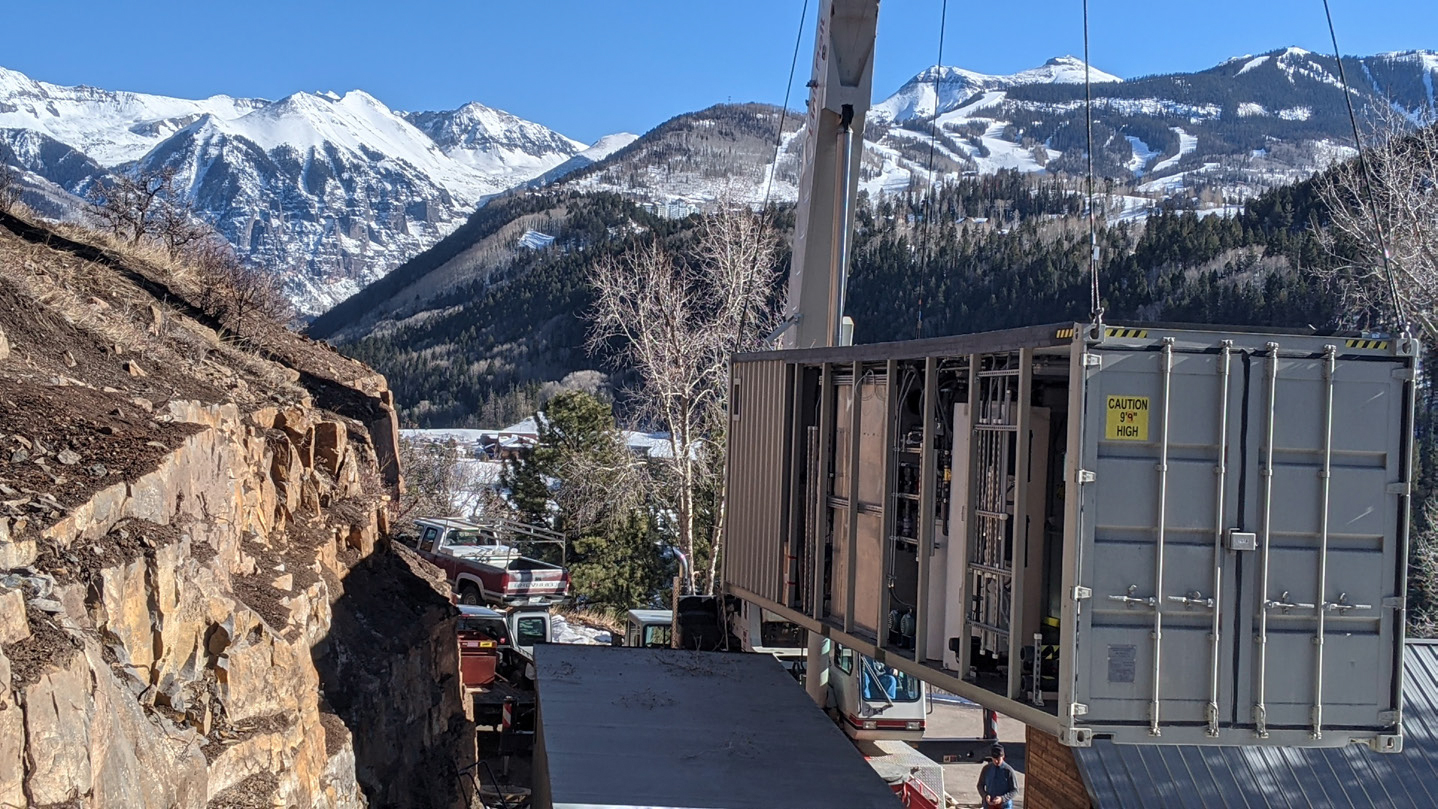 |
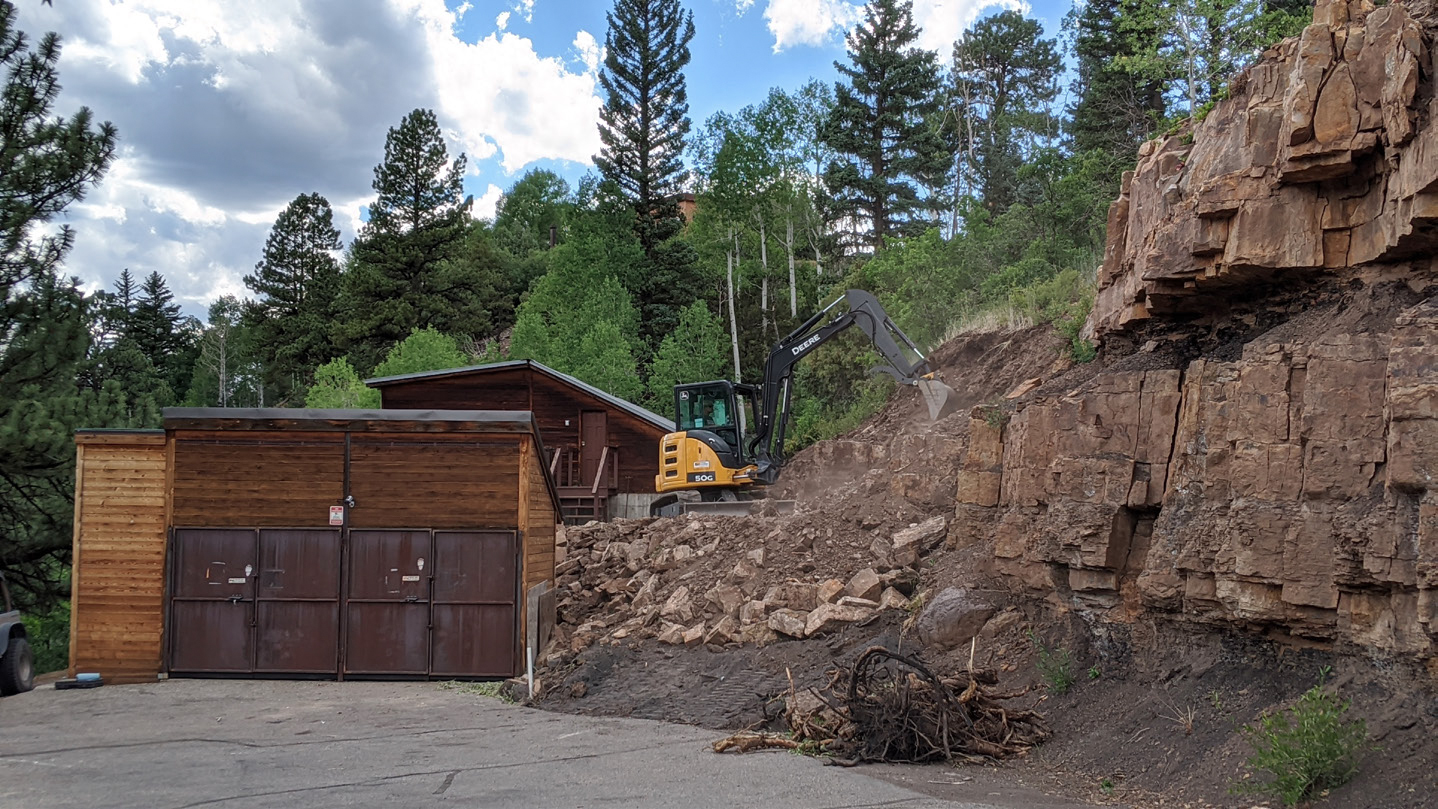 |
Facility serves a community near the Telluride Ski Resort
|
Facility was installed between a rock and a hard place
|
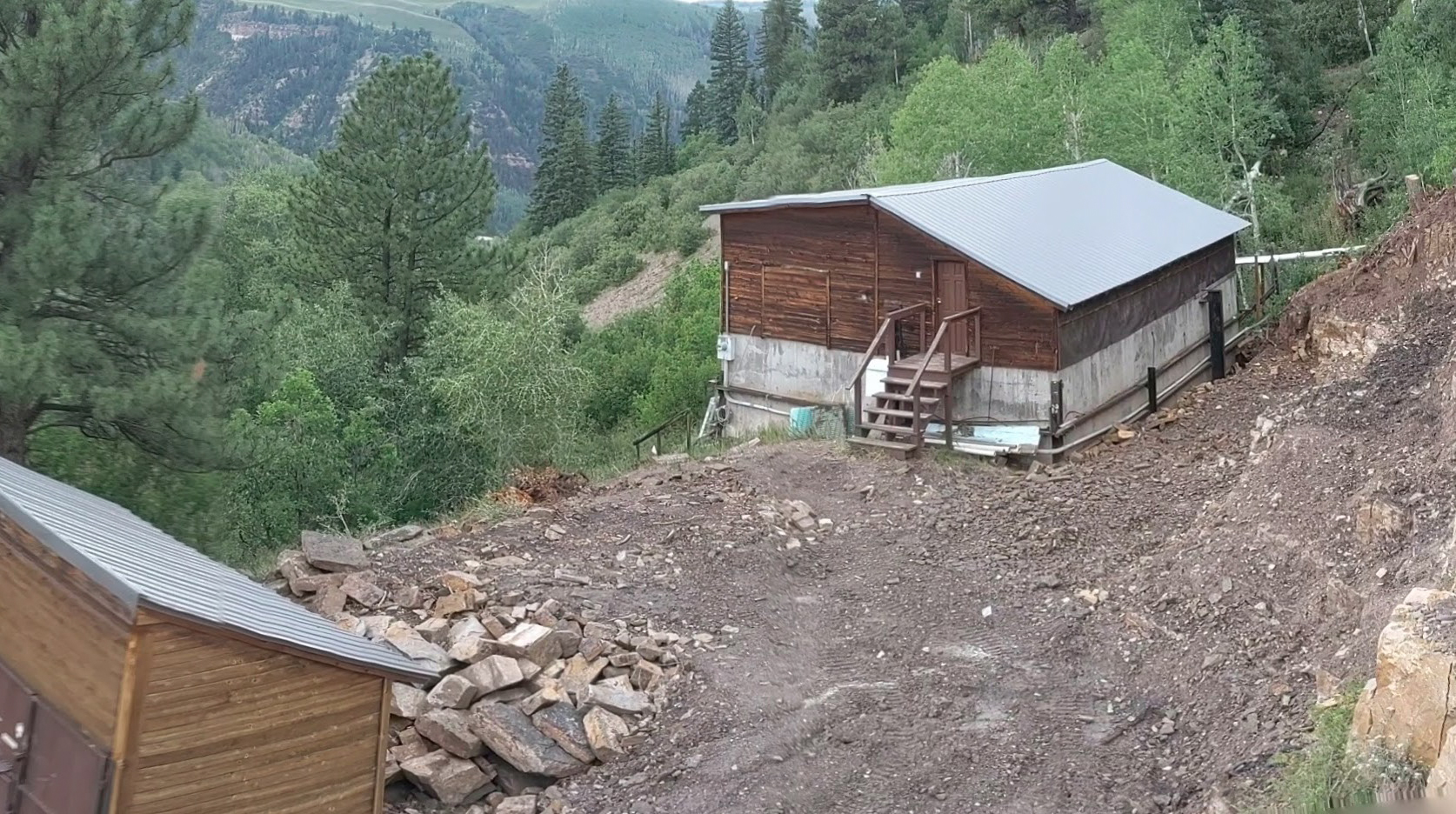 |
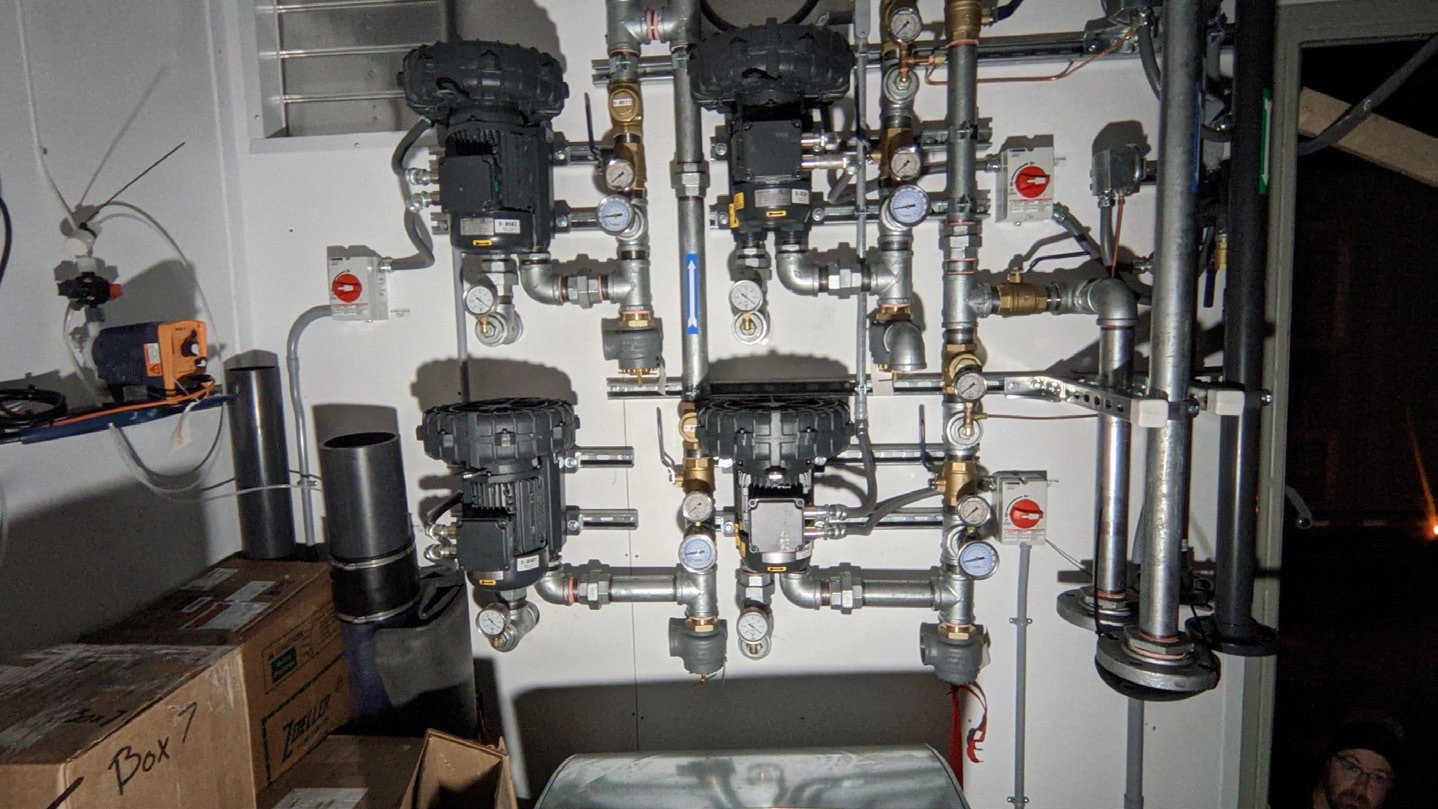 |
Predisturbed conditions
|
Pre-installed blower system
|
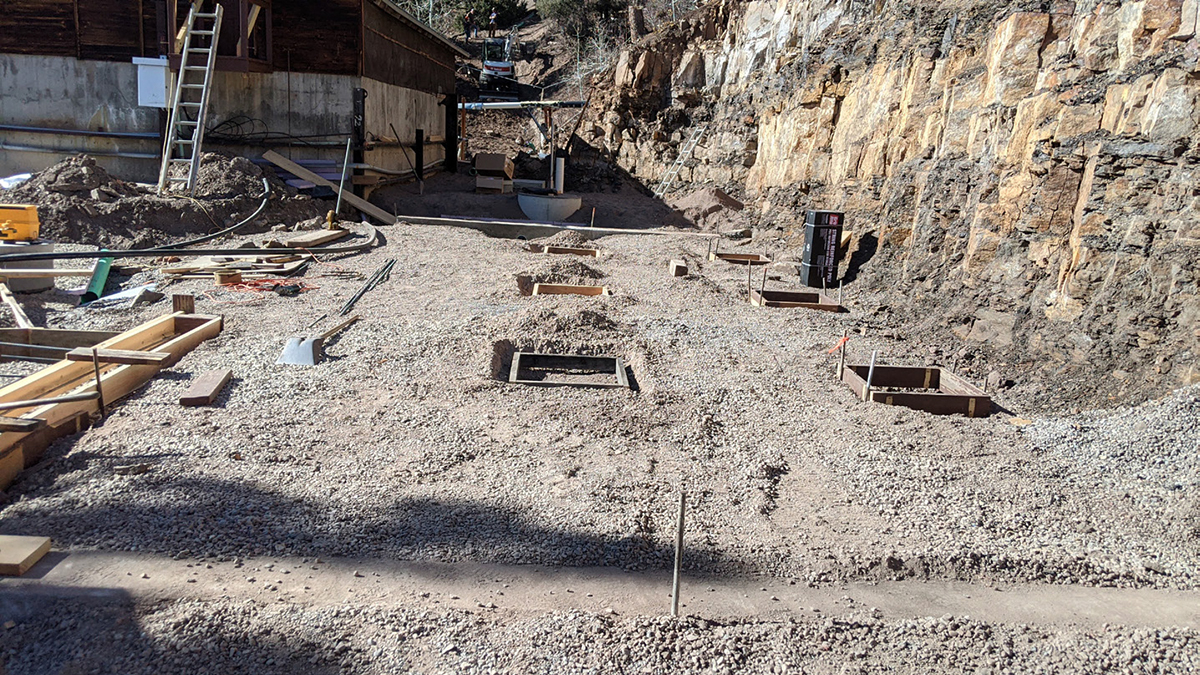 |
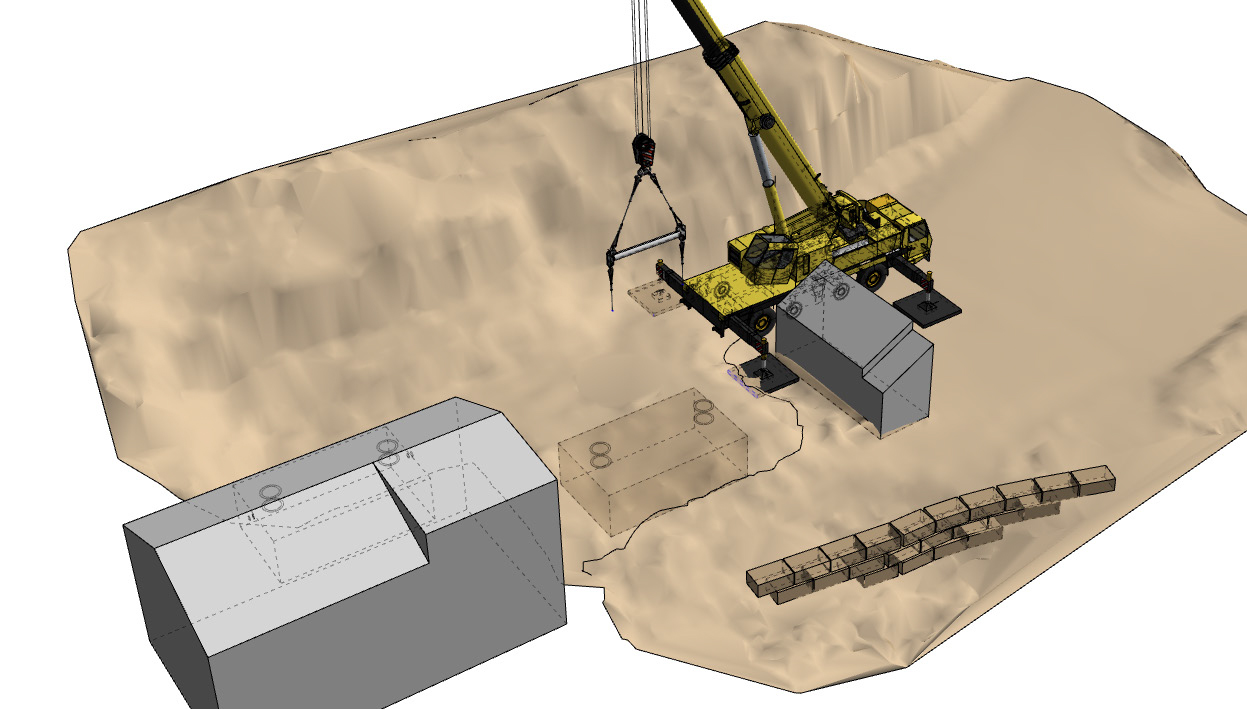 |
Site preparation for treatment containers
|
Site work rendering
|
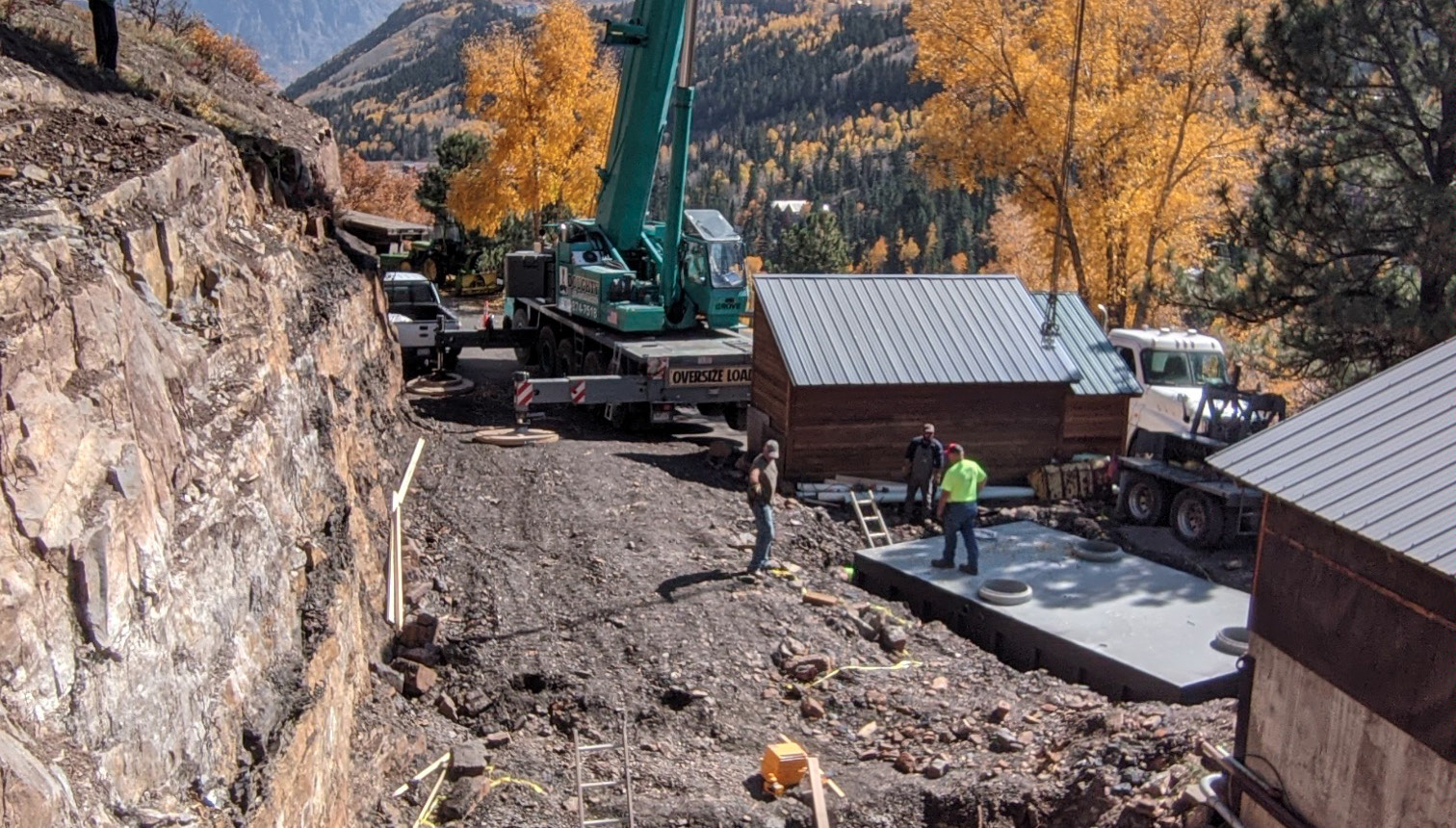 |
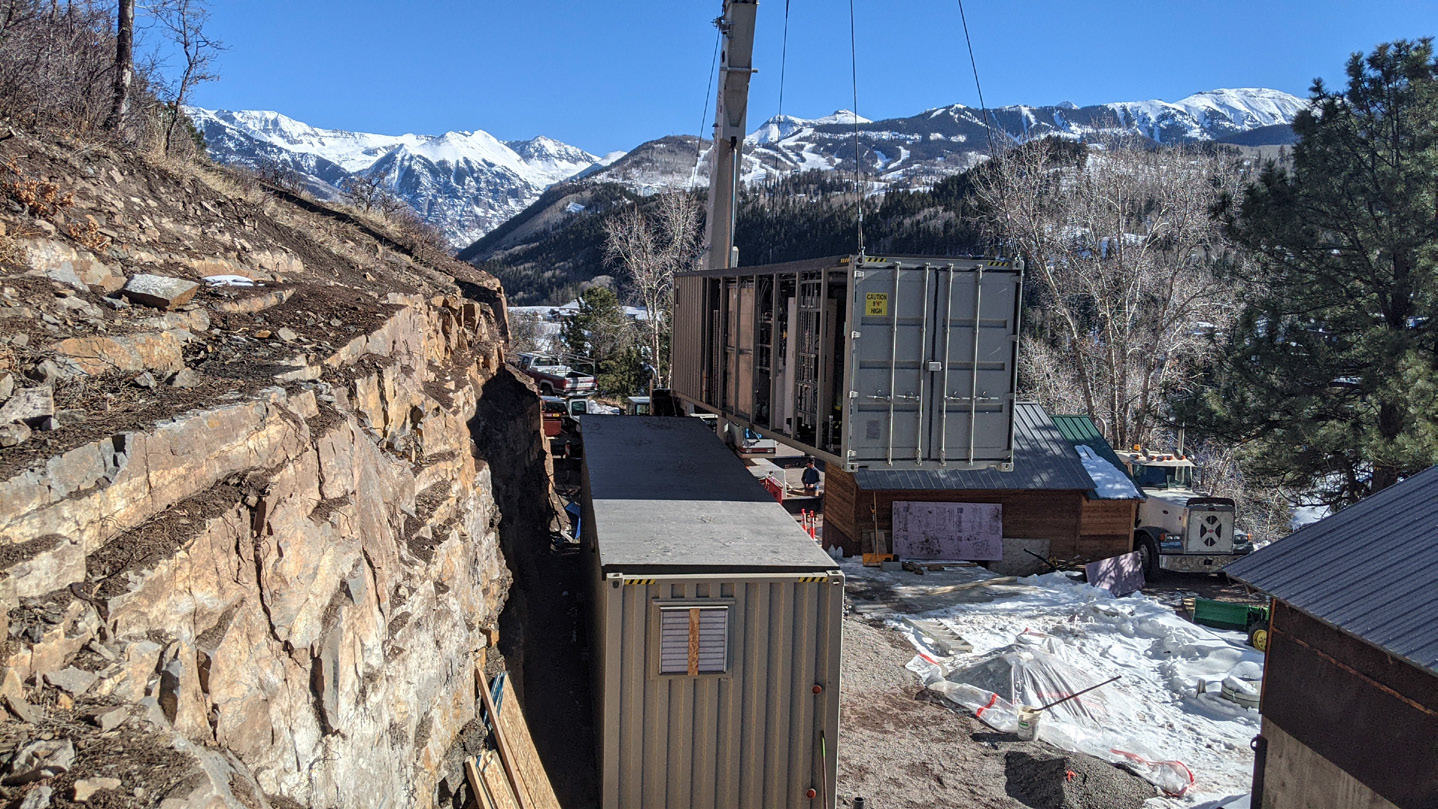 |
Unloading of precast process tanks
|
Unloading of treatment containers
|
|